Thermal evaporation is a widely used technique in thin film deposition, particularly in the fabrication of devices like OLEDs, solar cells, and thin-film transistors. It operates on the principle of heating a solid material in a high vacuum chamber until it vaporizes, creating a vapor stream that travels to and adheres to a substrate, forming a thin film. This method is favored for its simplicity, ability to deposit high-purity films, and compatibility with a variety of materials. The process involves resistive heating or electron beam heating to achieve the necessary vapor pressure, and the vacuum environment ensures minimal contamination and efficient deposition. Thermal evaporation is versatile, capable of depositing both metallic and non-metallic layers, making it essential in advanced manufacturing and research applications.
Key Points Explained:
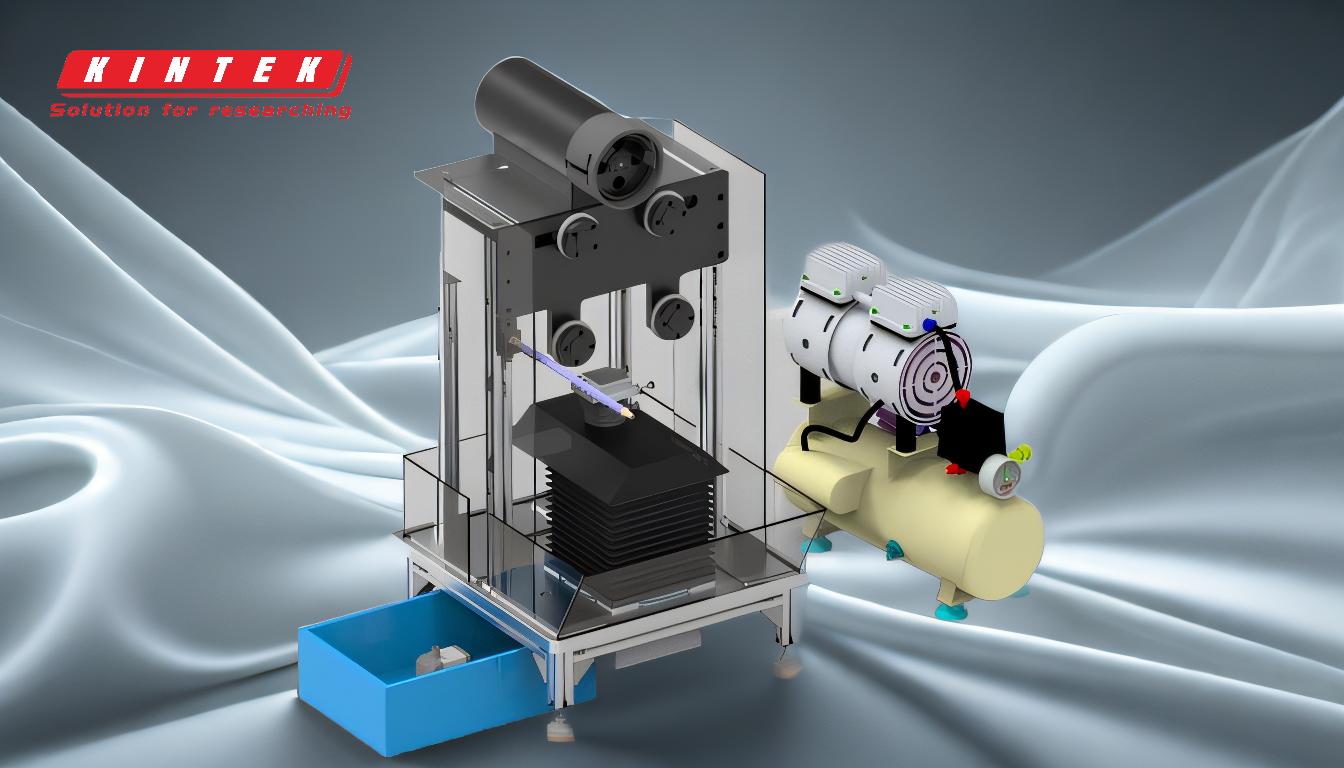
-
Principle of Thermal Evaporation:
- Thermal evaporation is a form of physical vapor deposition (PVD) where a solid material is heated to its evaporation point in a high vacuum chamber.
- The material vaporizes, creating a vapor stream that travels through the vacuum and deposits onto a substrate, forming a thin film.
- This process relies on achieving sufficient vapor pressure, which is easier in a vacuum due to the lack of atmospheric interference.
-
Equipment and Setup:
- A high vacuum chamber is essential to minimize contamination and ensure the vapor stream travels unimpeded.
- Heating is typically achieved using a resistive heating element (e.g., tungsten filament) or an electron beam evaporator.
- The substrate is positioned in the chamber to receive the vapor stream and form the thin film.
-
Advantages of Thermal Evaporation:
- High Purity: The vacuum environment reduces contamination, resulting in high-purity films.
- Versatility: Suitable for depositing a wide range of materials, including metals, semiconductors, and insulators.
- Simplicity: The process is straightforward and does not require complex chemical reactions.
- Precision: Allows for precise control over film thickness and uniformity.
-
Applications:
- OLEDs and Thin-Film Transistors: Used to deposit metallic contact layers and other functional layers in electronic devices.
- Solar Cells: Deposits thin films of materials like indium for efficient light absorption and charge transport.
- Wafer Bonding: Thick indium layers can be deposited for bonding applications in semiconductor manufacturing.
-
Types of Heating Methods:
- Resistive Heating: Uses a tungsten filament or boat to heat the material. Suitable for materials with lower melting points.
- Electron Beam Evaporation: Focuses an electron beam on the material, allowing for higher temperatures and the evaporation of refractory materials.
-
Process Steps:
- Material Loading: The target material is placed in the heating element or crucible.
- Vacuum Creation: The chamber is evacuated to a high vacuum to eliminate contaminants.
- Heating and Evaporation: The material is heated until it vaporizes, creating a vapor stream.
- Deposition: The vapor stream travels to the substrate and condenses into a thin film.
- Cooling and Removal: The substrate is cooled, and the chamber is vented to remove the coated substrate.
-
Challenges and Considerations:
- Material Compatibility: Not all materials are suitable for thermal evaporation due to differences in melting points and vapor pressures.
- Uniformity: Achieving uniform film thickness can be challenging, especially for large substrates.
- Heat Sensitivity: Some substrates may be sensitive to the heat generated during the process.
-
Comparison with Other Deposition Techniques:
- Sputtering: Unlike sputtering, which uses energetic ions to eject material from a target, thermal evaporation relies solely on heat.
- Chemical Vapor Deposition (CVD): Thermal evaporation is a physical process, whereas CVD involves chemical reactions to form the film.
-
Future Trends:
- Hybrid Techniques: Combining thermal evaporation with other methods like sputtering or CVD to enhance film properties.
- Advanced Materials: Expanding the range of materials that can be deposited using thermal evaporation, including complex oxides and organic compounds.
- Automation: Increasing automation to improve process control and reproducibility.
Thermal evaporation remains a cornerstone of thin film deposition due to its simplicity, effectiveness, and adaptability to various applications. As technology advances, this technique continues to evolve, enabling the development of cutting-edge devices and materials.
Summary Table:
Aspect | Details |
---|---|
Principle | Heats solid material in a vacuum until it vaporizes, forming a thin film. |
Heating Methods | Resistive heating or electron beam heating. |
Advantages | High purity, versatility, simplicity, and precision. |
Applications | OLEDs, solar cells, thin-film transistors, wafer bonding. |
Challenges | Material compatibility, uniformity, and heat sensitivity. |
Future Trends | Hybrid techniques, advanced materials, and automation. |
Discover how thermal evaporation can enhance your manufacturing process—contact us today for expert guidance!