The annealing process in the metal industry is a critical heat treatment technique used to modify the microstructure of metals, primarily to reduce hardness, increase ductility, and relieve internal stresses. By heating the metal to a specific temperature and then cooling it at a controlled rate, annealing helps in reducing crystal structure dislocations, making the material more workable and less prone to cracking under stress. This process is essential for improving the machinability and cold-working properties of metals, ensuring they can be shaped or processed further without failure.
Key Points Explained:
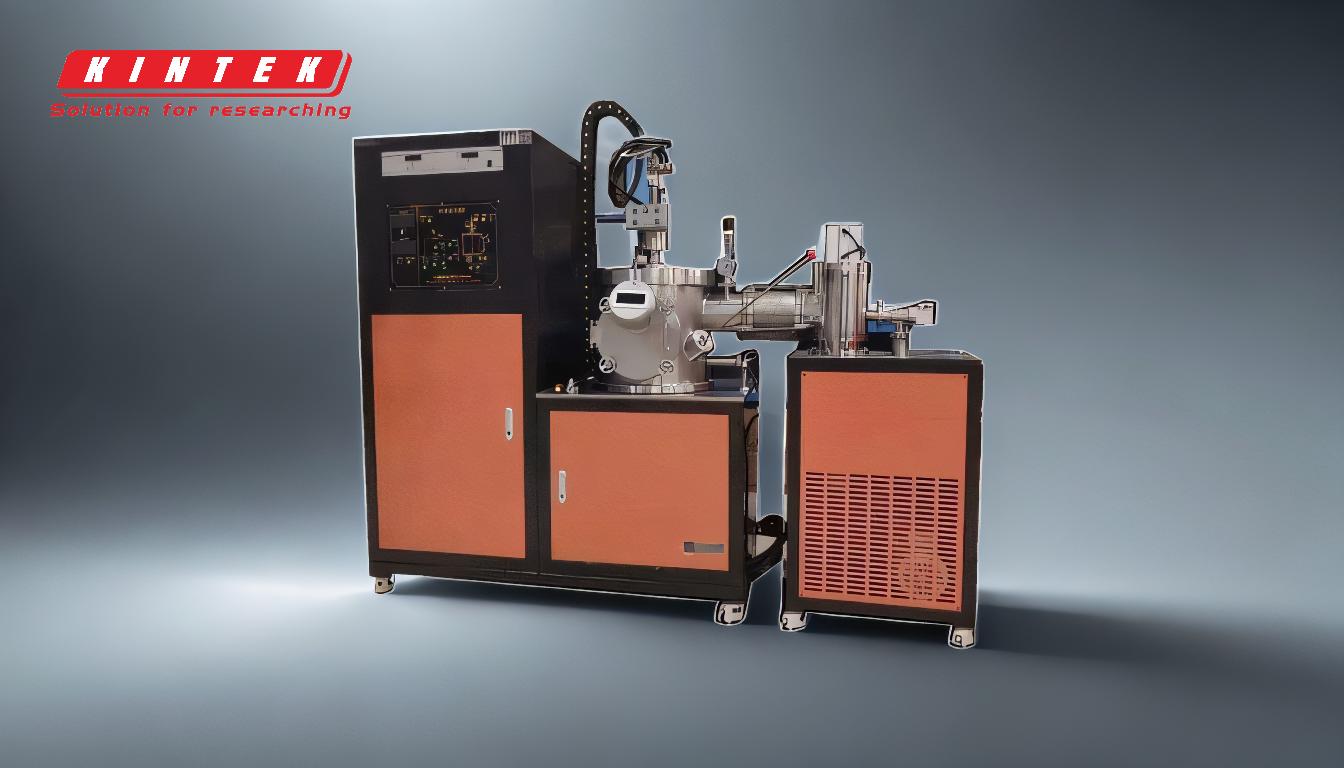
-
Reduction of Hardness:
- Annealing softens the metal by altering its internal structure. When metals are subjected to mechanical processes like rolling, forging, or extrusion, they often become harder and more brittle due to the introduction of internal stresses and dislocations in the crystal lattice.
- During annealing, the metal is heated to a temperature where these dislocations can rearrange, reducing internal stresses and restoring the metal to a softer state. This makes the material easier to machine or shape without cracking.
-
Increase in Ductility:
- Ductility refers to a material's ability to deform under tensile stress without breaking. Annealing enhances ductility by allowing the metal's crystal structure to reform into a more uniform and less stressed configuration.
- This is particularly important for metals that need to undergo further processing, such as cold working or drawing, where high ductility is required to prevent fractures.
-
Relief of Internal Stresses:
- Internal stresses in metals can arise from manufacturing processes, uneven cooling, or mechanical deformation. These stresses can lead to warping, cracking, or failure during service.
- Annealing relieves these stresses by heating the metal to a temperature where atoms can move more freely, allowing the material to "relax" and achieve a more stable, stress-free state.
-
Improved Machinability and Workability:
- Hard metals are difficult to machine or shape, as they require more force and are prone to tool wear. Annealing makes metals softer and more uniform, improving their machinability and reducing wear on tools.
- This is especially beneficial for metals that will undergo further processing, such as cutting, drilling, or bending.
-
Microstructural Homogenization:
- Annealing promotes a more uniform and homogeneous microstructure by allowing grain growth and recrystallization. This results in a more consistent material with predictable mechanical properties.
- A homogeneous structure is crucial for applications where uniform strength and performance are required, such as in structural components or electrical conductors.
-
Enhanced Electrical Conductivity:
- For certain metals, such as copper, annealing can improve electrical conductivity by reducing crystal defects and dislocations. This is particularly important in the production of electrical wires and components.
- A more uniform crystal structure allows electrons to flow more freely, enhancing the metal's ability to conduct electricity.
-
Preparation for Further Processing:
- Annealing is often used as an intermediate step in metalworking to prepare the material for additional heat treatments or mechanical processes. For example, it can restore a metal to its "soft" condition, making it suitable for further shaping or machining.
- This ensures that the material remains workable and less prone to failure during subsequent manufacturing steps.
-
Applications in Various Industries:
- Annealing is widely used in industries such as automotive, aerospace, construction, and electronics. For instance, in the automotive industry, annealed metals are used for components that require high ductility and strength, such as gears and shafts.
- In the electronics industry, annealing is critical for producing high-conductivity copper wires used in electrical circuits.
By understanding the role of annealing in the metal industry, manufacturers can optimize their processes to produce materials with the desired mechanical and physical properties, ensuring better performance and longevity in their applications.
Summary Table:
Key Benefits of Annealing | Description |
---|---|
Reduction of Hardness | Softens metal by rearranging dislocations, making it easier to machine or shape. |
Increase in Ductility | Enhances the metal's ability to deform without breaking, ideal for further processing. |
Relief of Internal Stresses | Reduces internal stresses to prevent warping, cracking, or failure. |
Improved Machinability | Makes metals softer and more uniform, reducing tool wear during machining. |
Microstructural Homogenization | Promotes uniform grain growth for consistent mechanical properties. |
Enhanced Electrical Conductivity | Improves conductivity in metals like copper by reducing crystal defects. |
Preparation for Further Processing | Restores metals to a soft state for additional shaping or machining. |
Wide Industry Applications | Used in automotive, aerospace, construction, and electronics industries. |
Optimize your metal processing with annealing—contact our experts today!