Physical Vapor Deposition (PVD) is a vacuum-based coating process used to deposit thin films of material onto a substrate. The process involves converting a solid precursor material into a vapor phase, typically through methods like thermal evaporation or sputtering, and then condensing the vapor onto the substrate to form a thin, durable, and high-performance coating. PVD is widely used in industries requiring precise, high-quality coatings, such as electronics, optics, and tool manufacturing, due to its ability to produce thin films with excellent adhesion, uniformity, and resistance to wear and corrosion.
Key Points Explained:
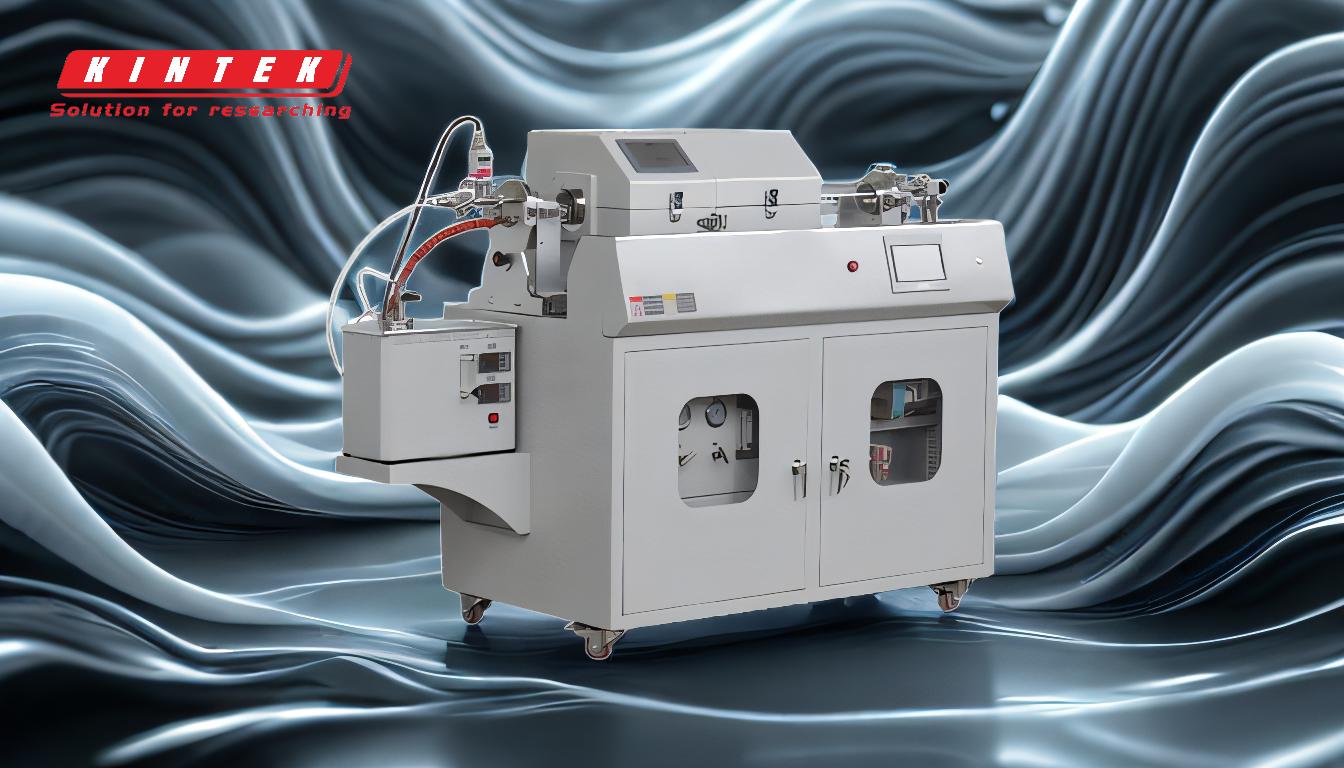
-
Basic Concept of PVD:
- PVD is a vacuum-based process where a solid material (precursor or target) is vaporized and then deposited onto a substrate to form a thin film.
- The vaporization of the solid material can be achieved through methods such as thermal evaporation, sputtering, or laser ablation.
- The process occurs in a vacuum chamber to minimize contamination and ensure precise control over the deposition.
-
Steps Involved in PVD:
- Vaporization: The solid precursor material is converted into a vapor phase using energy sources like high-power electricity, lasers, or thermal heating.
- Transport: The vaporized atoms or molecules travel through the vacuum chamber to the substrate.
- Condensation: The vapor condenses onto the substrate, forming a thin, uniform coating.
- Control: The thickness and rate of deposition are monitored and controlled using tools like quartz crystal rate monitors.
-
Key Methods of PVD:
- Thermal Evaporation: The target material is heated until it vaporizes, and the vapor is deposited onto the substrate.
- Sputtering: High-energy ions bombard the target material, dislodging atoms that then deposit onto the substrate.
- Laser Ablation: A laser is used to vaporize the target material, which then deposits onto the substrate.
-
Advantages of PVD:
- High-Quality Coatings: PVD produces thin films with excellent adhesion, uniformity, and durability.
- Versatility: It can deposit a wide range of materials, including metals, ceramics, and alloys.
- High Melting Point Materials: PVD is capable of handling materials with high melting points, which are difficult to process using other methods.
- Corrosion and Wear Resistance: The coatings are highly resistant to corrosion, wear, and high temperatures.
-
Applications of PVD:
- Electronics: Used for depositing conductive and insulating layers in semiconductor devices.
- Optics: Applied in the production of anti-reflective and reflective coatings for lenses and mirrors.
- Tool Manufacturing: Enhances the durability and performance of cutting tools and molds.
- Decorative Coatings: Used for creating scratch-resistant and aesthetically pleasing finishes on consumer products.
-
Environmental and Operational Considerations:
- Vacuum Conditions: PVD requires a high-vacuum environment to prevent contamination and ensure precise control over the deposition process.
- Low Temperatures: Unlike some other coating methods, PVD operates at relatively low temperatures, making it suitable for temperature-sensitive substrates.
- Energy Efficiency: While PVD requires significant energy for vaporization, it is generally considered environmentally friendly due to the lack of harmful byproducts.
-
Challenges and Limitations:
- Complex Equipment: PVD systems are often complex and require significant investment in equipment and maintenance.
- Limited Deposition Rates: The deposition rates can be slower compared to other coating methods, which may affect production throughput.
- Substrate Limitations: The process may not be suitable for all substrate materials, particularly those that cannot withstand vacuum conditions.
By understanding these key points, one can appreciate the working concept of PVD and its significance in modern manufacturing and technology. The process's ability to produce high-quality, durable coatings with precise control makes it a valuable technique across various industries.
Summary Table:
Aspect | Details |
---|---|
Process | Converts solid material into vapor, deposits onto substrate in a vacuum. |
Key Methods | Thermal Evaporation, Sputtering, Laser Ablation. |
Advantages | High-quality coatings, versatility, corrosion/wear resistance. |
Applications | Electronics, optics, tool manufacturing, decorative coatings. |
Challenges | Complex equipment, slower deposition rates, substrate limitations. |
Environmental Impact | Energy-efficient, no harmful byproducts, operates at low temperatures. |
Discover how PVD can enhance your manufacturing process—contact our experts today!