Hot isostatic pressing (HIP) is a manufacturing process that combines high temperature and high pressure to improve the properties of materials, such as eliminating porosity, enhancing density, and bonding materials. The process involves placing components or materials into a chamber, where they are subjected to uniform pressure and heat using inert gases like argon. This results in densification, sintering, and improved mechanical properties of the final product. The equipment is highly precise, controlled by computers, and customizable for various applications, including powder metallurgy, cladding, and the production of advanced materials like lithium batteries.
Key Points Explained:
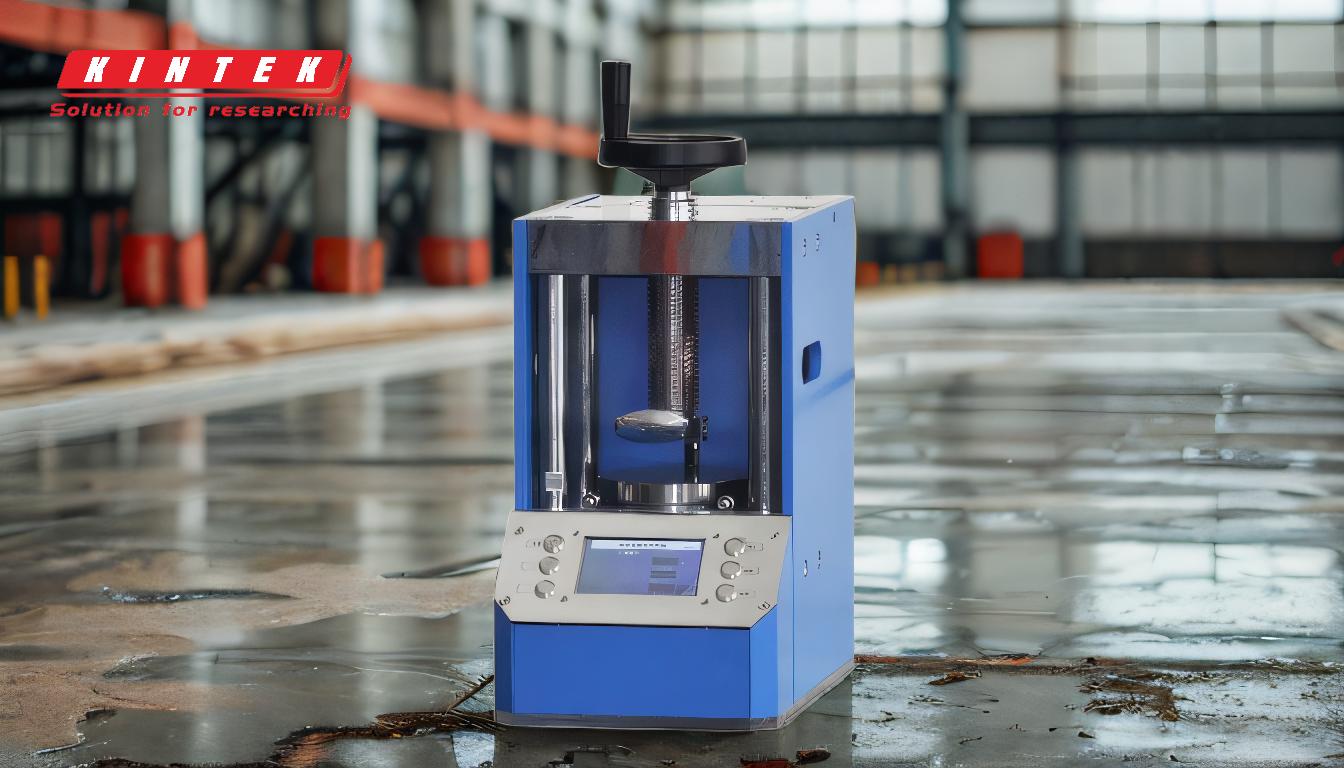
-
Process Overview:
- Hot isostatic pressing (HIP) involves loading components or materials into a chamber, which is then subjected to high temperature and uniform pressure.
- The process is controlled by computers, allowing precise regulation of temperature, pressure, and time to achieve desired material properties.
-
Uniform Pressure and Temperature:
- The cylindrical chamber ensures uniform pressure distribution, which is critical for achieving consistent results without altering the shape of the components.
- High temperature and pressure cause powder particles to move, undergo plastic deformation, and bond at the atomic level, leading to densification and sintering.
-
Material Transformation:
- In HIP, materials such as metal powders are pressed in a metal jacket. Under high temperature and pressure, the particles undergo processes like creep and diffusion, resulting in inter-atomic bonding and densification.
- This eliminates internal microporosity, creating materials with fine, uniform grain structures and isotropic properties.
-
Equipment Features:
- The warm isostatic press is a specialized version of HIP equipment, designed for applications requiring artificial pressure and custom modes for specific functions.
- It uses water or oil as thermal fluids for production and features external circulation heaters and touchscreen controls for user-friendly operation.
-
Applications:
- HIP is widely used in industries such as aerospace, automotive, and energy for producing high-performance components.
- It is also essential in the production of lithium batteries, where precise compression and heating are required.
-
Benefits of HIP:
- Improved mechanical properties, including enhanced fatigue life, ductility, impact strength, and toughness.
- Ability to bond or clad multiple materials, either in solid or powder form, creating composite structures with superior performance.
-
Process Steps:
- Loading parts into the heating chamber.
- Applying inert argon gas and heating the chamber.
- Monitoring and controlling temperature, pressure, and process time.
- Depressurizing and cooling the chamber to ensure safe removal of the processed parts.
By combining high temperature and pressure in a controlled environment, hot isostatic pressing transforms materials into high-density, high-performance components with superior mechanical properties. The process is versatile, precise, and essential for advanced manufacturing applications.
Summary Table:
Key Aspect | Details |
---|---|
Process Overview | Combines high temperature and uniform pressure to improve material properties. |
Uniform Pressure & Temp | Ensures consistent results without altering component shape. |
Material Transformation | Eliminates porosity, enhances density, and bonds materials at atomic level. |
Equipment Features | Computer-controlled, customizable, and user-friendly with touchscreen controls. |
Applications | Aerospace, automotive, energy, and lithium battery production. |
Benefits | Improved fatigue life, ductility, impact strength, and toughness. |
Process Steps | Loading, heating, monitoring, and cooling under controlled conditions. |
Learn how hot isostatic pressing can revolutionize your manufacturing process—contact us today!