Hot isostatic pressing (HIP) is a versatile manufacturing process used across various industries to improve the properties of materials such as ceramics, metals, composites, plastics, and carbon. It involves applying high temperature and pressure simultaneously using inert gases like argon to consolidate powders, heal defects in castings, or bond materials. This process is particularly useful for creating high-performance components in industries like aerospace, automotive, oil and gas, medical devices, and energy storage. HIP is divided into three main applications: densification, diffusion bonding, and powder metallurgy, each tailored to specific product requirements. Additionally, the warm isostatic press is a related technology that uses heated liquid media for precise temperature control during pressing.
Key Points Explained:
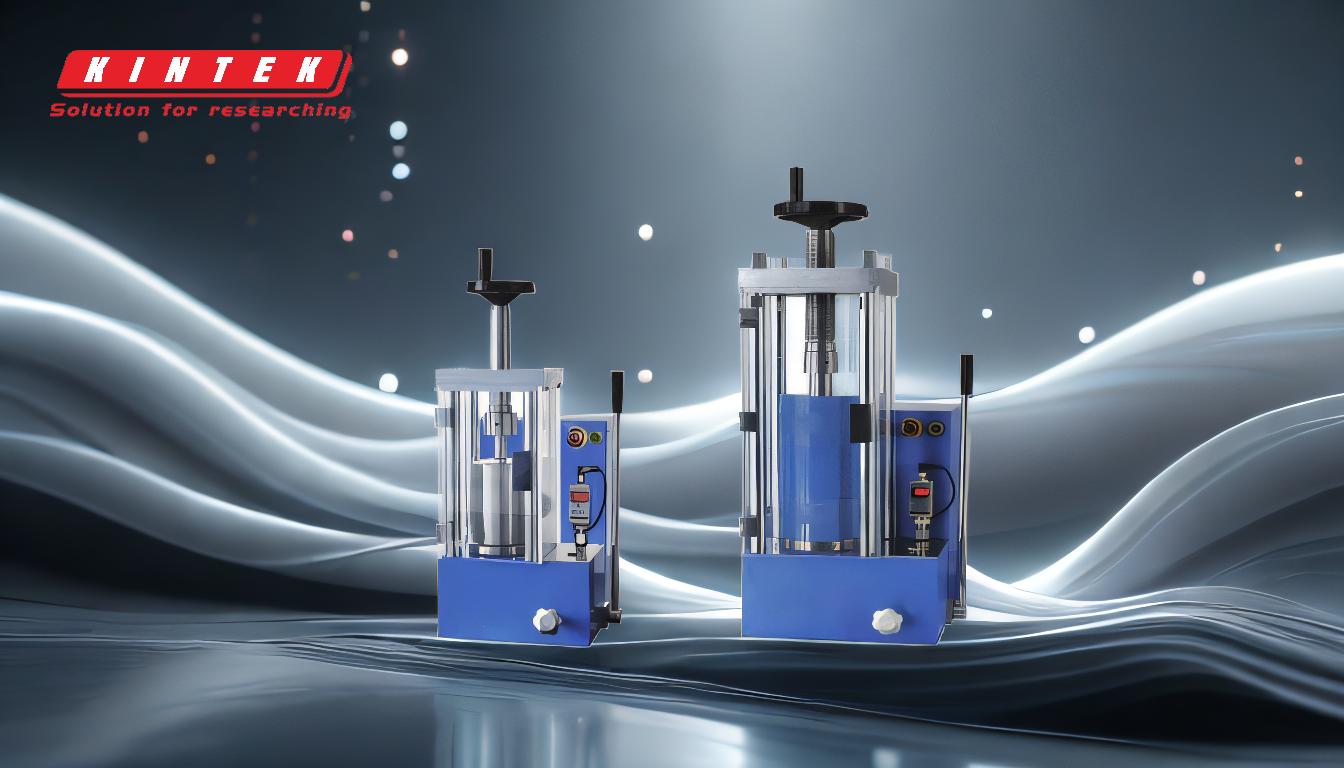
-
Process Overview:
- Hot isostatic pressing involves loading parts into a heating chamber where inert argon gas is applied under high pressure and temperature.
- The process includes heating, pressurization, controlled cooling, and depressurization to ensure the parts are safe to handle.
-
Applications:
- Densification: Used to consolidate powders, creating dense, high-strength materials.
- Defect Healing: Repairs internal defects in castings, improving their structural integrity.
- Diffusion Bonding: Joins materials without melting, ensuring strong, seamless bonds.
- Powder Metallurgy: Produces complex shapes and alloys that are difficult to achieve through traditional casting methods.
-
Industries and Materials:
- Aerospace and Automotive: Used to manufacture advanced ceramics and high-performance components.
- Oil and Gas: Produces durable parts for harsh environments.
- Medical Devices: Creates biocompatible and high-strength implants.
- Energy Storage: Enhances the performance of lithium-ion batteries and fuel cells.
-
Material Types:
- Suitable for ceramics (e.g., zirconia, alumina), metals, composites, plastics, and carbon-based materials.
-
Advantages:
- Improves material properties such as density, strength, and fatigue resistance.
- Enables the production of complex geometries and alloys.
- Reduces defects and enhances the reliability of critical components.
-
Warm Isostatic Press:
- A variation of HIP, the warm isostatic press uses heated liquid media for precise temperature control, making it ideal for specific applications requiring lower temperatures than traditional HIP.
-
Future Trends:
- Increasing adoption in energy storage technologies and additive manufacturing.
- Development of new alloys and materials with enhanced properties.
By understanding these key points, equipment and consumable purchasers can make informed decisions about integrating hot isostatic pressing into their manufacturing processes to achieve superior product performance and reliability.
Summary Table:
Key Aspect | Details |
---|---|
Process Overview | High temperature and pressure using inert gases like argon. |
Applications | Densification, defect healing, diffusion bonding, powder metallurgy. |
Industries | Aerospace, automotive, oil & gas, medical devices, energy storage. |
Material Types | Ceramics, metals, composites, plastics, carbon. |
Advantages | Improves density, strength, fatigue resistance, and reduces defects. |
Related Technology | Warm isostatic press for precise temperature control. |
Future Trends | Growing use in energy storage and additive manufacturing. |
Ready to enhance your manufacturing process? Contact us today to learn more about hot isostatic pressing!