The vacuum level of a vacuum furnace is a critical parameter that determines its performance in various industrial applications. Typically, a vacuum furnace can achieve a vacuum level as low as 7×10⁻³ Pa, depending on the configuration of its vacuum system, which may include components like mechanical pumps, diffusion pumps, and Roots pumps. Before heating, the furnace is often pre-pumped to around 6.67 Pa to ensure optimal conditions. However, achieving and maintaining this vacuum level can be challenging due to factors like damaged door seals, furnace leaks, or contamination in the high-temperature zone, which are common causes of poor evacuation.
Key Points Explained:
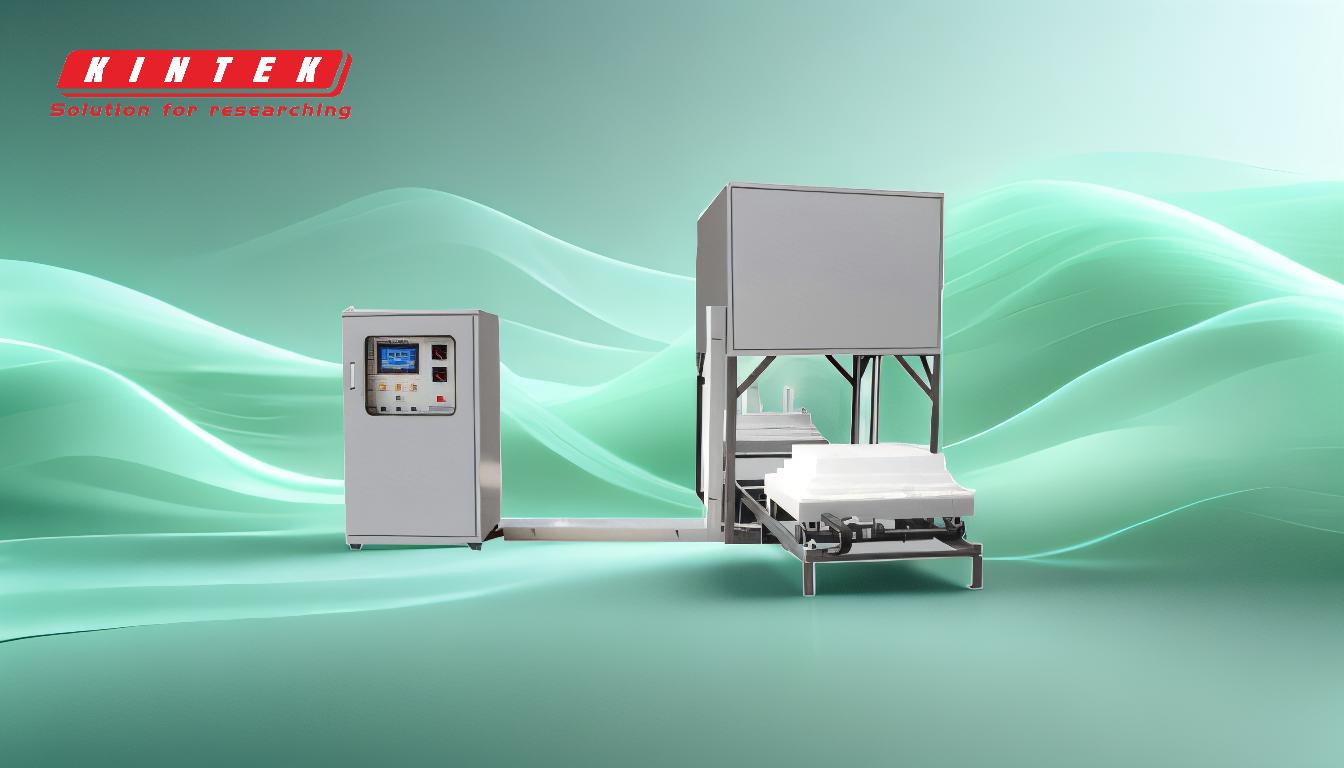
-
Typical Vacuum Levels in a Vacuum Furnace:
- A vacuum furnace can achieve a maximum vacuum level of 7×10⁻³ Pa, which is considered high vacuum and suitable for processes requiring minimal contamination and oxidation.
- Before heating, the furnace is often pre-pumped to 6.67 Pa to remove air and moisture, ensuring a stable environment for the workpiece.
-
Components of the Vacuum System:
- The vacuum system in a vacuum furnace includes:
- Mechanical pumps: Used for initial rough pumping to achieve low vacuum levels.
- Diffusion pumps: Employed to achieve higher vacuum levels by removing residual gases.
- Roots pumps: Often used in combination with other pumps to enhance pumping speed and efficiency.
- Vacuum valves: Control the flow of gases and maintain the vacuum level.
- The vacuum system in a vacuum furnace includes:
-
Factors Affecting Vacuum Level:
- Damaged door seals: The door seal is one of the most critical components, accounting for about 80% of evacuation problems. Wear and tear over time can lead to leaks.
- Furnace leaks: Small cracks or gaps in the furnace structure can compromise the vacuum level.
- Contamination in the high-temperature zone: Residues or debris can outgas during heating, reducing the vacuum level.
-
Importance of Maintaining Vacuum Levels:
- A stable and high vacuum level is essential for processes like brazing, sintering, and heat treatment, where oxidation and contamination must be minimized.
- Regular maintenance of the vacuum system, including checking seals and cleaning the furnace, is crucial to ensure consistent performance.
-
Troubleshooting Poor Evacuation:
- If the vacuum level is not achieved, common troubleshooting steps include:
- Inspecting and replacing damaged door seals.
- Checking for leaks in the furnace structure.
- Cleaning the high-temperature zone to remove contaminants.
- If the vacuum level is not achieved, common troubleshooting steps include:
By understanding the factors that influence vacuum levels and maintaining the vacuum system properly, operators can ensure the efficient and reliable operation of a vacuum furnace.
Summary Table:
Aspect | Details |
---|---|
Typical Vacuum Levels | - Maximum: 7×10⁻³ Pa (high vacuum) - Pre-pump: 6.67 Pa |
Vacuum System Components | - Mechanical pumps - Diffusion pumps - Roots pumps - Valves |
Factors Affecting Vacuum | - Damaged door seals (80% of issues) - Furnace leaks - Contamination |
Maintenance Tips | - Inspect/replace seals - Check for leaks - Clean high-temp zone |
Ensure your vacuum furnace operates at peak efficiency—contact our experts today for tailored solutions!