The synthesis of carbon nanotubes (CNTs) using the Chemical Vapor Deposition (CVD) method involves the use of specific precursors that decompose and react to form carbon nanotubes. The CVD process is a versatile technique that allows for the controlled growth of CNTs by adjusting parameters such as temperature, pressure, and gas flow rates. The key to successful CNT synthesis lies in the choice of precursor, which typically includes hydrocarbons like methane, ethylene, or acetylene, along with a catalyst such as iron, cobalt, or nickel. These precursors decompose at high temperatures, releasing carbon atoms that then assemble into the cylindrical structures of CNTs. The CVD method is favored for its ability to produce high-quality CNTs with controlled properties, making it a popular choice in both research and industrial applications.
Key Points Explained:
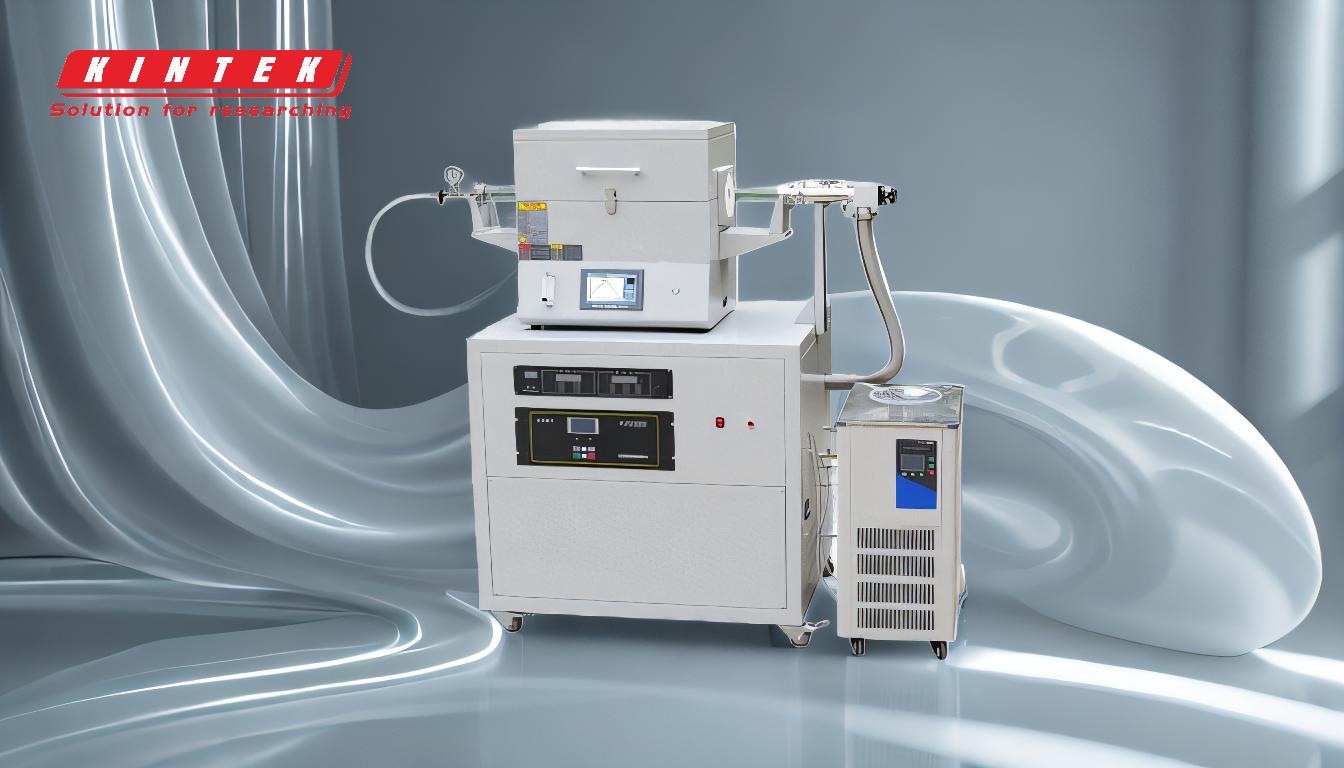
-
Precursor Selection in CVD for CNT Synthesis:
- The choice of precursor is critical in the CVD process for CNT synthesis. Common precursors include hydrocarbons such as methane (CH₄), ethylene (C₂H₄), and acetylene (C₂H₂). These gases are chosen because they can decompose at high temperatures to release carbon atoms, which are essential for the formation of CNTs.
- The decomposition of these hydrocarbons typically occurs at temperatures ranging from 600°C to 1200°C, depending on the specific precursor and the desired properties of the CNTs.
-
Role of Catalysts:
- Catalysts play a crucial role in the CVD process by lowering the activation energy required for the decomposition of the precursor and facilitating the growth of CNTs. Common catalysts include transition metals such as iron (Fe), cobalt (Co), and nickel (Ni).
- The catalyst is often deposited on a substrate in the form of nanoparticles, which serve as nucleation sites for the growth of CNTs. The size and distribution of these nanoparticles can significantly influence the diameter and quality of the resulting CNTs.
-
Decomposition and Growth Mechanism:
- During the CVD process, the hydrocarbon precursor decomposes on the surface of the catalyst nanoparticles, releasing carbon atoms. These carbon atoms then dissolve into the catalyst and precipitate out to form the cylindrical structure of the CNTs.
- The growth mechanism can be either tip-growth or base-growth, depending on the interaction between the catalyst and the substrate. In tip-growth, the catalyst remains at the tip of the growing CNT, while in base-growth, the catalyst stays at the base.
-
Influence of Process Parameters:
- The quality and properties of the CNTs are highly dependent on the process parameters, including temperature, pressure, gas flow rate, and the concentration of the precursor.
- Higher temperatures generally lead to faster decomposition of the precursor and faster growth of CNTs, but excessive temperatures can also lead to defects or unwanted by-products.
- The pressure and gas flow rate affect the uniformity and density of the CNTs. Optimal conditions must be carefully controlled to achieve the desired CNT characteristics.
-
Advantages of CVD for CNT Synthesis:
- The CVD method offers several advantages, including the ability to produce high-purity CNTs with controlled diameters and lengths. It is also a scalable process, making it suitable for industrial applications.
- The method allows for the synthesis of both single-walled carbon nanotubes (SWCNTs) and multi-walled carbon nanotubes (MWCNTs) by adjusting the process conditions and the type of catalyst used.
-
Applications of CNTs Synthesized by CVD:
- CNTs produced by the CVD method have a wide range of applications, including in electronics, composites, energy storage, and biomedical devices. Their unique properties, such as high electrical conductivity, mechanical strength, and thermal stability, make them highly desirable for these applications.
In summary, the CVD method for CNT synthesis relies on the careful selection of precursors, catalysts, and process parameters to achieve high-quality CNTs with controlled properties. The method's versatility and scalability make it a preferred choice for both research and industrial applications.
Summary Table:
Precursor | Decomposition Temperature | Role in CNT Synthesis |
---|---|---|
Methane (CH₄) | 600°C - 1200°C | Releases carbon atoms for CNT formation |
Ethylene (C₂H₄) | 600°C - 1200°C | Provides carbon source for controlled growth |
Acetylene (C₂H₂) | 600°C - 1200°C | High reactivity for efficient CNT synthesis |
Need help optimizing your CNT synthesis process? Contact our experts today for tailored solutions!