Thermal evaporation in a vacuum pressure is a widely used physical vapor deposition (PVD) technique for creating thin films. It involves heating a solid material in a high vacuum environment until it reaches its evaporation point, producing a vapor stream. This vapor then travels through the vacuum chamber and condenses onto a substrate, forming a thin film. The process relies on thermal energy to break atomic bonds in the material, allowing atoms or molecules to escape and deposit onto the target surface. This method is often referred to as resistive evaporation because heat is generated by passing an electric current through a resistive element, such as a boat or coil, which holds the material.
Key Points Explained:
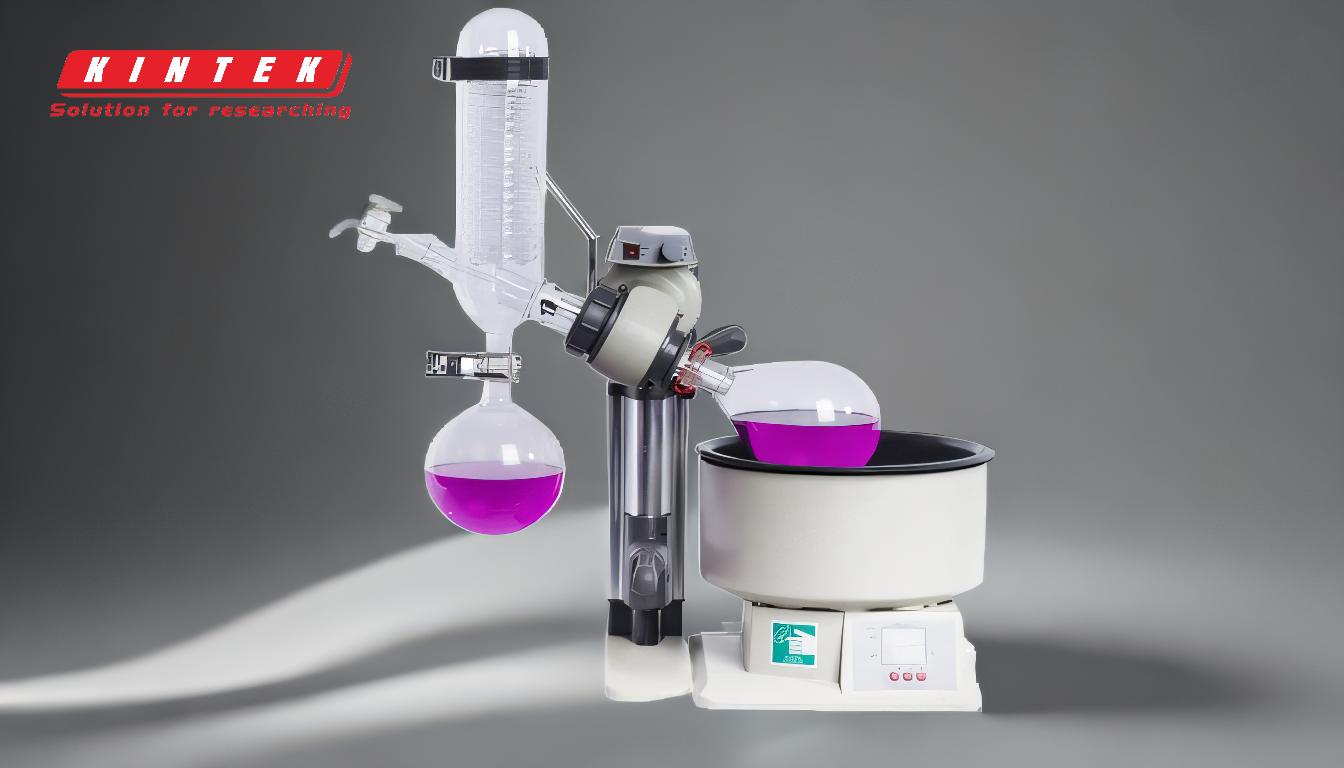
-
Definition and Purpose of Thermal Evaporation:
- Thermal evaporation is a PVD process used to deposit thin films of materials onto substrates.
- It is commonly employed in industries such as semiconductors, optics, and electronics for creating coatings with precise thickness and uniformity.
-
The Role of Vacuum Pressure:
- The process takes place in a high vacuum chamber to minimize contamination and ensure a clean deposition environment.
- Vacuum pressure reduces the presence of gas molecules, allowing the evaporated material to travel unimpeded to the substrate.
-
Heating Mechanism:
- The target material is heated using resistive heating elements, such as boats, coils, or baskets, which are made of materials like tungsten or molybdenum.
- Electrical current passes through these elements, generating heat that melts and evaporates the target material.
-
Evaporation and Vapor Formation:
- As the material is heated, it gains sufficient thermal energy to break atomic bonds, transitioning from a solid to a vapor phase.
- The vaporized atoms or molecules form a vapor stream that moves through the vacuum chamber.
-
Deposition onto the Substrate:
- The vapor stream travels to the substrate, where it condenses and forms a thin film.
- The substrate is typically positioned above the evaporation source to ensure uniform coating.
-
Advantages of Thermal Evaporation:
- High deposition rates and efficiency.
- Ability to deposit a wide range of materials, including metals, alloys, and some compounds.
- Simple and cost-effective equipment compared to other PVD methods.
-
Limitations and Challenges:
- Limited to materials with relatively low melting points.
- Difficulty in achieving precise stoichiometry for compound materials.
- Potential for contamination if the vacuum environment is not properly maintained.
-
Applications:
- Used in the production of optical coatings, such as anti-reflective and reflective layers.
- Essential in the fabrication of thin-film solar cells and semiconductor devices.
- Applied in the creation of decorative and protective coatings for various products.
By understanding these key points, one can appreciate the fundamental principles and practical considerations of thermal evaporation in a vacuum pressure environment. This method remains a cornerstone of thin-film technology due to its simplicity, versatility, and effectiveness.
Summary Table:
Aspect | Details |
---|---|
Definition | A PVD technique for depositing thin films by heating materials in a vacuum. |
Key Components | Vacuum chamber, resistive heating elements (boats/coils), substrate. |
Advantages | High deposition rates, cost-effective, versatile material compatibility. |
Limitations | Limited to low-melting-point materials, potential contamination risks. |
Applications | Optical coatings, thin-film solar cells, semiconductor devices. |
Discover how thermal evaporation can enhance your thin-film processes—contact our experts today!