Thermal evaporation deposition pressure refers to the vacuum environment required during the thermal evaporation process, a key physical vapor deposition (PVD) technique. This pressure is critical for ensuring the purity and quality of the deposited thin film. In thermal evaporation, a high vacuum environment (typically around 10^-6 Torr) is maintained to minimize contamination from background gases, which can degrade the performance of devices like OLEDs and organic photovoltaic cells. The process involves heating the source material to its vaporization point, creating a vapor stream that condenses on the substrate to form a thin film. The pressure directly influences the deposition rate, film purity, and overall process efficiency.
Key Points Explained:
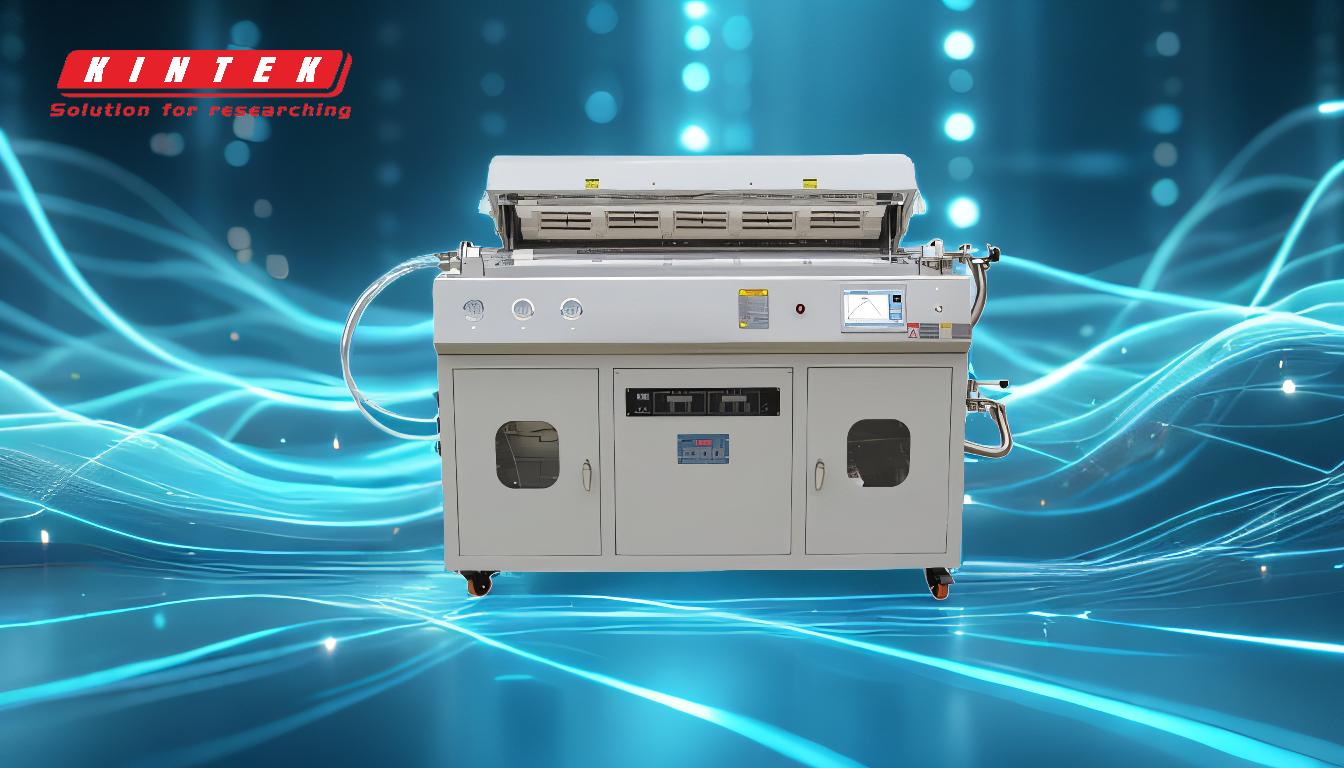
-
Definition of Thermal Evaporation Deposition Pressure:
- Thermal evaporation deposition pressure refers to the vacuum level maintained in the chamber during the thermal evaporation process. This pressure is crucial for creating a clean environment that minimizes contamination from residual gases, ensuring high-quality thin film deposition.
-
Role of Pressure in Thermal Evaporation:
- Film Purity: Lower pressures, typically around 10^-6 Torr, reduce the presence of background gases that can contaminate the film. This is especially important for sensitive applications like OLEDs and organic photovoltaic devices.
- Deposition Rate: The pressure affects the mean free path of the vaporized particles. At lower pressures, particles travel longer distances without collisions, leading to a more uniform and efficient deposition process.
- Process Efficiency: Maintaining optimal pressure ensures that the material vaporizes and condenses effectively, improving the overall efficiency of the deposition process.
-
Importance of High Vacuum Environment:
- A high vacuum environment is essential for thermal evaporation because it prevents oxidation and contamination of the source material and the substrate. This is particularly important for materials that are sensitive to reactive gases, such as organic compounds used in OLEDs.
-
Factors Influencing Thermal Evaporation Pressure:
- Material Properties: The vapor pressure of the source material at a given temperature determines the required vacuum level. Materials with higher vapor pressures can be evaporated at lower temperatures, but still require a high vacuum to ensure purity.
- Application Requirements: The desired film properties, such as thickness, uniformity, and purity, dictate the optimal pressure settings. For example, high-performance electronic devices require extremely low pressures to achieve the necessary film quality.
-
Comparison with Other Deposition Techniques:
- Unlike chemical vapor deposition (CVD), which relies on reactive gases and precursors, thermal evaporation is a purely physical process. This makes it simpler and more cost-effective, but also necessitates precise control of the vacuum environment to achieve high-quality results.
-
Practical Considerations for Equipment and Consumables:
- Vacuum Pumps: High-performance vacuum pumps are essential for achieving and maintaining the required low pressures. These pumps must be capable of reaching and sustaining pressures of 10^-6 Torr or lower.
- Chamber Design: The deposition chamber must be designed to minimize leaks and outgassing, which can introduce contaminants. Materials used in the chamber should be compatible with high vacuum conditions.
- Source Material: The choice of source material is critical, as it must have suitable vapor pressure characteristics for the desired deposition rate and film quality. Materials with low vapor pressures may require higher temperatures, which can increase energy consumption and equipment wear.
-
Applications of Thermal Evaporation:
- Thermal evaporation is widely used in the fabrication of thin films for electronic devices, including OLEDs, thin-film transistors, and solar cells. The ability to deposit high-purity films at relatively low temperatures makes it a preferred method for these applications.
-
Challenges and Solutions:
- Contamination Control: Maintaining a high vacuum is challenging, especially in large-scale production. Advanced vacuum systems and regular maintenance are necessary to minimize contamination.
- Material Limitations: Some materials are difficult to evaporate due to their high melting points or low vapor pressures. In such cases, alternative deposition methods, such as electron beam evaporation, may be used.
By understanding the role of pressure in thermal evaporation, equipment and consumable purchasers can make informed decisions about the necessary components and systems to achieve optimal deposition results. For more detailed information on thermal evaporation, you can refer to this resource: thermal evaporation.
Summary Table:
Aspect | Details |
---|---|
Definition | Vacuum level in the chamber during thermal evaporation (typically ~10^-6 Torr). |
Role of Pressure | - Ensures film purity by minimizing contamination. - Enhances deposition rate and process efficiency. |
High Vacuum Importance | Prevents oxidation and contamination, critical for sensitive materials. |
Key Factors | - Material properties (vapor pressure). - Application requirements (film quality). |
Applications | OLEDs, thin-film transistors, solar cells, and other electronic devices. |
Challenges | Contamination control and material limitations. |
Optimize your thermal evaporation process with expert guidance—contact us today for tailored solutions!