Vacuum casting is a manufacturing process used to create high-quality replicas of original parts using silicone molds. The process involves pouring liquid material, typically polyurethane resin, into a silicone mold under vacuum conditions to eliminate air bubbles and ensure precise replication. The mold itself is held together by a combination of physical design, material properties, and the vacuum environment. The silicone mold's flexibility and durability allow it to maintain its shape during the casting process, while the vacuum pressure ensures that the mold remains tightly closed, preventing any material leakage or deformation. This combination of factors ensures that the mold stays intact and produces accurate, high-quality parts.
Key Points Explained:
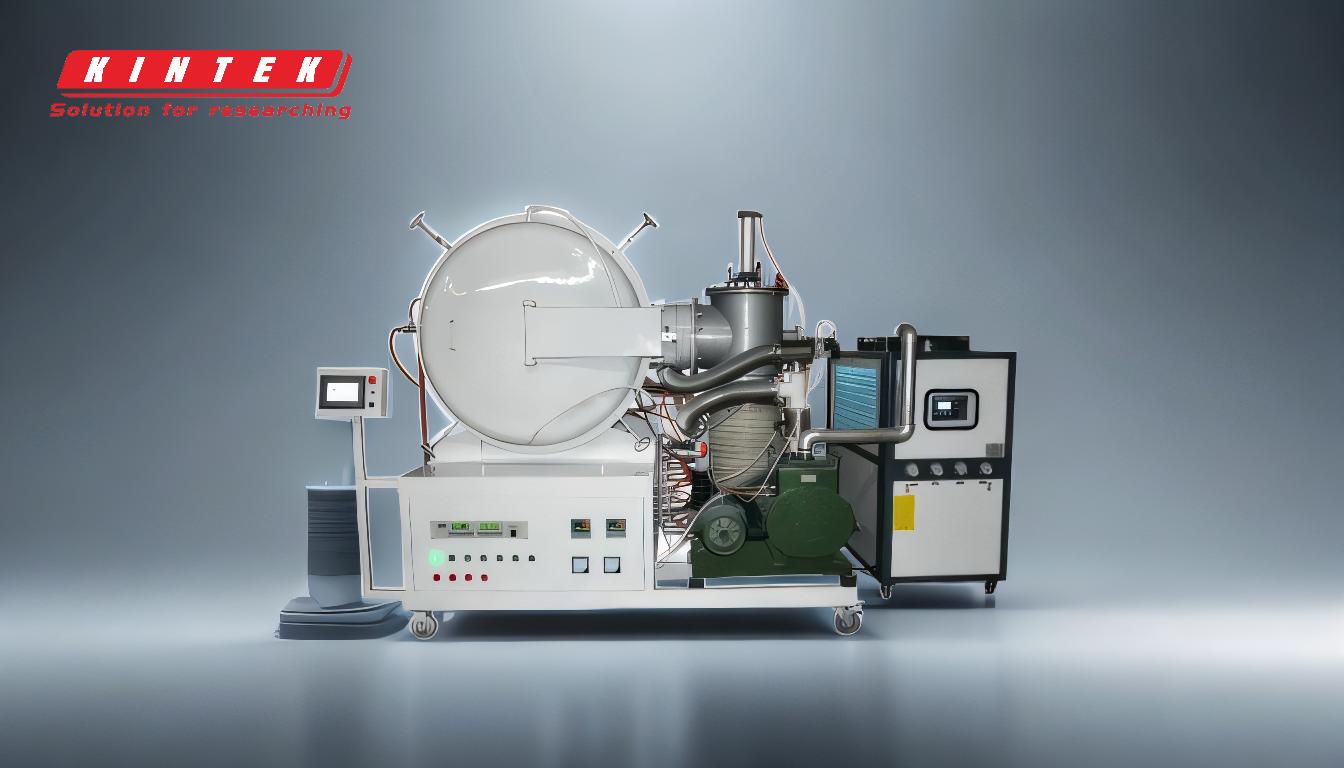
-
Silicone Mold Design and Material Properties:
- Silicone molds are designed with a specific geometry that allows them to hold their shape during the vacuum casting process. The mold is typically split into two or more parts, which are aligned and clamped together.
- The silicone material used for the mold is flexible yet durable, allowing it to withstand the vacuum pressure and the curing process without tearing or deforming.
- The mold's flexibility also enables easy demolding of the finished part without damaging the mold or the part.
-
Vacuum Pressure:
- The vacuum environment plays a crucial role in keeping the mold together. The vacuum chamber creates a low-pressure environment that ensures the mold remains tightly closed during the casting process.
- The vacuum pressure helps eliminate air bubbles from the liquid resin, ensuring a smooth and precise replication of the part. This pressure also prevents the mold from shifting or opening during the process.
-
Clamping Mechanism:
- In addition to the vacuum pressure, molds are often held together using clamps or other mechanical fasteners. These clamps ensure that the mold halves remain tightly sealed, preventing any material from leaking out during the casting process.
- The clamping mechanism is designed to apply even pressure across the mold, ensuring that it stays together uniformly and does not distort under the vacuum pressure.
-
Mold Alignment and Sealing:
- Proper alignment of the mold halves is critical to maintaining the mold's integrity. Misalignment can lead to gaps or uneven surfaces, which can cause defects in the final part.
- The mold is designed with precise alignment features, such as pins or grooves, to ensure that the halves fit together perfectly. Additionally, the silicone material itself acts as a seal, preventing any resin from escaping during the casting process.
-
Curing Process:
- Once the resin is poured into the mold, the curing process begins. The mold must remain closed and intact during this phase to ensure that the resin sets correctly and the part retains its desired shape.
- The vacuum environment and clamping mechanism work together to maintain the mold's integrity throughout the curing process, ensuring that the final part is free from defects and accurately replicates the original design.
-
Durability and Reusability:
- Silicone molds are designed to be durable and reusable, capable of producing multiple parts before needing replacement. The material's resilience allows it to withstand repeated use under vacuum conditions without losing its shape or integrity.
- The combination of the mold's design, material properties, and the vacuum environment ensures that the mold remains intact and functional over multiple casting cycles.
In summary, the mold in vacuum casting is kept together through a combination of its design, material properties, vacuum pressure, clamping mechanisms, and proper alignment. These factors work in harmony to ensure that the mold remains intact and produces high-quality, precise parts during the casting process.
Summary Table:
Key Factor | Role in Mold Integrity |
---|---|
Silicone Mold Design | Holds shape, enables easy demolding, and withstands vacuum pressure and curing processes. |
Vacuum Pressure | Keeps mold tightly closed, eliminates air bubbles, and prevents shifting or deformation. |
Clamping Mechanism | Ensures even pressure and prevents material leakage during casting. |
Mold Alignment and Sealing | Prevents gaps or defects with precise alignment and silicone sealing. |
Curing Process | Maintains mold integrity for accurate part replication. |
Durability and Reusability | Allows molds to be reused multiple times without losing shape or integrity. |
Interested in vacuum casting for your projects? Contact our experts today to learn more!