The tolerance of a muffle furnace refers to its ability to maintain a consistent temperature within a specified range during operation. This is critical for applications requiring precise thermal control, such as ashing, annealing, and heat treatment. Based on the references, the temperature control accuracy of a high-quality muffle furnace is typically ±1°C, while the temperature uniformity across the chamber is around ±2°C. These tolerances ensure reliable and repeatable results in high-temperature processes. The furnace's intelligent PID system further enhances temperature regulation, allowing for precise control over heating and cooling cycles.
Key Points Explained:
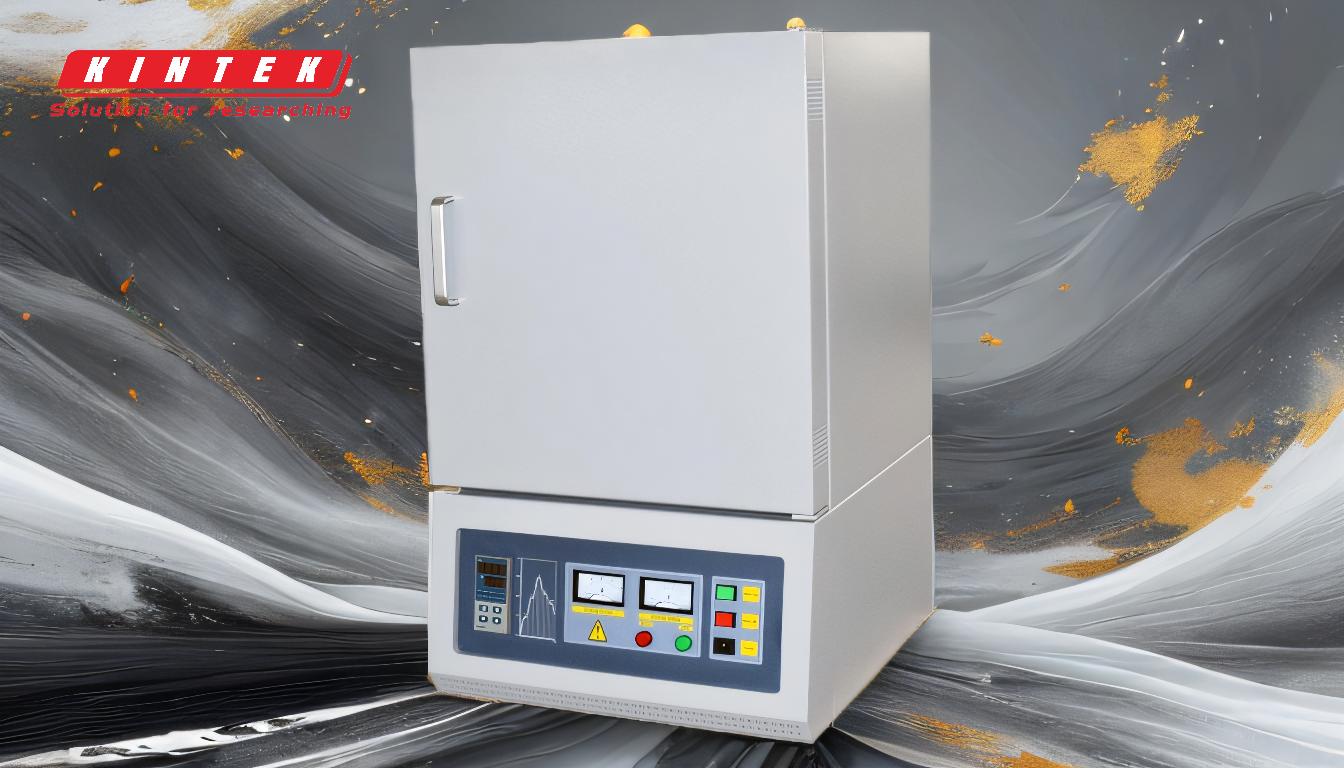
-
Temperature Control Accuracy:
- The temperature control accuracy of a muffle furnace is typically ±1°C. This means the furnace can maintain the set temperature within a 1°C range, ensuring precise thermal conditions for sensitive processes like annealing or ashing.
- This level of accuracy is achieved through advanced temperature regulation systems, such as PID (Proportional-Integral-Derivative) controllers, which continuously adjust the heating elements to minimize deviations from the target temperature.
-
Temperature Uniformity:
- The temperature uniformity across the furnace chamber is generally ±2°C. This ensures that the entire chamber maintains a consistent temperature, which is crucial for uniform heat treatment of materials.
- Uniformity is influenced by factors such as the design of the heating elements, insulation quality, and airflow within the chamber. High-quality muffle furnaces are engineered to minimize temperature gradients.
-
Intelligent PID System:
- Muffle furnaces often utilize an intelligent PID system to regulate temperature. This system allows for precise control over heating and cooling cycles, enabling the furnace to follow complex temperature programs (e.g., 30 stages of temperature rise and fall).
- The PID system adjusts the power supplied to the heating elements based on real-time feedback, ensuring rapid response to temperature changes and minimizing overshooting or undershooting.
-
Maximum Temperature and Heating Elements:
- The maximum temperature a muffle furnace can achieve depends on the type of heating elements used:
- Metallic wire heating elements: Typically support temperatures up to 1000°C to 1200°C.
- Silicon carbide heating elements: Can achieve temperatures up to 1600°C.
- Molybdenum disilicide heating elements: Allow for temperatures up to 1800°C.
- The choice of heating elements determines the furnace's suitability for specific high-temperature applications, such as metal melting or advanced material testing.
- The maximum temperature a muffle furnace can achieve depends on the type of heating elements used:
-
Applications and Importance of Tolerance:
- Muffle furnaces are used in a variety of applications, including ashing, annealing, heat treatment, and metal production. In these processes, maintaining precise temperature control and uniformity is critical to achieving consistent results.
- For example, in ashing, a deviation of even a few degrees could affect the accuracy of residue measurements. Similarly, in annealing, uneven temperatures could lead to inconsistent material properties.
-
Design and Construction:
- Muffle furnaces are constructed from heat-resistant materials with low thermal conductivity, ensuring efficient heat retention and minimizing energy loss.
- The interior chamber is designed to house and process materials uniformly, with insulation and heating elements strategically placed to maintain the desired temperature profile.
By understanding these key points, a purchaser can evaluate the suitability of a muffle furnace for their specific needs, ensuring that the chosen model meets the required temperature tolerances and performance standards.
Summary Table:
Key Feature | Specification |
---|---|
Temperature Control Accuracy | ±1°C |
Temperature Uniformity | ±2°C |
Heating Elements | Metallic wire (1000°C-1200°C), Silicon carbide (1600°C), Molybdenum disilicide (1800°C) |
Intelligent PID System | Enables precise control over heating and cooling cycles |
Applications | Ashing, annealing, heat treatment, metal production |
Need a muffle furnace with precise temperature control? Contact us today to find the perfect solution for your lab!