The VAR (Vacuum Arc Remelting) process is a specialized metallurgical technique used to produce high-quality metal ingots, particularly for applications requiring exceptional purity and homogeneity. It involves the continuous remelting of a consumable electrode using an electric arc under vacuum conditions. The heat generated by the arc melts the electrode tip, which then solidifies in a water-cooled copper mold to form a new ingot. This process is conducted in a high vacuum to minimize contamination and ensure the removal of impurities. The VAR process is widely used in industries such as aerospace, medical, and energy, where material performance is critical.
Key Points Explained:
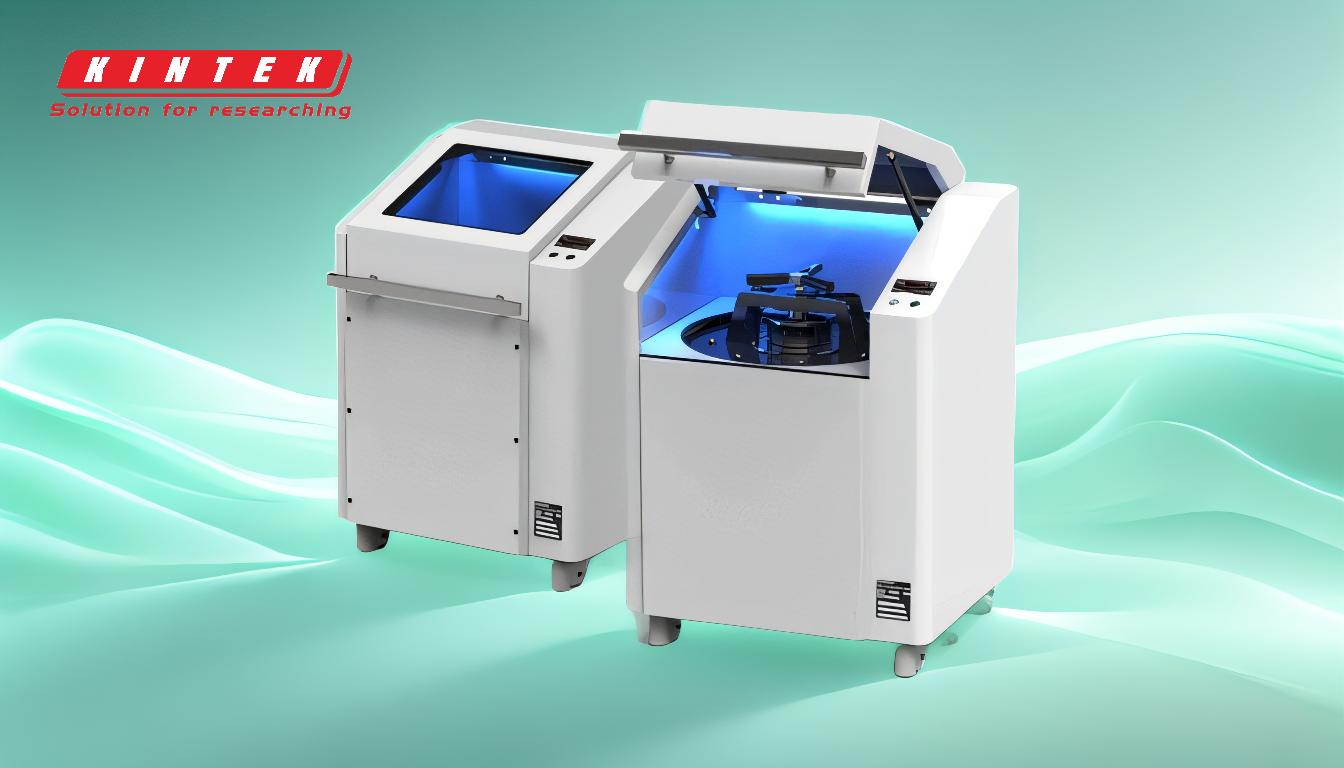
-
Core Principle of VAR Melting:
- The VAR process relies on the use of a direct current (DC) electric arc to melt a consumable electrode. The arc is struck between the electrode and a water-cooled copper mold, which serves as the crucible for the new ingot.
- The vacuum environment is essential to prevent oxidation and contamination, ensuring the production of high-purity metals and alloys.
-
Equipment and Setup:
- The primary components of a VAR furnace include the consumable electrode, the water-cooled copper mold, and the vacuum chamber.
- The consumable electrode is typically made from the same material as the desired ingot, ensuring consistency in composition.
- The water-cooled copper mold is designed to rapidly solidify the molten metal, forming a dense and homogeneous ingot.
-
Process Steps:
- Electrode Preparation: The consumable electrode is prepared from the raw material, often through processes like vacuum induction melting (VIM) or other primary melting techniques.
- Vacuum Creation: The chamber is evacuated to create a high vacuum, typically in the range of 10^-4 to 10^-5 torr.
- Arc Initiation: A DC power supply is used to strike an arc between the electrode and the copper mold. The heat generated by the arc melts the electrode tip.
- Ingot Formation: The molten metal drips into the mold, where it solidifies under controlled cooling conditions. The process continues until the entire electrode is consumed, forming a new ingot.
-
Advantages of VAR Melting:
- High Purity: The vacuum environment removes gases and volatile impurities, resulting in a cleaner and more homogeneous material.
- Improved Mechanical Properties: The controlled solidification process minimizes defects such as porosity and segregation, enhancing the mechanical properties of the ingot.
- Versatility: VAR can be used for a wide range of metals and alloys, including titanium, nickel-based superalloys, and specialty steels.
-
Applications:
- Aerospace: VAR is used to produce critical components such as turbine blades and engine parts, where material performance is paramount.
- Medical: The process is employed to manufacture biocompatible implants and surgical instruments from materials like titanium and cobalt-chromium alloys.
- Energy: VAR-produced materials are used in nuclear reactors and other high-stress environments.
-
Comparison with Vacuum Induction Melting (VIM):
- While both VAR and VIM are conducted under vacuum, they differ in their energy sources and applications.
- VIM uses electromagnetic induction to melt metal, making it suitable for initial melting and refining. In contrast, VAR is primarily used for remelting and refining already melted materials to achieve superior quality.
- VIM is often used as a precursor to VAR, where the initial melt is cast into electrodes for further processing.
-
Challenges and Considerations:
- Cost: The VAR process is capital-intensive due to the need for specialized equipment and high vacuum conditions.
- Process Control: Maintaining consistent arc stability and ingot quality requires precise control of parameters such as current, voltage, and cooling rates.
- Material Limitations: While VAR is versatile, it is most effective for materials that benefit from vacuum refining, such as reactive metals and high-performance alloys.
By understanding the VAR melting process, equipment purchasers can make informed decisions about its suitability for their specific applications, ensuring the production of high-quality materials tailored to their needs.
Summary Table:
Aspect | Details |
---|---|
Core Principle | Uses a DC electric arc to melt a consumable electrode under vacuum. |
Key Components | Consumable electrode, water-cooled copper mold, and vacuum chamber. |
Process Steps | Electrode preparation, vacuum creation, arc initiation, and ingot formation. |
Advantages | High purity, improved mechanical properties, and material versatility. |
Applications | Aerospace, medical implants, and energy sectors. |
Comparison with VIM | VAR refines already melted materials, while VIM is for initial melting. |
Challenges | High cost, precise process control, and material-specific limitations. |
Ready to enhance your material quality with the VAR melting process? Contact our experts today for tailored solutions!