Thin film deposition by plasma is a sophisticated process used to apply thin layers of material onto a substrate within a vacuum chamber. This technique is crucial for creating coatings that enhance the properties of the substrate, such as electrical insulation, optical transmission, and corrosion resistance. The process can be categorized into methods like Physical Vapor Deposition (PVD) and Chemical Vapor Deposition (CVD), each involving specific steps to ensure the desired characteristics of the thin film. Plasma-enhanced methods, including the use of remote plasma sources, allow for the extraction of reactive species without exposing the substrate to harmful ions and electrons, thus minimizing defects and impurities. This method is essential in industries requiring precise and high-quality thin film coatings.
Key Points Explained:
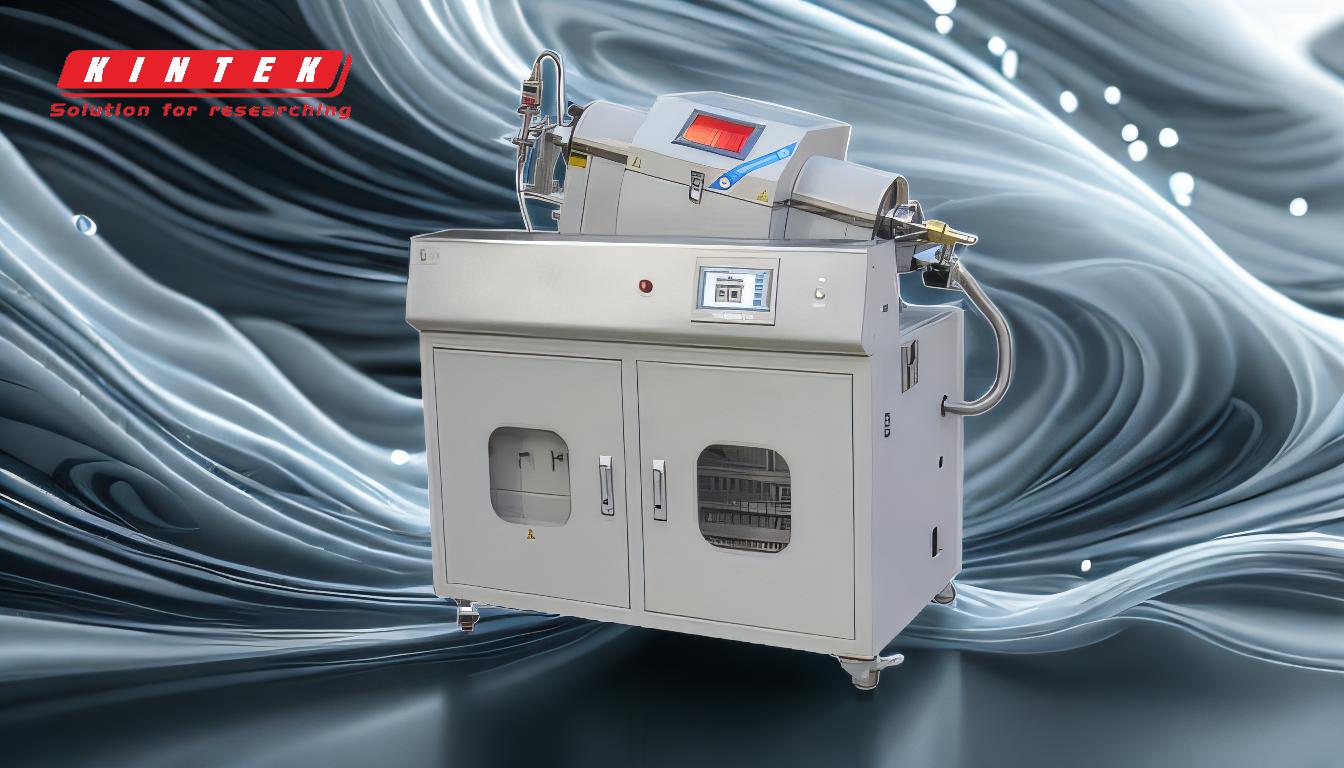
-
Definition and Purpose of Thin Film Deposition by Plasma:
- Thin film deposition by plasma involves creating a thin layer of material on a substrate within a vacuum environment. This process is used to enhance the substrate's properties, such as improving electrical insulation, optical transmission, and corrosion resistance.
-
Common Techniques:
- Physical Vapor Deposition (PVD): This method uses thermodynamic or mechanical means to deposit thin films, typically requiring a low-pressure environment to achieve accurate and functional results.
- Chemical Vapor Deposition (CVD): This technique involves chemical reactions to produce the thin film on the substrate surface.
-
Basic Steps in Thin Film Deposition:
- Selection of Material Source: A pure material source (target) is chosen based on the desired properties of the thin film.
- Transportation of Target: The target material is transported to the substrate through a medium, which can be a fluid or a vacuum.
- Deposition: The target material is deposited onto the substrate to form a thin film.
- Post-Deposition Treatment: The film may undergo annealing or heat treatment to enhance its properties.
- Analysis and Modification: The properties of the deposited film are analyzed, and the deposition process may be modified based on the results to achieve the desired characteristics.
-
Role of Plasma in Thin Film Deposition:
- Remote Plasma Sources: These sources allow reactive species to be extracted and fed into the thin film process without exposing the substrate to the plasma. This method helps in avoiding defects and impurities that could be caused by free ions and electrons bombarding the growing film.
- Plasma-Enhanced Deposition: The use of plasma can enhance the deposition process by providing energy to the reactants, leading to better film quality and adherence.
-
Applications and Benefits:
- Industrial Applications: Thin film deposition is widely used in various industries, including electronics, optics, and materials science, to improve the performance and durability of substrates.
- Enhanced Properties: The coatings can provide essential properties such as electrical insulation, optical transmission, and corrosion resistance, which are critical for the functionality of many devices and materials.
By understanding these key points, one can appreciate the complexity and importance of thin film deposition by plasma in modern technology and industry. The precise control over the deposition process ensures that the thin films meet the required specifications, making this technique indispensable in the fabrication of high-performance materials and devices.
Summary Table:
Aspect | Details |
---|---|
Definition | Process of applying thin material layers on a substrate in a vacuum chamber. |
Purpose | Enhances substrate properties (e.g., electrical insulation, corrosion resistance). |
Common Techniques | - Physical Vapor Deposition (PVD) |
- Chemical Vapor Deposition (CVD) | |
Key Steps | 1. Material selection |
- Target transportation
- Deposition
- Post-treatment
- Analysis & modification | | Role of Plasma | - Remote plasma sources minimize defects.
- Plasma-enhanced methods improve film quality. | | Applications | Electronics, optics, materials science, and more. |
Discover how thin film deposition by plasma can elevate your projects—contact our experts today!