Brazing is a versatile joining process that allows for the bonding of a wide variety of metals and alloys. It is particularly useful for creating strong, leak-proof joints in complex assemblies. The process involves heating the base metals to a temperature above 450°C (842°F) but below their melting points, and then using a filler metal that melts and flows into the joint by capillary action. Furnace brazing, in particular, is a controlled process that ensures uniform heating and cooling, making it suitable for joining a diverse range of metals, including nickel-based alloys, stainless steels, carbon and alloy steels, as well as non-ferrous materials like aluminium, titanium, and copper.
Key Points Explained:
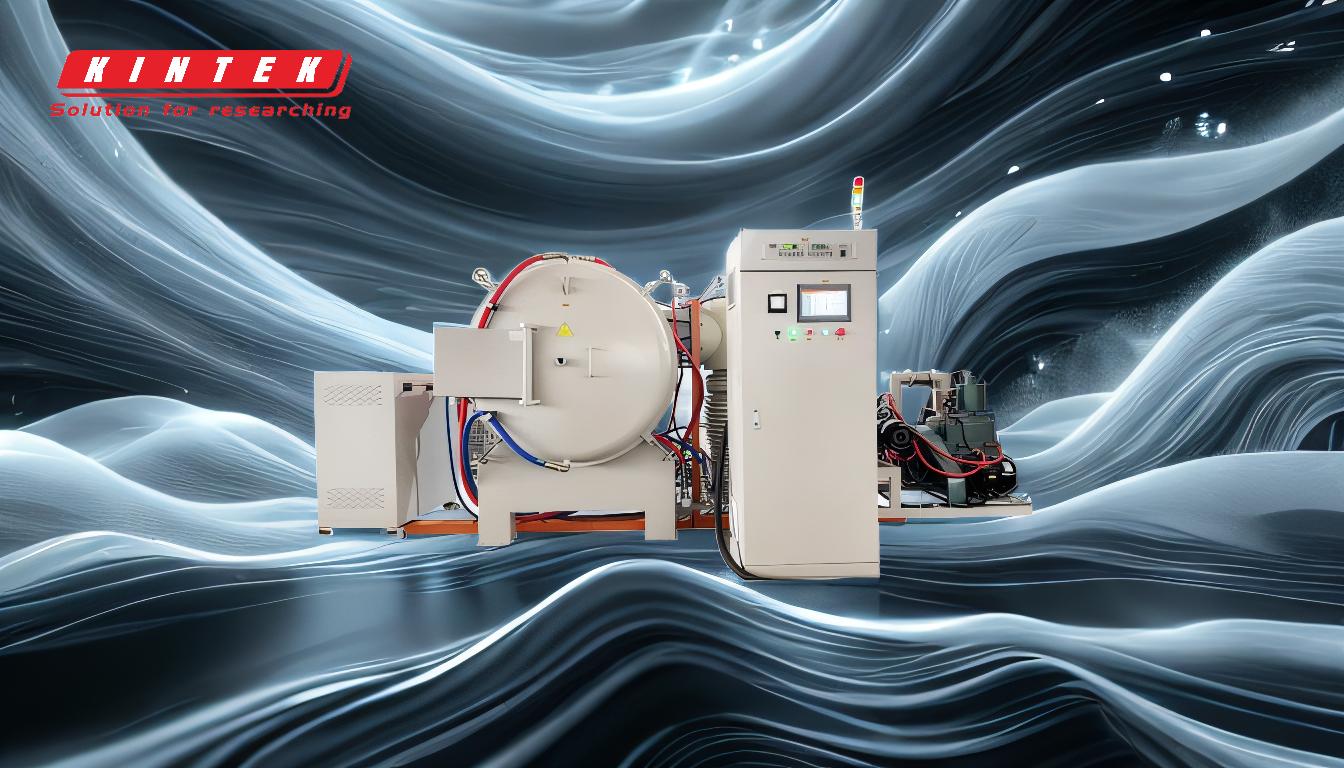
-
Nickel-Based Alloys:
- Nickel-based alloys are commonly used in high-temperature applications due to their excellent resistance to oxidation and corrosion. These alloys can be effectively brazed using specialized filler metals that match their thermal and mechanical properties. The brazing process must be carefully controlled to avoid compromising the alloy's inherent strengths.
-
Stainless Steels:
- Stainless steels, known for their corrosion resistance, can also be brazed. The key challenge is to prevent the formation of chromium carbides, which can reduce corrosion resistance. This is typically managed by using low-temperature brazing alloys and controlling the cooling rate to minimize carbide precipitation.
-
Carbon and Alloy Steels:
- Carbon and alloy steels are widely used in various industries due to their strength and durability. These materials can be brazed using filler metals that have a lower melting point than the base metal. The brazing process enhances the joint strength without significantly altering the base metal's properties.
-
Non-Ferrous Materials:
- Aluminium: Aluminium and its alloys are lightweight and have excellent thermal and electrical conductivity. Brazing aluminium requires careful selection of filler metals and fluxes to ensure proper wetting and bonding. The process must be conducted in a controlled atmosphere to prevent oxidation.
- Titanium: Titanium is known for its high strength-to-weight ratio and resistance to corrosion. Brazing titanium is challenging due to its reactivity with oxygen and nitrogen at high temperatures. Specialized filler metals and controlled atmospheres are essential for successful brazing.
- Copper: Copper and its alloys are widely used in electrical and thermal applications due to their excellent conductivity. Brazing copper is relatively straightforward, with a variety of filler metals available that provide strong, durable joints.
-
Furnace Brazing Advantages:
- Furnace brazing offers several advantages, including uniform heating and cooling, which minimizes thermal stress and distortion. The controlled atmosphere in the furnace prevents oxidation and contamination, ensuring high-quality joints. This method is particularly suitable for complex assemblies and high-volume production.
-
Filler Metal Selection:
- The choice of filler metal is critical in brazing. It must have a melting point below that of the base metals but should also provide the necessary strength, corrosion resistance, and thermal properties for the intended application. Common filler metals include silver-based alloys, copper-based alloys, and nickel-based alloys.
-
Joint Design and Preparation:
- Proper joint design and surface preparation are essential for successful brazing. The joint must be designed to allow capillary action to draw the filler metal into the gap. Surface preparation involves cleaning to remove oxides, oils, and other contaminants that could impede the flow of the filler metal.
-
Post-Brazing Treatment:
- After brazing, it may be necessary to perform post-brazing treatments such as heat treatment or surface finishing to enhance the joint's properties and appearance. These treatments can improve corrosion resistance, mechanical strength, and overall durability.
In summary, brazing is a highly effective method for joining a wide range of metals, including nickel-based alloys, stainless steels, carbon and alloy steels, and non-ferrous materials like aluminium, titanium, and copper. The process requires careful selection of filler metals, proper joint design, and controlled heating and cooling to ensure strong, durable, and high-quality joints. Furnace brazing, in particular, offers significant advantages in terms of uniformity and control, making it suitable for a variety of industrial applications.
Summary Table:
Metal Type | Key Characteristics | Brazing Considerations |
---|---|---|
Nickel-Based Alloys | High-temperature resistance, oxidation, and corrosion resistance. | Use specialized filler metals; control brazing process to preserve alloy properties. |
Stainless Steels | Excellent corrosion resistance. | Prevent chromium carbide formation with low-temperature alloys and controlled cooling. |
Carbon & Alloy Steels | High strength and durability. | Use filler metals with lower melting points; maintain base metal properties. |
Aluminium | Lightweight, excellent thermal and electrical conductivity. | Requires controlled atmosphere and proper flux to prevent oxidation. |
Titanium | High strength-to-weight ratio, corrosion resistance. | Use specialized filler metals and controlled atmospheres due to high reactivity. |
Copper | Excellent electrical and thermal conductivity. | Straightforward brazing process with a variety of filler metals. |
Need expert advice on brazing metals for your project? Contact us today to get started!