Vacuum deposition of aluminum is a specialized coating process where aluminum is deposited onto a substrate in a vacuum environment. This technique involves evaporating solid aluminum under low pressure, allowing the aluminum atoms or molecules to travel freely and adhere to the target surface without interference from air molecules. The process is widely used to create thin, uniform layers of aluminum on various materials, enhancing properties such as reflectivity, conductivity, and corrosion resistance. Applications include manufacturing mirrors, optical components, and protective coatings for plastics. The vacuum environment ensures precise control over the deposition process, enabling high-quality, durable coatings.
Key Points Explained:
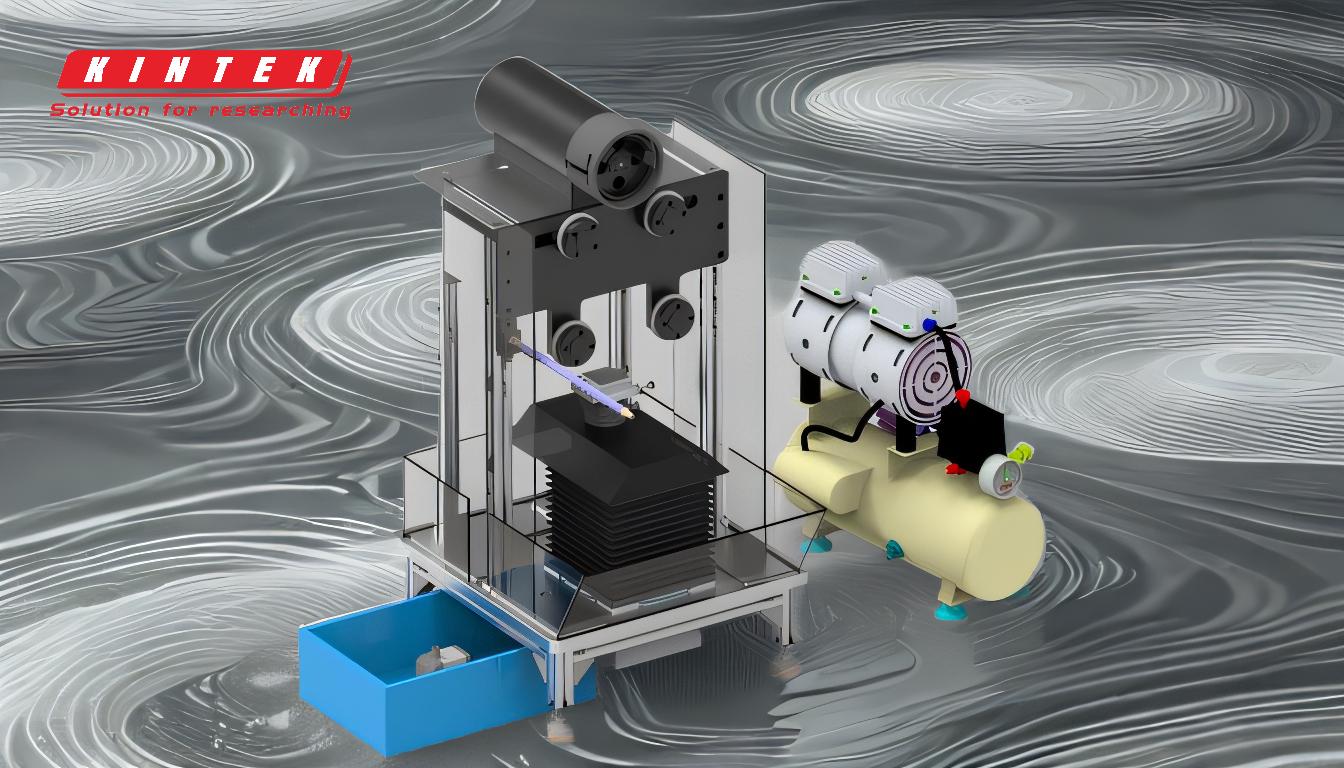
-
Definition of Vacuum Deposition of Aluminum:
- Vacuum deposition of aluminum is a process where aluminum is evaporated in a vacuum chamber and deposited onto a substrate. The vacuum environment minimizes the presence of gas molecules, allowing aluminum atoms or molecules to travel unimpeded and form a thin, uniform layer on the target surface.
-
How the Process Works:
- The process begins by placing the substrate (e.g., glass, plastic, or metal) and solid aluminum in a vacuum chamber.
- The chamber is evacuated to remove air and other gases, creating a low-pressure environment.
- Aluminum is heated until it evaporates, producing a vapor of aluminum atoms or molecules.
- The aluminum vapor travels through the vacuum and condenses onto the substrate, forming a thin, even coating.
-
Key Advantages of Vacuum Deposition:
- Precision and Control: The vacuum environment allows for precise control over the deposition process, enabling the creation of ultra-thin layers, even at the nanometer scale.
- Uniformity: The absence of air molecules ensures that the aluminum coating is uniform and free from defects.
- Versatility: This process can be used on a wide range of substrates, including plastics, metals, and glass.
- Enhanced Material Properties: Aluminum coatings improve properties such as reflectivity (e.g., in mirrors), electrical conductivity, and corrosion resistance.
-
Applications of Vacuum-Deposited Aluminum:
- Optical Components: Used to create reflective surfaces in mirrors, telescopes, and other optical devices.
- Packaging: Aluminum coatings are applied to plastic films for food packaging to provide a barrier against moisture and oxygen.
- Electronics: Used in the production of conductive layers for electronic components and displays.
- Protective Coatings: Applied to plastics and metals to enhance durability and resistance to environmental factors.
-
Comparison to Other Coating Methods:
- Unlike electroplating, which involves chemical reactions and requires conductive substrates, vacuum deposition is a physical process that can be used on non-conductive materials like plastics.
- Compared to chemical vapor deposition (CVD), vacuum deposition operates at lower temperatures, making it suitable for heat-sensitive materials.
-
Environmental and Operational Considerations:
- The vacuum environment eliminates the need for chemical solvents, reducing environmental impact.
- The process requires specialized equipment, such as vacuum chambers and evaporation sources, which can be costly but offer long-term benefits in terms of coating quality and durability.
-
Challenges and Limitations:
- Equipment Costs: The need for vacuum chambers and high-precision equipment can make the process expensive.
- Substrate Compatibility: While versatile, some materials may not adhere well to aluminum coatings without additional surface treatments.
- Process Complexity: Achieving consistent results requires careful control of parameters such as vacuum pressure, temperature, and deposition rate.
By understanding these key points, equipment and consumable purchasers can evaluate whether vacuum deposition of aluminum is the right solution for their specific needs, considering factors such as cost, application requirements, and desired material properties.
Summary Table:
Key Aspect | Details |
---|---|
Process | Aluminum is evaporated in a vacuum chamber and deposited onto a substrate. |
Advantages | Precision, uniformity, versatility, enhanced material properties. |
Applications | Optical components, packaging, electronics, protective coatings. |
**Comparison to Other Methods | No chemical reactions, lower temperatures, suitable for non-conductive materials. |
Challenges | High equipment costs, substrate compatibility, process complexity. |
Discover how vacuum deposition of aluminum can benefit your projects—contact us today for expert guidance!