Resistance furnaces are versatile heating devices used across various industries for processes such as hardening, annealing, sintering, and material treatment. They operate by generating heat through electrical resistance, offering precise temperature control and high thermal efficiency. These furnaces are well-suited for applications requiring high temperatures, often exceeding 1500°C, and are designed to maintain a sealed environment to prevent heat loss and oxidation. Their ability to handle demanding workpieces and provide consistent, controlled heating makes them indispensable in fields like metallurgy, ceramics, electronics, and scientific research.
Key Points Explained:
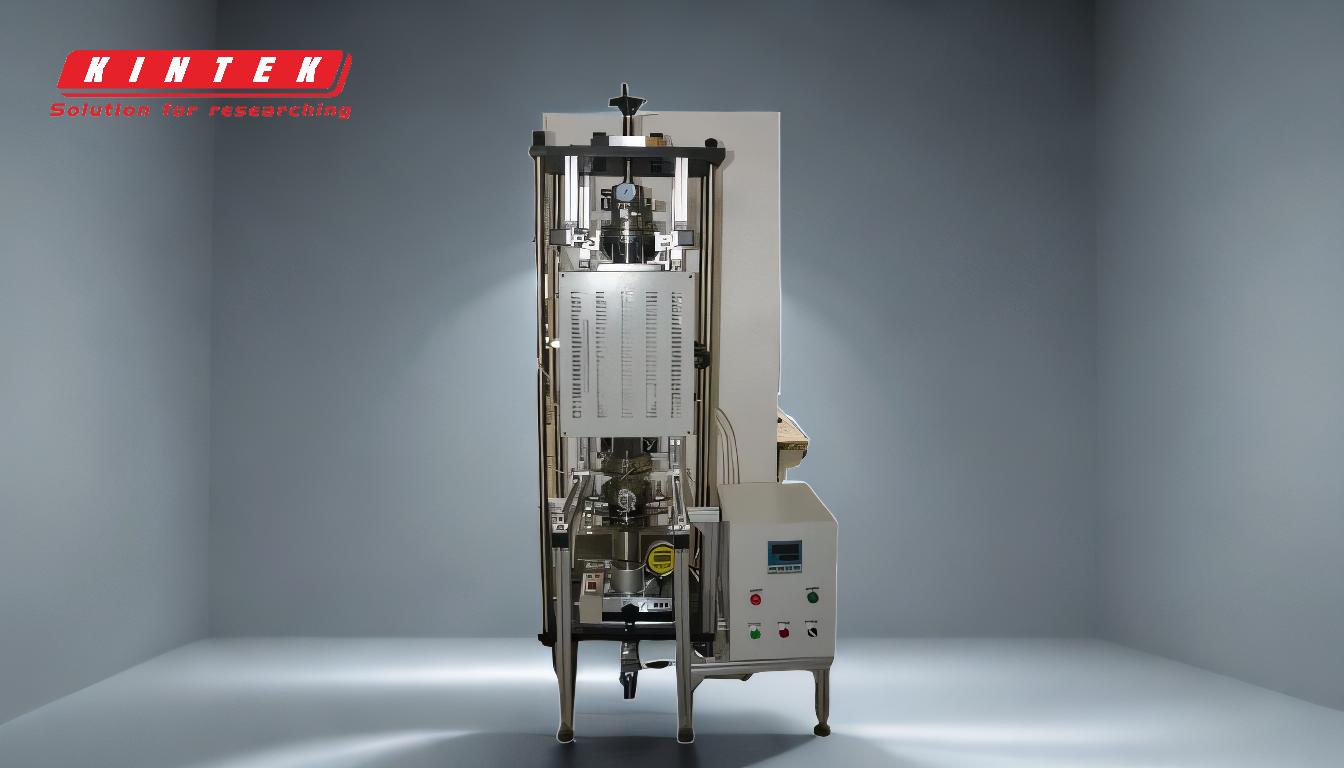
-
Operating Principle of Resistance Furnaces:
- Resistance furnaces generate heat through electrical resistance, where the furnace charge (material to be heated) acts as the resistance element.
- Heat is produced either by electrodes embedded in the material or by resistance elements lining the furnace interior.
- This method ensures uniform heating and precise temperature control, making it ideal for high-temperature applications.
-
Temperature Range and Applications:
- Resistance furnaces can operate at temperatures exceeding 1500°C, making them suitable for high-temperature processes.
- High-Temperature Applications (1,050°C to 1,350°C): Used for hardening metals and other materials.
- Medium-Temperature Applications (300°C to 1,050°C): Employed for annealing, normalizing steel and non-ferrous metals, melting non-ferrous metals, and stove enamelling.
- These furnaces are also used for powder roasting, ceramic sintering, high-temperature experiments, and material treatment.
-
Industries and Use Cases:
- Resistance furnaces are widely used in industries such as ceramics, metallurgy, electronics, glass, chemicals, machinery, refractories, and special materials.
- They are also utilized in universities, scientific research institutes, and industrial enterprises for processes like annealing, sintering, and flue gas treatment.
- Their versatility makes them essential for both manufacturing and research purposes.
-
Advantages of Resistance Furnaces:
- High Thermal Efficiency (50-80%): Ensures effective heat utilization and energy savings.
- Precise Temperature Control: Automated control units maintain consistent temperatures, crucial for sensitive processes.
- Sealed Environment: Prevents heat loss and oxidation, enhancing the quality of treated materials.
- Durability: Long furnace life and suitability for demanding workpieces make them a cost-effective choice.
-
Limitations:
- High Power Consumption: Resistance furnaces require significant electrical energy, which can increase operational costs.
- Despite this drawback, their efficiency and precision often outweigh the energy expenses, especially in specialized applications.
-
Special Features:
- Vacuum Sealing: Creates an airtight environment to prevent oxidation and hardening, particularly beneficial for mining and metallurgical applications.
- Gaseous Medium: Some furnaces use a controlled atmosphere to further eliminate oxidation risks and enhance material properties.
In summary, resistance furnaces are indispensable tools in industries requiring precise and high-temperature heating. Their ability to maintain controlled environments, coupled with high thermal efficiency and durability, makes them ideal for a wide range of applications, from material hardening to scientific research. While they consume significant power, their benefits in terms of quality and consistency often justify their use.
Summary Table:
Feature | Details |
---|---|
Operating Principle | Heat generated through electrical resistance; ensures uniform heating. |
Temperature Range | Up to 1500°C; suitable for hardening, annealing, sintering, and more. |
Industries | Metallurgy, ceramics, electronics, glass, chemicals, and scientific research. |
Advantages | High thermal efficiency (50-80%), precise temperature control, durability. |
Limitations | High power consumption, but benefits often outweigh costs. |
Special Features | Vacuum sealing, gaseous medium for oxidation prevention. |
Ready to enhance your processes with a resistance furnace? Contact our experts today to find the perfect solution for your needs!