High-temperature furnaces are essential in various industries for processes requiring extreme heat, such as sintering, melting, and testing. The materials used in these furnaces are carefully selected based on their ability to withstand high temperatures, resist corrosion, and maintain structural integrity under thermal stress. Key materials include tungsten, molybdenum, alumina ceramic, quartz glass, graphite, and refractory metals like platinum and silicon carbide. These materials are chosen for their high melting points, thermal stability, and durability in harsh environments. The design and construction of high-temperature furnaces also involve robust base materials like stainless steel and copper for structural components, ensuring longevity and performance.
Key Points Explained:
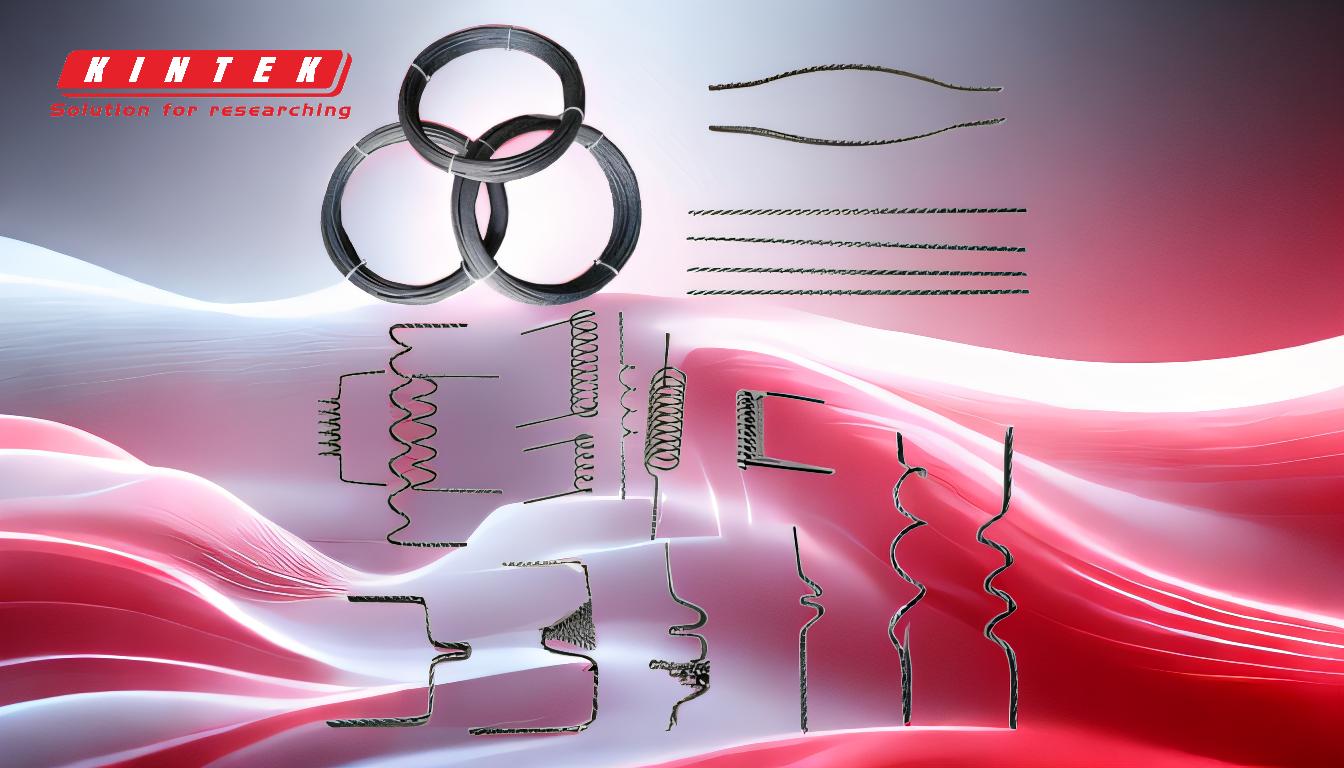
-
Tungsten and Molybdenum in Hot Zones:
- Tungsten and molybdenum are widely used in the hot zones of high temperature furnace due to their exceptionally high melting points (tungsten: 3,422°C, molybdenum: 2,623°C). These materials are ideal for vacuum furnaces, crystal growth furnaces, and sapphire growth furnaces, where extreme temperatures and vacuum environments are required. Their resistance to thermal degradation and ability to maintain structural integrity at high temperatures make them indispensable in these applications.
-
Alumina Ceramic and Quartz Glass in Furnace Chambers:
- The furnace chamber in high-temperature muffle furnaces is often constructed from alumina ceramic or quartz glass. Alumina ceramic is prized for its high-temperature resistance (up to 1,800°C) and excellent corrosion resistance, making it suitable for harsh chemical environments. Quartz glass, on the other hand, offers high transparency, allowing for real-time observation of experiments. Both materials are chosen for their ability to withstand thermal shock and maintain stability under high heat.
-
Refractory Materials in Vacuum Furnaces:
- High-temperature vacuum furnaces are typically lined with refractory materials such as graphite and ceramic. These materials can endure extreme temperatures and vacuum conditions without degrading. Graphite is particularly valued for its thermal conductivity and resistance to thermal shock, while ceramics provide excellent insulation and durability.
-
Heating Elements in High-Temperature Furnaces:
- Heating elements in high-temperature furnaces are often made from exotic materials like platinum, tungsten disilicide, molybdenum disilicide, and silicon carbide. These materials are selected for their ability to generate and withstand high temperatures while maintaining consistent performance. For instance, silicon carbide heating elements are known for their high thermal efficiency and long lifespan, even in oxidizing environments.
-
Structural Materials for Brazing Furnaces:
- Brazing furnaces, which operate at slightly lower temperatures compared to other high-temperature furnaces, are constructed from robust base materials such as brass, copper, stainless steel, and carbon steel. These materials provide the necessary strength and durability to support the furnace structure while withstanding the thermal and mechanical stresses of the brazing process.
-
Alumina Tubes in Tube Furnaces:
- Alumina tubes are essential components in tube furnaces, particularly for high-temperature operations. These tubes are designed to withstand extreme heat but are susceptible to thermal shock. Smaller-diameter alumina tubes generally perform better due to reduced thermal stress and improved heat distribution. They are commonly used in applications requiring precise temperature control and uniform heating.
-
Applications Across Industries:
- High-temperature furnaces are utilized in a wide range of industries, including aerospace, mining, battery manufacturing, metal 3D printing, dental, heat treatment, quality control laboratories, and powder metallurgy. Each industry has specific requirements for temperature, atmosphere, and material compatibility, which influence the choice of furnace materials and design.
By carefully selecting materials like tungsten, molybdenum, alumina ceramic, and refractory metals, manufacturers ensure that high-temperature furnaces can meet the demanding requirements of various industrial processes. These materials not only provide the necessary thermal and mechanical properties but also contribute to the overall efficiency and longevity of the furnace.
Summary Table:
Material | Key Properties | Applications |
---|---|---|
Tungsten | High melting point (3,422°C), thermal stability, vacuum compatibility | Vacuum furnaces, crystal growth, sapphire growth |
Molybdenum | High melting point (2,623°C), thermal resistance, structural integrity | Hot zones in high-temperature furnaces |
Alumina Ceramic | High-temperature resistance (up to 1,800°C), corrosion resistance | Furnace chambers, harsh chemical environments |
Quartz Glass | High transparency, thermal shock resistance | Real-time observation in furnace chambers |
Graphite | Thermal conductivity, resistance to thermal shock, vacuum compatibility | Lining in vacuum furnaces |
Platinum | High-temperature stability, consistent performance | Heating elements in high-temperature furnaces |
Silicon Carbide | High thermal efficiency, long lifespan, oxidation resistance | Heating elements in oxidizing environments |
Stainless Steel | Structural strength, durability, thermal stress resistance | Structural components in brazing furnaces |
Alumina Tubes | High-temperature resistance, precise heat distribution | Tube furnaces for uniform heating |
Need a high-temperature furnace tailored to your industry? Contact our experts today for a customized solution!