The vacuum induction method is a specialized process used primarily in metallurgy and materials science for melting and refining metals under vacuum conditions. This method employs a vacuum induction furnace, which combines the principles of induction heating with a vacuum environment to achieve precise control over the melting process. The vacuum environment prevents oxidation and contamination, making it ideal for producing high-purity metals and alloys. The furnace's key components include an airtight, water-cooled steel jacket, a crucible within an induction coil, and a vacuum system. This setup allows for uniform heating, precise temperature control, and the removal of impurities, ensuring high-quality end products.
Key Points Explained:
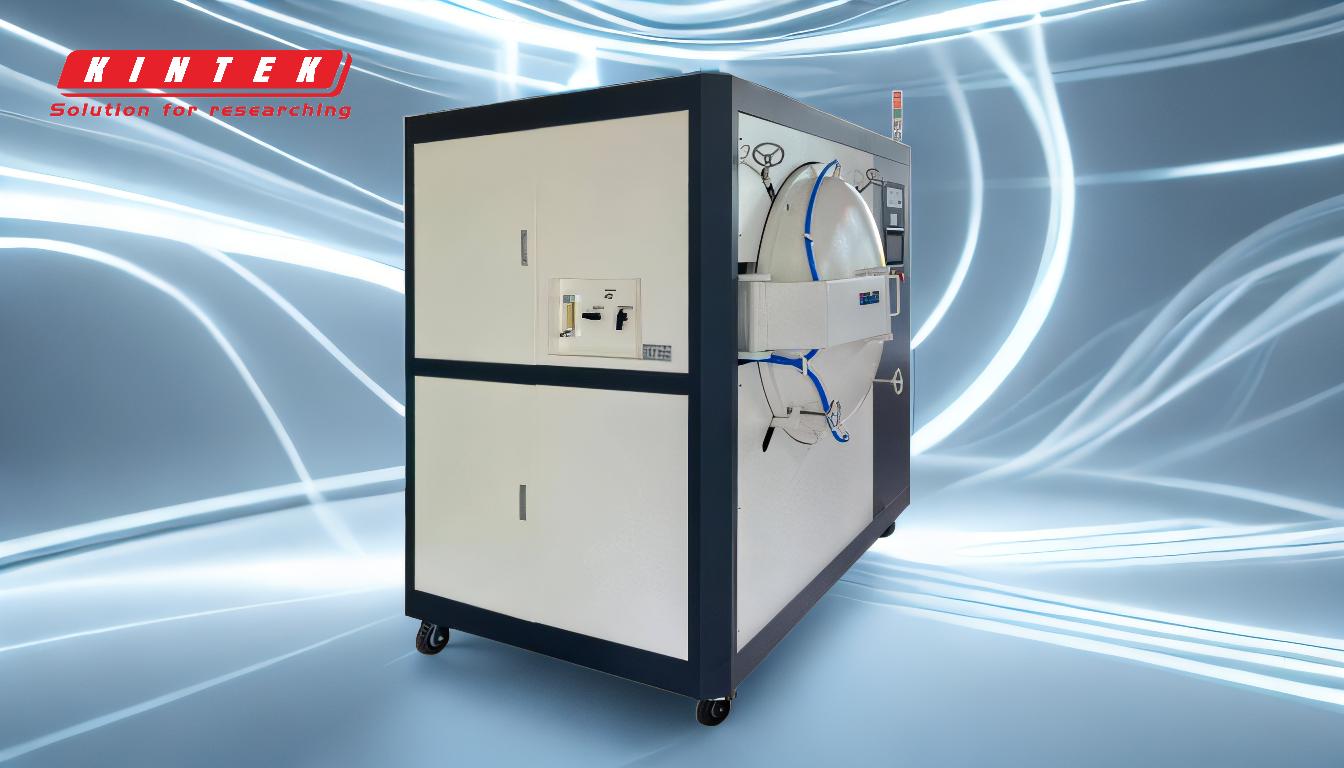
-
Definition and Purpose of the Vacuum Induction Method:
- The vacuum induction method is a process used to melt and refine metals in a vacuum environment. It is particularly useful for producing high-purity metals and alloys, as the vacuum prevents oxidation and contamination.
- This method is widely used in industries such as aerospace, automotive, and electronics, where material purity and performance are critical.
-
Components of a Vacuum Induction Furnace:
- Airtight, Water-Cooled Steel Jacket: This component ensures the furnace can maintain a vacuum and withstand the high temperatures involved in the melting process.
- Crucible and Induction Coil: The crucible, housed within a water-cooled induction coil, is where the metal is melted. The induction coil generates an electromagnetic field that induces eddy currents in the metal, heating it uniformly.
- Vacuum System: This system creates and maintains the vacuum environment, which is essential for preventing oxidation and contamination during the melting process.
-
How the Vacuum Induction Method Works:
- Induction Heating: The induction coil generates an alternating magnetic field, which induces eddy currents in the metal. These currents generate heat due to resistance, melting the metal.
- Vacuum Environment: The vacuum system removes air and other gases from the furnace, creating a low-pressure environment. This prevents oxidation and allows for the removal of volatile impurities.
- Temperature Control: Advanced control systems allow for precise regulation of the heating process, ensuring uniform melting and refining of the metal.
-
Advantages of the Vacuum Induction Method:
- High Purity: The vacuum environment prevents oxidation and contamination, resulting in high-purity metals and alloys.
- Uniform Heating: Induction heating ensures that the metal is heated uniformly, reducing the risk of hot spots and ensuring consistent quality.
- Precise Control: Advanced control systems allow for precise regulation of the melting process, enabling the production of materials with specific properties.
-
Applications of the Vacuum Induction Method:
- Aerospace: Used to produce high-performance alloys for aircraft engines and other critical components.
- Automotive: Employed in the production of high-strength, lightweight materials for vehicle components.
- Electronics: Utilized to create high-purity metals for semiconductors and other electronic components.
-
Maintenance and Operation:
- Regular Maintenance: Components such as the vacuum system, induction coil, and crucible require regular maintenance to ensure optimal performance.
- Safety Interlocks: Modern vacuum induction furnaces are equipped with safety interlocks to prevent accidents and ensure safe operation.
By understanding these key points, one can appreciate the complexity and precision involved in the vacuum induction method, making it a valuable tool in the production of high-quality metals and alloys.
Summary Table:
Aspect | Details |
---|---|
Purpose | Melting and refining metals in a vacuum to prevent oxidation and contamination. |
Key Components | Airtight steel jacket, crucible, induction coil, and vacuum system. |
How It Works | Induction heating in a vacuum environment for uniform melting and impurity removal. |
Advantages | High purity, uniform heating, and precise temperature control. |
Applications | Aerospace, automotive, and electronics industries. |
Maintenance | Regular upkeep of vacuum system, induction coil, and crucible is essential. |
Interested in learning more about vacuum induction furnaces? Contact our experts today to discuss your needs!