The water quality for an IGBT induction furnace is critical to ensure efficient operation, prevent equipment damage, and maintain consistent performance. Proper water quality helps in cooling the furnace components, particularly the induction coils and power electronics, which are sensitive to overheating. The water must meet specific standards in terms of purity, conductivity, temperature, and flow rate to avoid scaling, corrosion, or blockages in the cooling system. Regular monitoring and maintenance of the water system are essential to ensure the longevity and reliability of the furnace.
Key Points Explained:
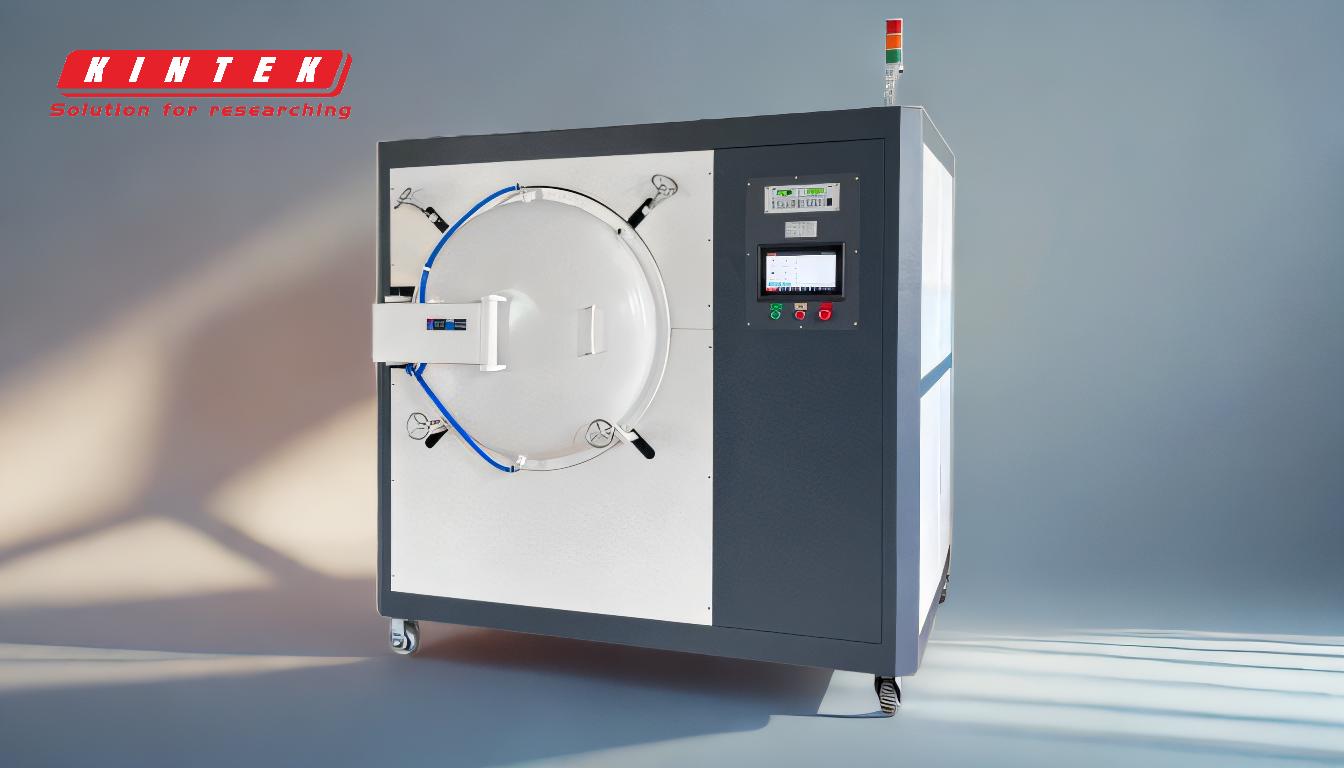
-
Importance of Water Quality in Induction Furnaces
- Water is used as a cooling medium in induction furnaces to dissipate heat generated during operation. Poor water quality can lead to scaling, corrosion, or biological growth, which can block cooling channels and reduce efficiency.
- High-quality water ensures optimal heat transfer, prevents overheating of critical components like induction coils and IGBT modules, and extends the lifespan of the furnace.
-
Key Water Quality Parameters
- Conductivity: The water should have low conductivity (typically less than 50 µS/cm) to prevent electrical leakage and minimize the risk of short circuits.
- pH Level: The ideal pH range is between 6.5 and 8.5. Water that is too acidic or alkaline can cause corrosion or scaling.
- Hardness: Water hardness should be less than 50 ppm (as CaCO3) to prevent the formation of scale deposits.
- Temperature: The inlet water temperature should be maintained between 20°C and 35°C to ensure effective cooling without causing thermal stress.
- Flow Rate: Adequate flow rate is necessary to maintain consistent cooling. The specific flow rate depends on the furnace's power rating and design.
-
Water Treatment Requirements
- Filtration: Use fine filters to remove suspended solids and particulates that could clog the cooling system.
- Deionization: Deionized water is often recommended to reduce conductivity and prevent mineral buildup.
- Chemical Treatment: Additives like corrosion inhibitors and biocides may be used to prevent corrosion and microbial growth, but these must be compatible with the furnace materials.
- Regular Maintenance: Periodic flushing and cleaning of the cooling system are necessary to remove any accumulated deposits or contaminants.
-
Consequences of Poor Water Quality
- Scaling: Mineral deposits can form on cooling surfaces, reducing heat transfer efficiency and causing localized overheating.
- Corrosion: Impurities in water can corrode metal components, leading to leaks and equipment failure.
- Blockages: Particulates or biological growth can block narrow cooling channels, disrupting the cooling process.
- Reduced Efficiency: Poor cooling can lead to increased energy consumption and reduced furnace performance.
-
Monitoring and Maintenance Practices
- Regularly test water quality parameters such as conductivity, pH, and hardness.
- Inspect the cooling system for signs of scaling, corrosion, or blockages.
- Replace filters and water treatment media as needed.
- Maintain a log of water quality measurements and maintenance activities for traceability.
-
Benefits of Maintaining Proper Water Quality
- Ensures consistent and efficient furnace operation.
- Reduces downtime and repair costs.
- Extends the lifespan of the furnace and its components.
- Improves safety by preventing overheating and electrical issues.
By adhering to these water quality standards and maintenance practices, operators can ensure the reliable and efficient performance of their IGBT induction furnace. Proper water management is a small but critical investment that pays off in terms of equipment longevity and operational efficiency.
Summary Table:
Parameter | Ideal Range | Purpose |
---|---|---|
Conductivity | < 50 µS/cm | Prevents electrical leakage and short circuits |
pH Level | 6.5 - 8.5 | Avoids corrosion and scaling |
Hardness | < 50 ppm (as CaCO3) | Prevents scale deposits |
Temperature | 20°C - 35°C | Ensures effective cooling without thermal stress |
Flow Rate | Depends on furnace design | Maintains consistent cooling |
Ensure your induction furnace operates at peak efficiency—contact our experts today for personalized guidance on water quality management!