The vapor transport deposition (VTD) process is a specialized method used to deposit thin films or coatings onto substrates, typically in a vacuum environment. It involves the transport of vaporized materials (either through physical or chemical means) to a substrate, where they condense and form a thin, uniform layer. This process is widely used in industries such as semiconductors, optics, and energy storage due to its precision and ability to produce high-quality coatings. VTD can be categorized into physical vapor deposition (PVD) and chemical vapor deposition (CVD), each with distinct mechanisms and applications. PVD relies on physical processes like evaporation or sputtering, while CVD involves chemical reactions to form the desired film. Both methods require controlled environments, precise temperature and pressure conditions, and specialized equipment to achieve optimal results.
Key Points Explained:
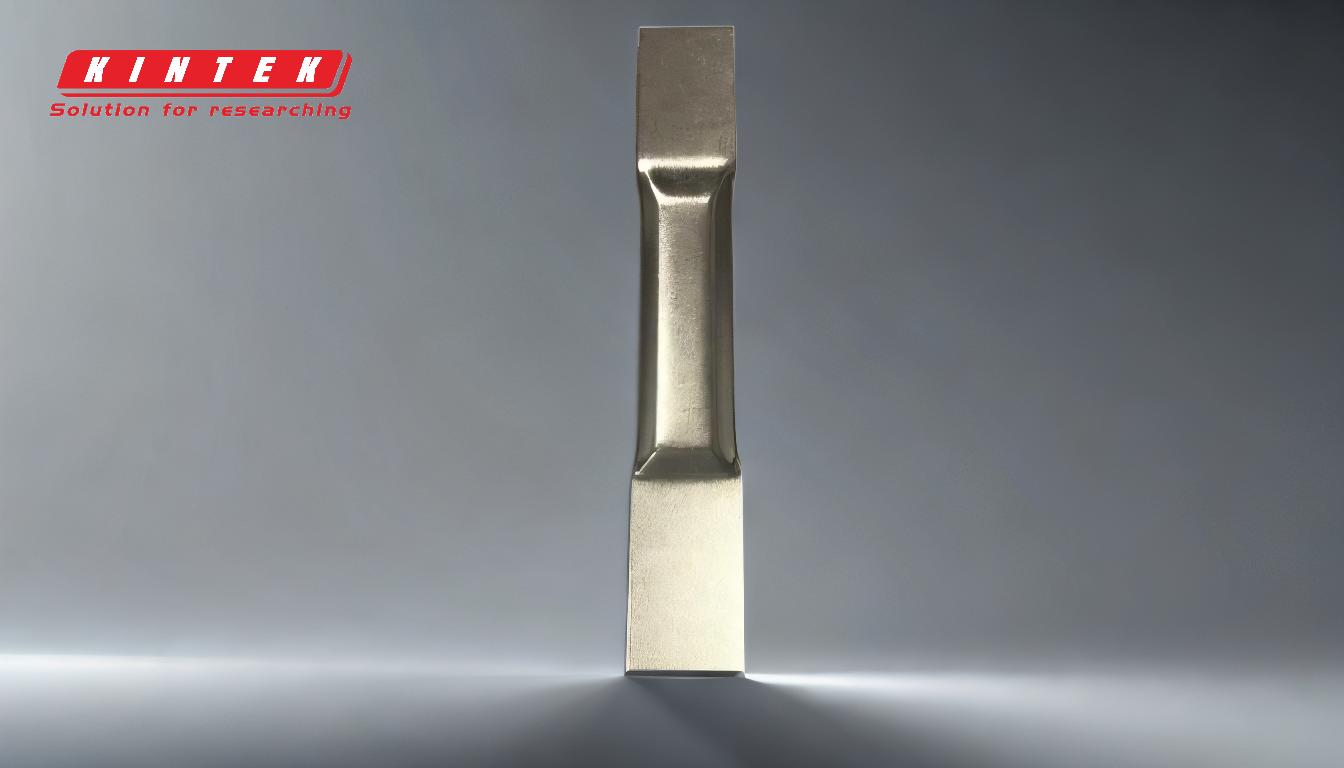
-
Definition and Purpose of Vapor Transport Deposition (VTD):
- VTD is a process used to deposit thin films or coatings onto substrates in a controlled environment.
- It is widely used in industries such as semiconductors, optics, and energy storage to create precise, high-quality coatings.
-
Types of Vapor Transport Deposition:
- Physical Vapor Deposition (PVD): Involves physical processes like evaporation or sputtering to transport vaporized material to the substrate. Examples include thermal evaporation and magnetron sputtering.
- Chemical Vapor Deposition (CVD): Relies on chemical reactions between gaseous precursors to form a thin film on the substrate. Examples include low-pressure CVD (LPCVD) and plasma-enhanced CVD (PECVD).
-
Key Steps in the VTD Process:
- Creating a Vacuum Environment: A vacuum chamber is used to eliminate air and gases that could interfere with the deposition process.
- Preparation of the Substrate: The substrate is cleaned or treated to ensure proper adhesion of the deposited material.
- Vaporization of the Material: In PVD, the material is vaporized through heating or sputtering. In CVD, gaseous precursors are introduced into the chamber.
- Transport and Deposition: The vaporized material or reactive gases are transported to the substrate, where they condense or react to form a thin film.
- Cooling and Venting: After deposition, the chamber is cooled and vented to allow removal of the coated substrate.
-
Mechanisms of VTD:
- Physical Processes (PVD): Involve the use of high-energy ions or plasma to vaporize the target material, which then condenses on the substrate.
- Chemical Processes (CVD): Involve chemical reactions between precursors, often activated by heat or plasma, to form the desired film on the substrate.
-
Applications of VTD:
- Semiconductors: Used to deposit thin films for integrated circuits and electronic devices.
- Optics: Applied in the production of anti-reflective coatings and optical filters.
- Energy Storage: Used to create coatings for battery materials, such as the carbon coating on LiFePO4 to enhance performance.
-
Advantages of VTD:
- Produces high-quality, uniform thin films with precise control over thickness and composition.
- Suitable for a wide range of materials, including metals, ceramics, and polymers.
- Environmentally friendly in some cases, such as CVD using solid precursors like glucose.
-
Challenges and Limitations:
- Requires sophisticated equipment and controlled environments, leading to higher costs.
- Longer production times, especially for CVD, due to lower decomposition rates of precursors.
- Limited scalability for large-scale production compared to other coating methods.
-
Key Factors Influencing VTD:
- Chamber Pressure: Low pressure is often required to ensure proper transport and deposition of materials.
- Substrate Temperature: Critical for controlling the rate of deposition and the quality of the film.
- Precursor Materials: The choice of precursors in CVD affects the chemical reactions and properties of the final film.
By understanding these key points, a purchaser of equipment or consumables can make informed decisions about the suitability of VTD for their specific applications, considering factors such as material requirements, desired film properties, and production scale.
Summary Table:
Aspect | Details |
---|---|
Types of VTD | Physical Vapor Deposition (PVD), Chemical Vapor Deposition (CVD) |
Key Steps | Vacuum creation, substrate preparation, vaporization, transport, deposition |
Applications | Semiconductors, optics, energy storage |
Advantages | High-quality films, precise control, material versatility |
Challenges | High costs, longer production times, limited scalability |
Key Factors | Chamber pressure, substrate temperature, precursor materials |
Discover how VTD can enhance your production process—contact our experts today!