The two-roll mill mixing process is a mechanical method used to mix rubber or plastic materials with additives, such as dying agents or fillers, to achieve a uniform compound. The process involves two horizontally placed metal rolls rotating towards each other at different speeds, creating a friction ratio. This generates heat and shearing forces in the nip (gap) between the rolls, which stretch and break the internal macromolecular chains of the materials. The repeated squeezing and shearing actions disperse and mix the compositions evenly, resulting in a sheet-like compound. This process is essential for achieving the desired mastication or mixing state in rubber and plastic manufacturing.
Key Points Explained:
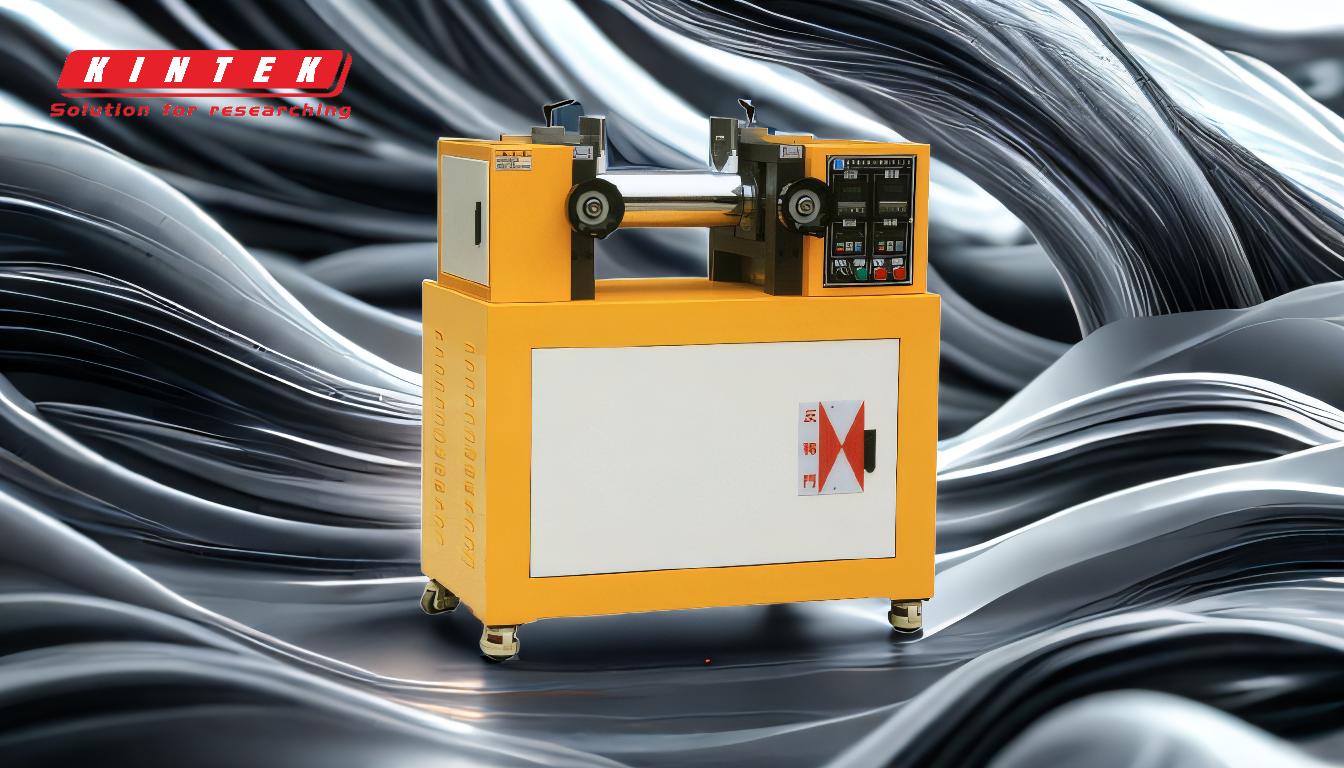
-
Structure of a Two-Roll Mill:
- The two-roll mill consists of two horizontally placed hollow metal rolls that rotate towards each other.
- The distance between the rolls, known as the nip, can be adjusted to control the thickness of the material being processed.
- The rolls rotate at different speeds, creating a friction ratio that facilitates the mixing process.
-
Material Feeding and Initial Processing:
- Rubber or plastic materials, along with additives like dying agents or fillers, are fed into the gap between the two rolls.
- The rotation of the rolls draws the materials into the nip, where they are subjected to intensive squeezing and shearing forces.
-
Heat Generation and Shearing Action:
- The friction between the rolls generates heat, which softens the materials and makes them more pliable.
- The speed difference between the rolls creates shearing forces that stretch and break the internal macromolecular chains of the materials.
- This shearing action increases the contact area between the different components, promoting uniform mixing.
-
Dispersion and Mixing:
- As the materials pass through the nip, they are repeatedly squeezed and sheared, which disperses the additives evenly throughout the compound.
- The process continues until the desired level of mastication or mixing is achieved, resulting in a homogeneous mixture.
-
Final Output:
- The mixed material is typically removed from the rolls in the form of a sheet-like compound.
- This sheet can then be further processed or used directly in manufacturing applications.
-
Importance of the Friction Ratio:
- The friction ratio, which is the speed difference between the two rolls, is crucial for effective mixing.
- A higher friction ratio increases the shearing forces, which enhances the mixing efficiency but may also generate more heat.
- The optimal friction ratio depends on the specific materials being processed and the desired properties of the final compound.
-
Applications of Two-Roll Mill Mixing:
- The two-roll mill is widely used in the rubber and plastic industries for compounding and mastication.
- It is particularly useful for preparing materials for further processing, such as extrusion, molding, or calendering.
- The process is also used in laboratory mills for small-scale mixing and testing of new formulations.
-
Advantages of Two-Roll Mill Mixing:
- The process allows for precise control over the mixing conditions, including temperature, nip gap, and friction ratio.
- It is effective for dispersing additives and achieving uniform mixing, even with difficult-to-mix materials.
- The sheet-like output is easy to handle and can be directly used in subsequent manufacturing processes.
-
Challenges and Considerations:
- The process can generate significant heat, which may require cooling mechanisms to prevent overheating of the materials.
- The shearing forces can cause wear and tear on the rolls, necessitating regular maintenance.
- The process may not be suitable for materials that are highly sensitive to heat or mechanical stress.
In summary, the two-roll mill mixing process is a critical step in the rubber and plastic industries, enabling the uniform dispersion of additives and the preparation of materials for further processing. The process relies on the mechanical action of two rotating rolls, which generate heat and shearing forces to achieve the desired mixing state. Understanding the key parameters, such as the friction ratio and nip gap, is essential for optimizing the process and achieving high-quality results.
Summary Table:
Key Aspect | Description |
---|---|
Structure | Two horizontally placed metal rolls rotating at different speeds. |
Material Feeding | Rubber/plastic and additives are fed into the nip for squeezing and shearing. |
Heat & Shearing | Friction generates heat, while speed differences create shearing forces. |
Dispersion & Mixing | Repeated squeezing and shearing ensure uniform mixing of additives. |
Final Output | Sheet-like compound ready for further processing or direct use. |
Friction Ratio | Speed difference between rolls is critical for effective mixing. |
Applications | Used in rubber/plastic industries for compounding and mastication. |
Advantages | Precise control, uniform mixing, and easy-to-handle output. |
Challenges | Heat generation, roll wear, and material sensitivity considerations. |
Optimize your rubber and plastic compounding process—contact our experts today for tailored solutions!