Plasma nitriding is a surface hardening process that enhances the wear resistance, fatigue strength, and corrosion resistance of ferrous alloys, including stainless steels. The process is performed in a vacuum environment where nitrogen ions are introduced into the surface of the material through a plasma discharge. The typical temperature range for plasma nitriding is between 350°C to 600°C (662°F to 1112°F), depending on the material and desired properties. This temperature range ensures effective diffusion of nitrogen into the material while avoiding excessive thermal stress or distortion. Plasma nitriding offers advantages such as no need for special surface preparation, precise control over the process, and the ability to mask specific areas. However, challenges include the risk of overheating, batch size limitations, and high initial costs.
Key Points Explained:
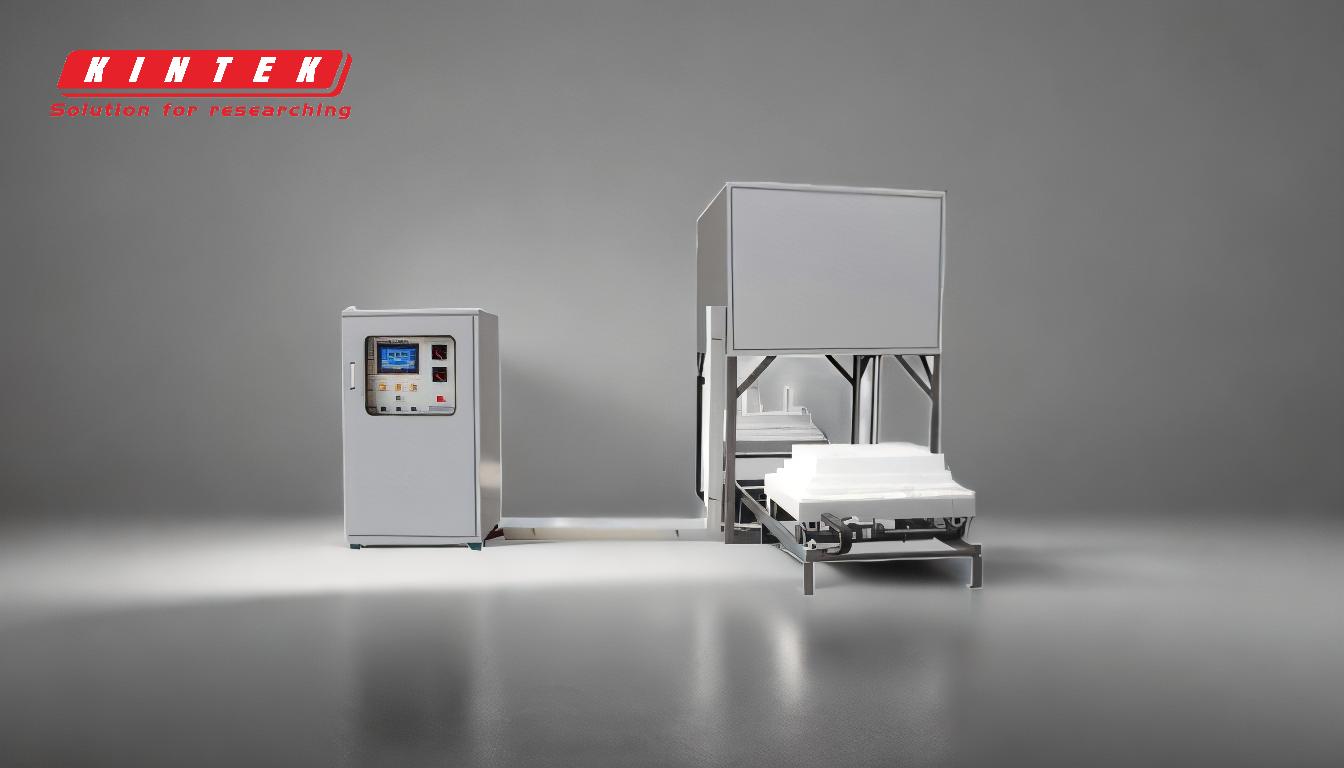
-
Typical Temperature Range for Plasma Nitriding:
- The process operates within a range of 350°C to 600°C (662°F to 1112°F). This range is chosen to balance effective nitrogen diffusion with minimal thermal distortion.
- Lower temperatures (350°C–450°C) are often used for materials like stainless steels to prevent chromium nitride formation, which can reduce corrosion resistance.
- Higher temperatures (500°C–600°C) are suitable for low-alloy steels and tool steels, where deeper case depths and higher hardness are required.
-
Advantages of Plasma Nitriding:
- No Special Preparation Required: Unlike gas nitriding, plasma nitriding does not require surface activation or special preparation, making it suitable for a wide range of ferrous alloys.
- Precise Control: The process allows for precise control over the nitriding layer, enabling customization of surface hardness and case depth.
- Masking Capability: Mechanical masking can be used to protect specific areas, such as threaded holes, from nitriding, ensuring they remain soft and functional.
-
Challenges of Plasma Nitriding:
- Overheating Risk: Parts must be carefully monitored to avoid overheating, which can lead to distortion or damage.
- Batch Size Limitations: Components of similar size cannot always be processed together due to the power/area relationship, which can limit throughput.
- High Initial Cost: The equipment and setup costs for plasma nitriding are higher compared to traditional nitriding methods, which may be a barrier for smaller operations.
-
Applications and Materials:
- Plasma nitriding is widely used for stainless steels, tool steels, and low-alloy steels to improve wear resistance, fatigue strength, and corrosion resistance.
- It is particularly beneficial for components in industries such as automotive, aerospace, and tooling, where surface hardening is critical.
-
Process Considerations:
- The treatment results are based on standard and long-term treatments, ensuring consistent and reliable outcomes.
- The process is performed in a vacuum environment, which minimizes contamination and ensures a clean, uniform surface.
By understanding the temperature range, advantages, and challenges of plasma nitriding, equipment and consumable purchasers can make informed decisions about its suitability for specific applications and materials.
Summary Table:
Aspect | Details |
---|---|
Temperature Range | 350°C to 600°C (662°F to 1112°F) |
Advantages | No special preparation, precise control, masking capability |
Challenges | Overheating risk, batch size limitations, high initial costs |
Applications | Stainless steels, tool steels, low-alloy steels |
Key Industries | Automotive, aerospace, tooling |
Learn how plasma nitriding can enhance your material's performance—contact our experts today!