Vacuum deposition is a sophisticated technique used to create thin films or coatings on solid surfaces by depositing material atom-by-atom or molecule-by-molecule in a high-vacuum environment. This process is essential for applications requiring precise control over film thickness, ranging from nanometers to millimeters, and is widely used in industries such as electronics, optics, and manufacturing. Techniques like physical vapor deposition (PVD), chemical vapor deposition (CVD), thermal evaporation, and sputtering are commonly employed in vacuum deposition. The method ensures a clean, controlled environment, minimizing contamination and enabling the production of high-quality coatings with enhanced properties like conductivity, corrosion resistance, and optical performance.
Key Points Explained:
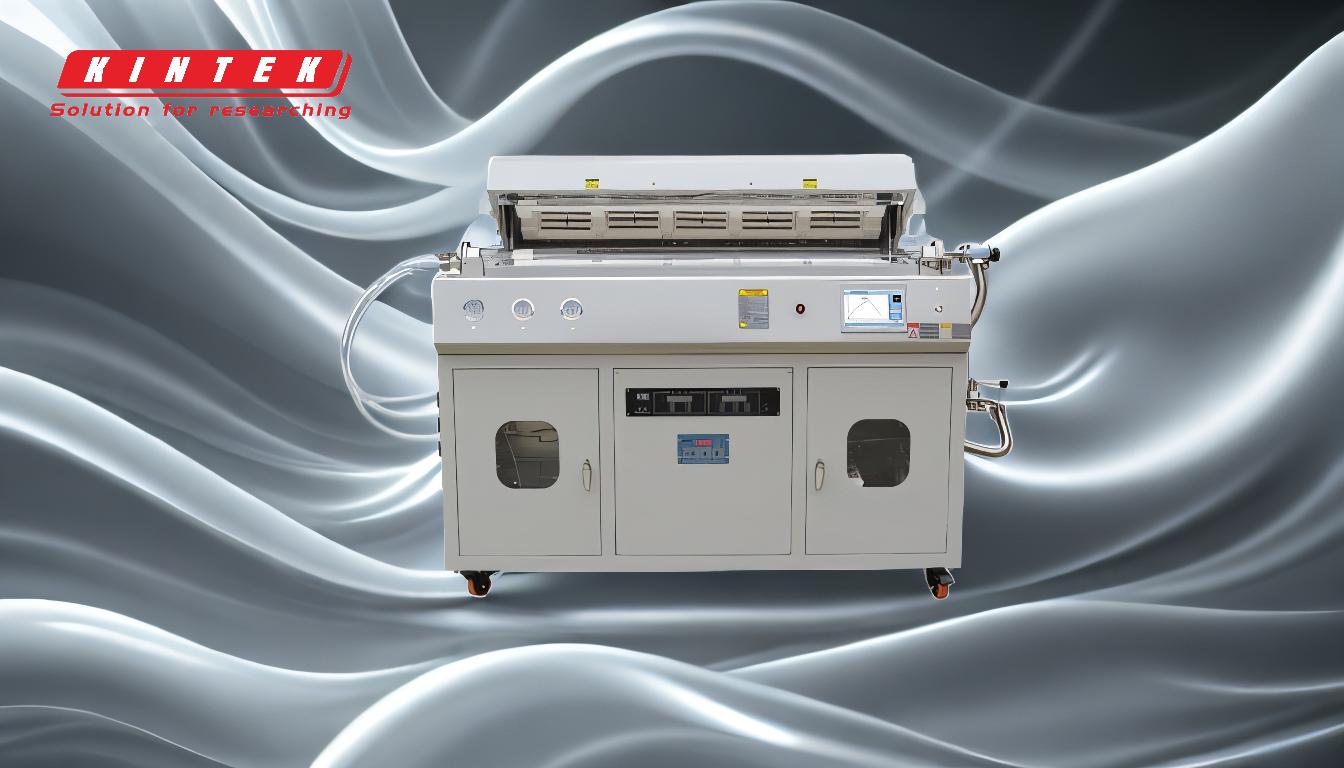
-
Definition and Purpose of Vacuum Deposition:
- Vacuum deposition is a family of processes that deposit thin layers of material onto a substrate in a high-vacuum environment.
- The primary purpose is to create coatings or films with precise thickness and enhanced properties, such as improved conductivity, optical performance, or corrosion resistance.
-
How Vacuum Deposition Works:
- The process occurs in a vacuum chamber where the pressure is significantly reduced, minimizing the presence of gas molecules.
- Material is deposited atom-by-atom or molecule-by-molecule onto the substrate surface, ensuring uniformity and precision.
- Techniques like thermal evaporation, sputtering, ion beam deposition, and chemical vapor deposition (CVD) are commonly used.
-
Key Techniques in Vacuum Deposition:
- Physical Vapor Deposition (PVD): Involves the physical transfer of material from a source to the substrate, often using methods like sputtering or thermal evaporation.
- Chemical Vapor Deposition (CVD): Uses chemical reactions to deposit material onto the substrate, often at elevated temperatures.
- Thermal Evaporation: Material is heated until it vaporizes and then condenses onto the substrate.
- Sputtering: Atoms are ejected from a target material and deposited onto the substrate using a plasma or ion beam.
-
Advantages of Vacuum Deposition:
- Precision: Allows for the deposition of extremely thin films, even at the nanometer scale.
- Clean Environment: The vacuum minimizes contamination, ensuring high-quality coatings.
- Versatility: Can be used with a wide range of materials, including metals, ceramics, and polymers.
- Enhanced Properties: Improves properties like conductivity, optical performance, and corrosion resistance.
-
Applications of Vacuum Deposition:
- Electronics: Used in the production of semiconductors, thin-film transistors, and solar cells.
- Optics: Creates anti-reflective coatings, mirrors, and lenses.
- Manufacturing: Enhances the durability and performance of tools and components through protective coatings.
- Medical Devices: Provides biocompatible coatings for implants and surgical tools.
-
Challenges and Considerations:
- Cost: Vacuum deposition equipment and processes can be expensive.
- Complexity: Requires specialized knowledge and precise control of process parameters.
- Scalability: While effective for small-scale applications, scaling up for mass production can be challenging.
-
Future Trends in Vacuum Deposition:
- Nanotechnology: Increasing use of vacuum deposition in nanotechnology for creating nanoscale devices and materials.
- Sustainability: Development of more energy-efficient and environmentally friendly deposition techniques.
- Advanced Materials: Exploration of new materials, such as 2D materials (e.g., graphene) and hybrid organic-inorganic compounds, for innovative applications.
In summary, vacuum deposition is a critical technology for creating high-quality thin films and coatings with precise control over thickness and properties. Its applications span across various industries, and ongoing advancements continue to expand its capabilities and potential uses.
Summary Table:
Aspect | Details |
---|---|
Definition | Depositing material atom-by-atom in a vacuum to create thin films. |
Key Techniques | PVD, CVD, thermal evaporation, sputtering. |
Advantages | Precision, clean environment, versatility, enhanced material properties. |
Applications | Electronics, optics, manufacturing, medical devices. |
Challenges | High cost, complexity, scalability issues. |
Future Trends | Nanotechnology, sustainability, advanced materials. |
Discover how vacuum deposition can elevate your projects—contact our experts today!