The materials used for melting furnaces are primarily designed to withstand high temperatures, provide excellent thermal insulation, and ensure durability. Key materials include high-purity alumina fiber, lightweight alumina ceramic fiber, high-quality insulation boards, and Morgan materials brick. These materials are chosen for their ability to bear extreme heat, minimize heat loss, and reduce energy consumption. Additionally, the furnace body often incorporates stainless steel components for structural integrity and resistance to corrosion. Heating elements, such as iron-chrome aluminum or nickel chrome alloys, are also integral to the furnace's functionality, ensuring efficient heat generation and distribution.
Key Points Explained:
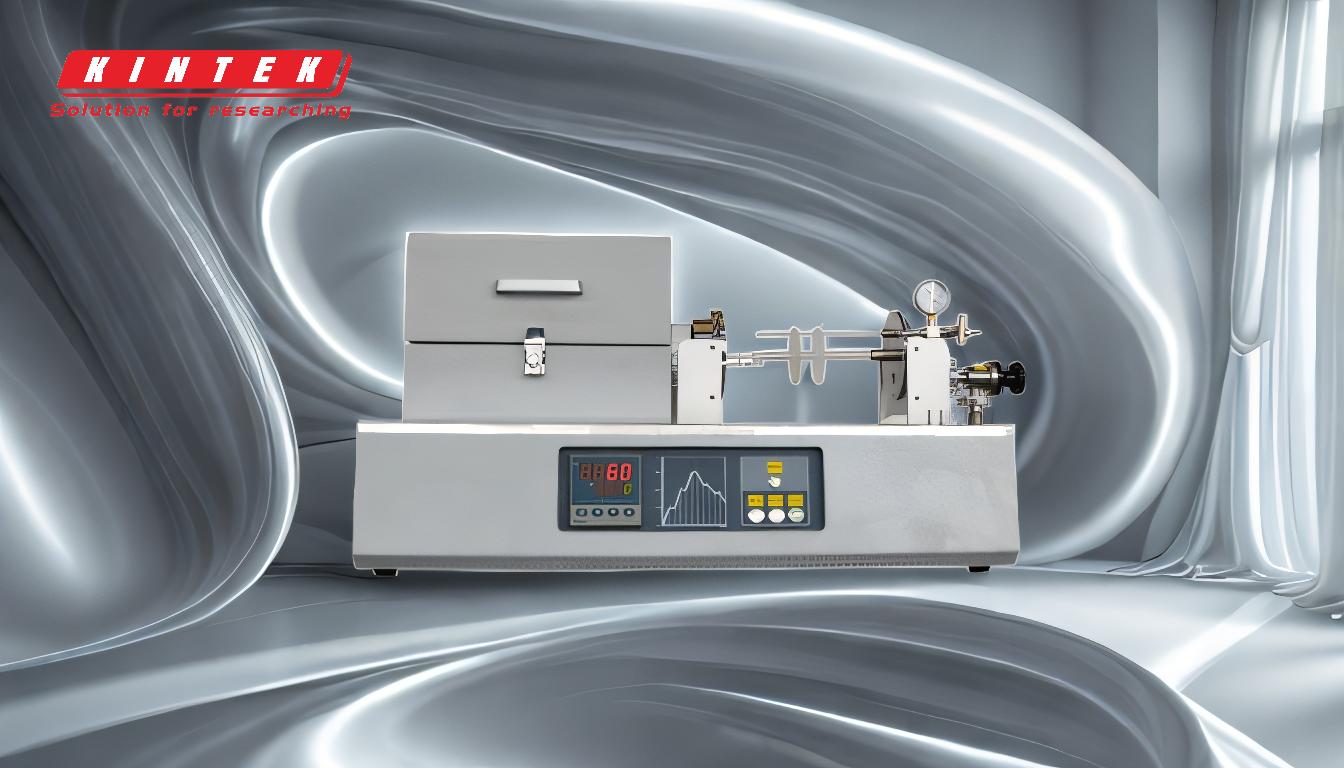
-
High-Purity Alumina Fiber:
- Description: High-purity alumina fiber is a common material used in the construction of melting furnaces. It is vacuum-formed to create a structure that can withstand high temperatures.
- Benefits: This material provides excellent heat preservation, reducing energy consumption and heat loss. It is also durable, making it suitable for high-temperature applications.
- Applications: Used in the insulation layers of the furnace to maintain high thermal efficiency.
-
Lightweight Alumina Ceramic Fiber:
- Description: Lightweight alumina ceramic fiber is another key material used in the multi-layer insulation design of melting furnaces.
- Benefits: It offers low heat loss and is free from asbestos, ensuring safety and environmental compliance. Its lightweight nature contributes to easier handling and installation.
- Applications: Often used in conjunction with high-quality insulation boards to enhance the furnace's thermal performance.
-
High-Quality Insulation Boards:
- Description: These boards are used as backing materials in the multi-layer insulation design of furnaces.
- Benefits: They provide additional thermal insulation, further reducing heat loss and improving energy efficiency.
- Applications: Positioned behind the alumina ceramic fiber layers to create a robust insulation barrier.
-
Morgan Materials Brick:
- Description: Morgan materials brick is a type of refractory brick used in the construction of sintering furnaces.
- Benefits: Known for its durability and efficiency in high-temperature environments, it contributes to the overall longevity and performance of the furnace.
- Applications: Used in the structural components of the furnace to withstand prolonged exposure to high temperatures.
-
Stainless Steel Components:
- Description: The furnace body often includes components made from 304 stainless steel, such as cylinders, inner and outer tubes, and flanges.
- Benefits: Stainless steel provides structural integrity, resistance to corrosion, and a polished outer surface that enhances the furnace's appearance.
- Applications: Used in the construction of the furnace shell, electrode holes, suction holes, vent holes, thermocouple holes, infrared holes, and observation holes.
-
Refractory Metals:
- Description: High-temperature furnaces may also incorporate refractory metals, which are dense, hard, and highly resistant to heat and wear.
- Benefits: These metals can endure extreme temperatures without degrading, ensuring the furnace's reliability and longevity.
- Applications: Used in critical areas of the furnace that are exposed to the highest temperatures.
-
Heating Elements:
- Description: Heating elements in industrial furnaces are typically made from iron-chrome aluminum or nickel chrome alloys.
- Benefits: These materials are excellent conductors of heat and can be shaped into various forms (cylindrical, semi-circular, or flat panels) to suit different furnace designs.
- Applications: Integral to the furnace's heating system, these elements generate and distribute heat efficiently throughout the furnace chamber.
By combining these materials, melting furnaces achieve a balance of high thermal efficiency, durability, and safety, making them suitable for a wide range of industrial applications.
Summary Table:
Material | Key Benefits | Applications |
---|---|---|
High-Purity Alumina Fiber | Excellent heat preservation, reduces energy consumption, durable | Insulation layers for high thermal efficiency |
Lightweight Alumina Fiber | Low heat loss, asbestos-free, lightweight | Multi-layer insulation design |
High-Quality Insulation Boards | Additional thermal insulation, reduces heat loss | Backing material in insulation layers |
Morgan Materials Brick | Durable, efficient in high-temperature environments | Structural components for prolonged high-temperature exposure |
Stainless Steel Components | Structural integrity, corrosion resistance, polished appearance | Furnace shell, electrode holes, vent holes, and more |
Refractory Metals | Resistant to extreme heat and wear, ensures reliability | Critical areas exposed to highest temperatures |
Heating Elements | Efficient heat generation and distribution, customizable shapes | Integral to the furnace's heating system |
Ready to optimize your melting furnace with the best materials? Contact our experts today for tailored solutions!