A vacuum furnace is a versatile piece of equipment used across various industries for processes that require a controlled, contaminant-free environment. Its primary applications include ceramic firing, vacuum smelting, degassing of electric vacuum parts, annealing, brazing of metal parts, and ceramic-metal sealing. The furnace operates under a vacuum or inert atmosphere, ensuring that materials are processed without oxidation or contamination. This makes it ideal for heat treatments like quenching, tempering, and annealing, as well as advanced processes such as vacuum sintering and brazing. Additionally, specialized types like vacuum hot press furnaces and horizontal vacuum furnaces cater to specific needs in powder metallurgy, advanced ceramics, and composite material preparation. The vacuum system, comprising components like vacuum valves and pumps, ensures precise control over the environment, achieving high vacuum degrees for optimal results.
Key Points Explained:
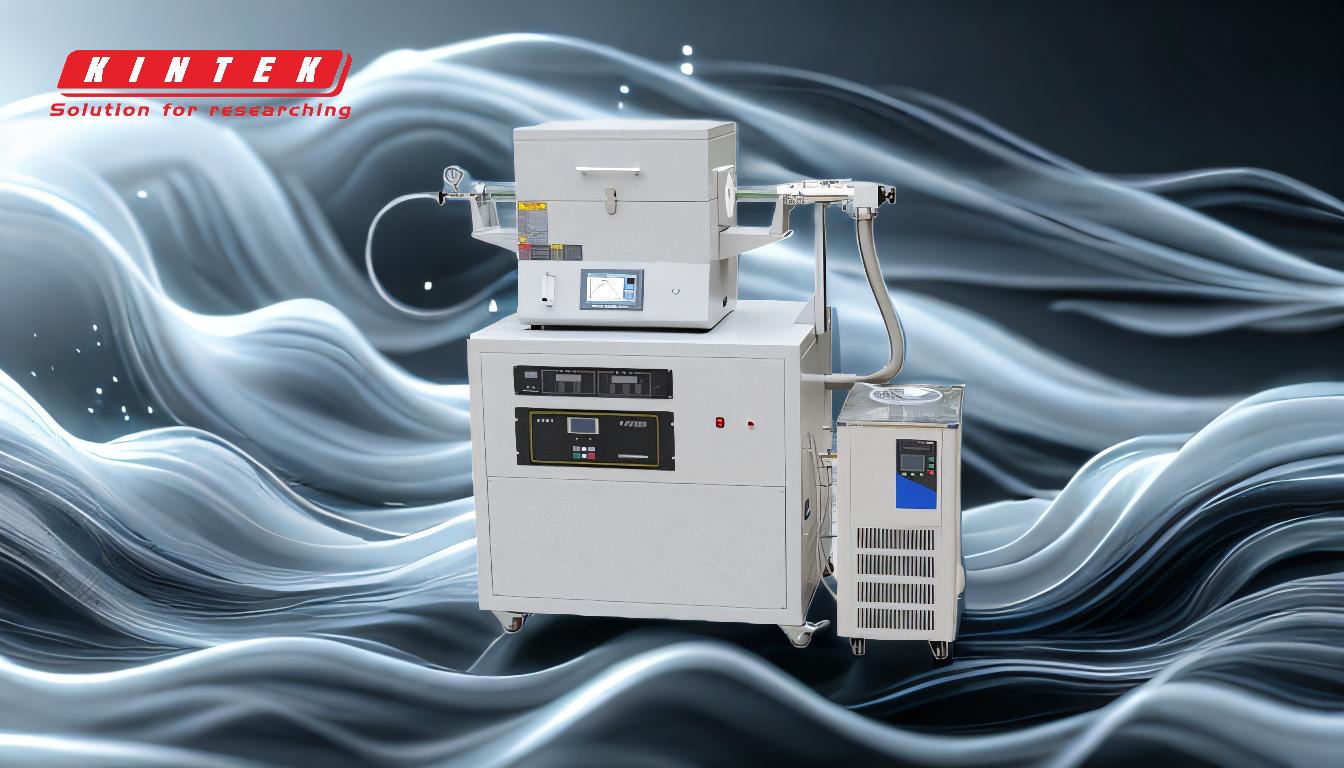
-
Primary Applications of a Vacuum Furnace:
- Ceramic Firing: Used to fire ceramics in a controlled environment, ensuring high-quality results without contamination.
- Vacuum Smelting: Ideal for melting metals and alloys under vacuum conditions to prevent oxidation and impurities.
- Degassing of Electric Vacuum Parts: Removes trapped gases from components, enhancing their performance and longevity.
- Annealing: A heat treatment process that softens materials, improves ductility, and reduces internal stresses.
- Brazing: Joins metal parts using a filler metal that melts at a lower temperature than the base metals, ensuring strong, clean joints.
- Ceramic-Metal Sealing: Used in electronics and aerospace industries to create hermetic seals between ceramics and metals.
-
Heat Treatment Processes:
- Vacuum Quenching: Rapid cooling of materials to achieve desired hardness and strength.
- Tempering: Reheating quenched materials to reduce brittleness and improve toughness.
- Annealing: Heating and slow cooling to refine grain structure and enhance material properties.
-
Vacuum Sintering:
- A process where metal powder products are heated under vacuum to sinter adjacent metal powder grains into solid parts. This is critical in powder metallurgy and advanced material preparation.
-
Vacuum Brazing:
- A joining process where parts are heated to a temperature above the filler metal's melting point but below the base metal's melting point. This ensures a clean, strong bond without oxidation.
-
Specialized Vacuum Furnaces:
- Vacuum Hot Press Furnace: Combines high temperature and pressure for applications in powder metallurgy, ceramic preparation, and composite material processing. It achieves better densification and performance in materials.
- Horizontal Vacuum Furnace: Suitable for heat treatments, sintering, advanced ceramics, and aluminizing. It can operate in argon atmospheres and high-purity vacuums, making it ideal for heat-treating metals and alloys.
-
Vacuum System Components:
- The vacuum system includes vacuum valves, mechanical pumps, diffusion pumps, and Roots pumps. These components work together to achieve and maintain high vacuum degrees, typically up to 7 × 10^-3 Pa, ensuring a contaminant-free environment.
-
Advantages of Vacuum Furnaces:
- Elimination of Impurities: The vacuum environment ensures that workpiece surfaces remain clean, bright, and free from transmutation.
- Wide Industry Applications: Used in material science, electronics, metallurgy, and chemical industries for processes like sintering, annealing, and heat treatment.
- Precision and Control: The ability to operate under precise vacuum conditions allows for consistent, high-quality results in material modification, preparation, and research.
For more detailed information on vacuum furnaces, visit vacuum furnace.
Summary Table:
Application | Description |
---|---|
Ceramic Firing | Fires ceramics in a controlled, contamination-free environment. |
Vacuum Smelting | Melts metals and alloys under vacuum to prevent oxidation and impurities. |
Degassing of Electric Vacuum Parts | Removes trapped gases to enhance component performance and longevity. |
Annealing | Softens materials, improves ductility, and reduces internal stresses. |
Brazing | Joins metal parts using a filler metal for strong, clean joints. |
Ceramic-Metal Sealing | Creates hermetic seals between ceramics and metals in electronics and aerospace. |
Interested in learning more about vacuum furnaces? Contact our experts today for tailored solutions!