The temperature zones of a kiln are critical for understanding its operation and functionality, particularly in processes like sintering, firing ceramics, or other high-temperature applications. Kilns are designed with specific temperature zones to ensure controlled heating, sintering, and cooling of materials. These zones typically include a pre-heating zone, a high-temperature sintering or firing zone, and a cooling zone. Each zone serves a distinct purpose, such as removing organic materials, bonding particles through diffusion, or preventing oxidation during cooling. The exact temperature ranges and zones depend on the type of kiln (e.g., rotary, tunnel, or laboratory kilns) and the materials being processed. For example, rotary kilns may require flame temperatures of up to 2000 °C to achieve sintering zone temperatures of around 1450 °C, while laboratory kilns can operate across a broader range, from 100 to 1700 °C. Understanding these zones is essential for optimizing kiln performance and ensuring the desired outcomes for the materials being processed.
Key Points Explained:
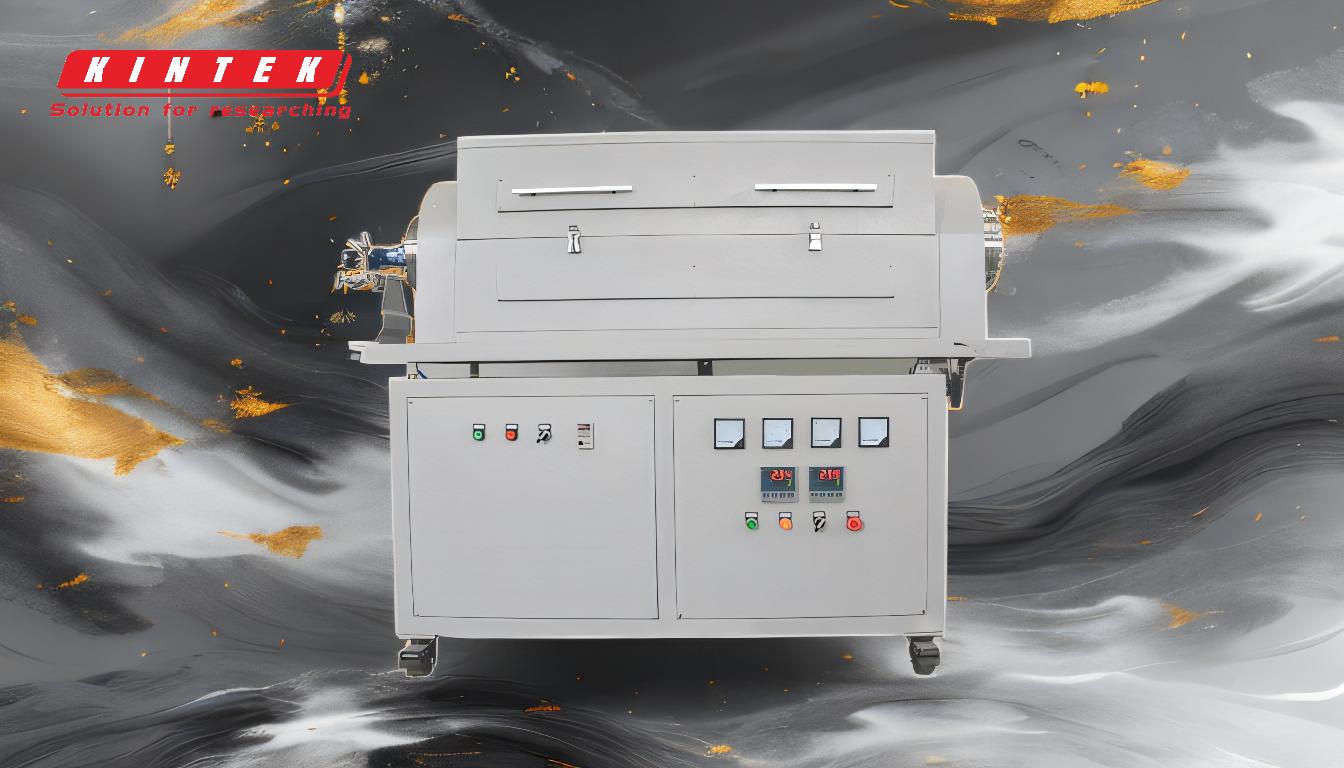
-
General Structure of Kiln Temperature Zones:
- Kilns are typically divided into three main temperature zones: pre-heating, sintering (or high-temperature heating), and cooling.
- Each zone has a specific function and temperature range tailored to the material and process requirements.
-
Pre-Heating Zone:
- Purpose: Removes lubricants, organic materials, and moisture from the material before high-temperature processing.
- Temperature Range: Varies depending on the kiln type and material but generally ranges from ambient temperature to several hundred degrees Celsius.
- Example: In tunnel kilns, this zone ensures the removal of organic binders or lubricants before sintering.
-
Sintering or High-Temperature Zone:
- Purpose: Facilitates the bonding of particles through diffusion, melting, or chemical reactions to create a solid structure.
- Temperature Range: Typically ranges from 1000 °C to 2000 °C, depending on the material and kiln type.
- Rotary kilns: Sintering zone temperatures are around 1450 °C, requiring flame temperatures of approximately 2000 °C.
- Laboratory kilns: Can achieve temperatures up to 1700 °C.
- Example: In sintering furnaces, this zone reduces oxides and bonds powder particles through diffusion.
-
Cooling Zone:
- Purpose: Allows the material to cool gradually to prevent thermal shock, cracking, or oxidation.
- Temperature Range: Starts at the sintering temperature and decreases to ambient temperature.
- Example: In tunnel kilns, the cooling zone ensures controlled cooling while preventing air ingress and oxidation.
-
Variations by Kiln Type:
-
Rotary Kilns:
- Flame temperatures of about 2000 °C are required to achieve sintering zone temperatures of 1450 °C.
- Includes pre-heating and high-temperature heating zones, each with multiple sub-zones for precise temperature control.
-
Tunnel Kilns:
- Three distinct zones: preheat, sintering, and cooling.
- The preheat zone removes organic materials, the sintering zone fuses particles, and the cooling zone ensures gradual cooling.
-
Laboratory Kilns:
- Capable of operating across a wide temperature range (100–1700 °C).
- Often used for smaller-scale or experimental processes with precise temperature control.
-
Rotary Kilns:
-
Importance of Temperature Control:
- Kilns provide excellent control over heat rise and fall, which is critical for achieving consistent results.
- Precise temperature management prevents defects, ensures material integrity, and optimizes energy efficiency.
- Example: In ceramic firing, improper cooling can lead to cracking or warping, while insufficient sintering can result in weak structures.
-
Material-Specific Considerations:
- Different materials require specific temperature profiles and zones.
- Ceramics: Require high temperatures for vitrification and bonding.
- Metals: Sintering temperatures depend on the alloy and particle size.
- Organic materials: Lower temperatures are needed to avoid combustion or degradation.
- Example: In sintering furnaces, the temperature zones are tailored to the material's melting point and bonding mechanisms.
- Different materials require specific temperature profiles and zones.
-
Refractory Materials in Kilns:
- Kilns are constructed from refractory materials that can withstand high temperatures without melting.
- These materials ensure the kiln can contain heat and maintain stable temperature zones.
- Example: Refractory bricks or linings are used to insulate the kiln and protect its structure during high-temperature operations.
By understanding the temperature zones of a kiln, users can optimize processes, select appropriate kiln types, and achieve desired material properties. Whether for industrial applications or laboratory experiments, the precise control of these zones is essential for successful outcomes.
Summary Table:
Zone | Purpose | Temperature Range |
---|---|---|
Pre-Heating Zone | Removes lubricants, organic materials, and moisture. | Ambient to several hundred °C |
Sintering Zone | Bonds particles through diffusion, melting, or chemical reactions. | 1000–2000 °C (varies by kiln type and material) |
Cooling Zone | Prevents thermal shock, cracking, or oxidation during gradual cooling. | Sintering temperature to ambient temperature |
Need help optimizing your kiln's temperature zones? Contact our experts today for tailored solutions!