Vacuum deposition of metal is a precise and versatile process used to apply thin layers of material onto a substrate in a vacuum environment. This technique allows for the deposition of materials at the atomic or molecular level, enabling the creation of coatings with specific properties such as optical performance, conductivity, corrosion resistance, and wear resistance. The process is widely used in industries ranging from electronics and solar energy to automotive and packaging. By operating under vacuum conditions, the process minimizes contamination and ensures high-quality, uniform coatings. Applications include the production of thin-film solar cells, microchips, LEDs, and decorative or functional coatings.
Key Points Explained:
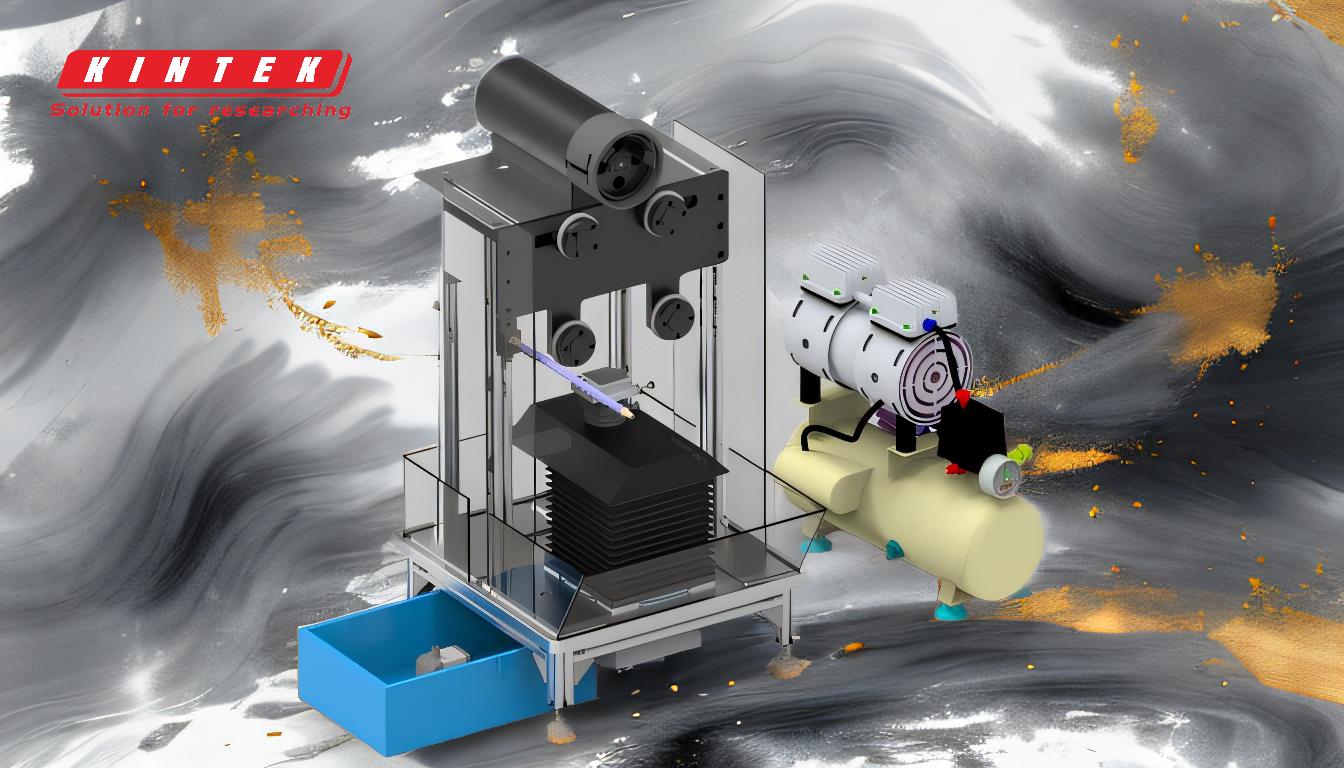
-
Definition and Process of Vacuum Deposition
- Vacuum deposition, also known as vacuum evaporation, involves depositing material onto a substrate in a vacuum or low-pressure environment.
- The process deposits atoms or molecules one at a time, creating layers that can range from a single atom to several millimeters in thickness.
- It is a clean and controlled method, as the absence of gas molecules reduces contamination and ensures uniformity.
-
Types of Vacuum Deposition Techniques
- Physical Vapor Deposition (PVD): A common method where material is vaporized from a solid source and then deposited onto the substrate.
- Low-Pressure Chemical Vapor Deposition (LPCVD): Involves chemical reactions at low pressures to deposit thin films.
- Other variations include sputtering and evaporation, each suited for specific applications and materials.
-
Applications of Vacuum Deposition
- Electronics: Used to create conductive metal patterns in microchips, LEDs, and solar cells.
- Optical Coatings: Produces mirror coatings, interference coatings, and anti-reflective layers.
- Energy: Enhances the efficiency and durability of thin-film solar cells by improving conductivity and light absorption.
- Automotive and Packaging: Provides wear-resistant, corrosion-resistant, and barrier coatings for functional and decorative purposes.
-
Advantages of Vacuum Deposition
- Precision: Allows for the deposition of ultra-thin layers, even in the nanometer range.
- Uniformity: Ensures consistent and high-quality coatings across the substrate.
- Versatility: Suitable for a wide range of materials and applications.
- Clean Environment: Reduces contamination, making it ideal for sensitive industries like semiconductors and optics.
-
Materials and Properties Enhanced by Vacuum Deposition
- Metals: Commonly used for conductive and reflective coatings.
- Inorganic Materials: Applied for corrosion resistance and durability.
- Functional Coatings: Improve properties such as conductivity, optical performance, and wear resistance.
-
Industrial Significance
- Vacuum deposition is a cornerstone of modern manufacturing, enabling advancements in electronics, renewable energy, and materials science.
- Its ability to produce high-performance coatings at scale makes it indispensable for industries requiring precision and reliability.
By understanding these key points, a purchaser of equipment or consumables can better evaluate the suitability of vacuum deposition for their specific needs, ensuring optimal performance and cost-effectiveness.
Summary Table:
Aspect | Details |
---|---|
Process | Deposits materials at atomic/molecular levels in a vacuum environment. |
Techniques | PVD, LPCVD, sputtering, evaporation. |
Applications | Electronics (microchips, LEDs), optical coatings, solar cells, automotive, packaging. |
Advantages | Precision, uniformity, versatility, clean environment. |
Materials Enhanced | Metals (conductive/reflective), inorganic materials (corrosion resistance), functional coatings. |
Industrial Significance | Key for electronics, renewable energy, and materials science advancements. |
Learn how vacuum deposition can elevate your manufacturing process—contact our experts today!