An induction furnace operates on the principle of electromagnetic induction and the Joule effect, where an alternating current passed through a coil generates a magnetic field. This magnetic field induces eddy currents in a conductive metal charge placed within the coil, causing the metal to heat up due to its electrical resistance. The heat generated is localized within the metal itself, ensuring efficient and uniform heating or melting. The process involves converting electrical energy into heat energy without direct contact between the coil and the metal, making it a non-contact heating method. Induction furnaces are widely used in melting metals and creating precise alloys due to their efficiency and ability to generate high temperatures rapidly.
Key Points Explained:
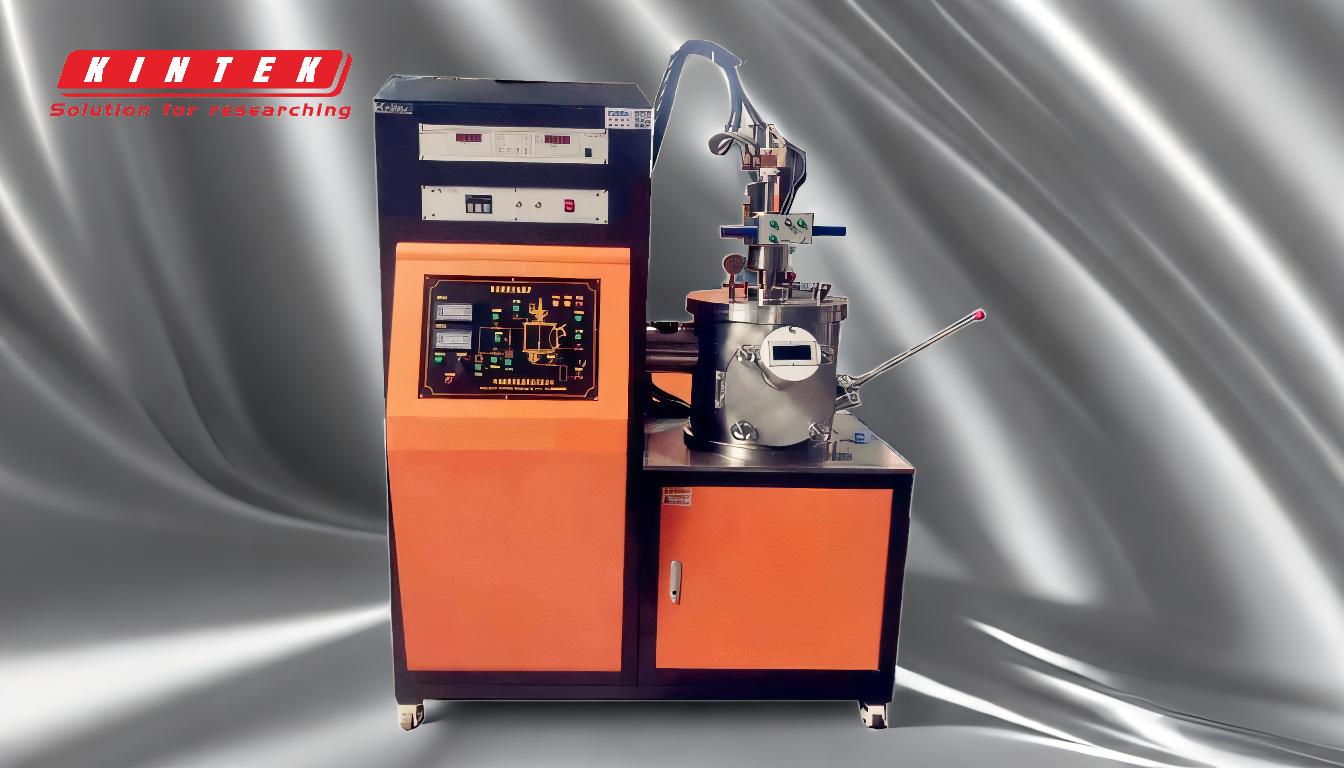
-
Electromagnetic Induction:
- An induction furnace uses electromagnetic induction to generate heat within a conductive metal charge.
- An alternating current (AC) is passed through a hollow copper coil, creating a powerful electromagnetic field around it.
- When a conductive metal is placed within this field, the changing magnetic field induces eddy currents within the metal.
-
Eddy Currents and Joule Heating:
- The eddy currents induced in the metal flow in closed loops, generating heat due to the metal's electrical resistance (Joule effect).
- This heat is produced directly within the metal, ensuring rapid and efficient heating or melting.
- The furnace surfaces may become warm, but the primary heat generation occurs within the metal charge itself.
-
Power Conversion and Frequency:
- The induction furnace operates by converting standard power frequency (50 Hz) alternating current into medium frequency (300 Hz to 10,000 Hz) using a power supply device.
- This conversion involves rectifying the AC into direct current (DC) and then inverting it into adjustable medium frequency AC.
- Higher frequencies increase the efficiency of heat generation and allow for precise control over the heating process.
-
Transformer Principle:
- The furnace operates on a transformer-like principle, where the primary winding is the induction coil, and the metal charge acts as the secondary winding.
- The alternating current in the primary coil induces a current in the metal charge, which heats up due to its resistance.
- The primary coil is typically cooled by circulating water to prevent overheating.
-
Non-Contact Heating:
- Induction furnaces use non-contact heating, meaning the induction coil does not physically touch the metal charge.
- Heat is generated internally within the metal, ensuring uniform heating and minimizing contamination or oxidation.
- This method is ideal for melting metals and creating precise alloys with controlled compositions.
-
Components of an Induction Furnace:
- Induction Coil: A hollow copper coil that carries the alternating current and generates the electromagnetic field.
- Power Supply Unit: Converts standard AC into medium frequency AC for efficient induction heating.
- Cooling System: Circulates water or another coolant to maintain the temperature of the induction coil.
- Furnace Chamber: Contains the metal charge and is designed to withstand high temperatures and thermal stresses.
-
Applications of Induction Furnaces:
- Induction furnaces are widely used in metalworking industries for melting and alloying metals such as steel, iron, aluminum, and copper.
- They are preferred for their ability to achieve precise temperature control, rapid heating, and energy efficiency.
- Induction furnaces are also used in foundries, laboratories, and recycling facilities for processing scrap metal.
-
Advantages of Induction Furnaces:
- Energy Efficiency: Heat is generated directly within the metal, minimizing energy loss.
- Precision: Allows for precise control over temperature and heating rates.
- Cleanliness: Non-contact heating reduces contamination and oxidation.
- Speed: Rapid heating and melting capabilities improve productivity.
- Versatility: Suitable for a wide range of metals and alloys.
By understanding these key points, one can appreciate the working principle of an induction furnace and its significance in modern industrial processes. The combination of electromagnetic induction, Joule heating, and advanced power conversion technologies makes induction furnaces a cornerstone of efficient and precise metal processing.
Summary Table:
Key Aspect | Details |
---|---|
Principle | Electromagnetic induction and Joule heating |
Heating Method | Non-contact, internal heat generation within the metal |
Frequency Range | 300 Hz to 10,000 Hz (medium frequency) |
Main Components | Induction coil, power supply unit, cooling system, furnace chamber |
Applications | Melting metals (steel, iron, aluminum, copper), alloy creation, recycling |
Advantages | Energy efficiency, precision, cleanliness, speed, versatility |
Discover how an induction furnace can revolutionize your metal processing—contact us today for expert guidance!