Sputter coating is a thin film deposition process that occurs under low-pressure conditions, typically in a vacuum chamber. The process involves the use of a plasma generated by ionizing a gas, usually argon, at pressures ranging from 1 to 15 millitorr (mTorr). This low-pressure environment is crucial as it allows the argon ions to accelerate and collide with the target material, causing atoms to be ejected and deposited onto a substrate. The pressure is carefully controlled to ensure efficient ionization and uniform coating. Techniques like magnetron sputtering, RF sputtering, and DC sputtering are commonly used, each requiring specific pressure conditions to optimize the deposition process. Sputter coating is widely used in applications such as semiconductor manufacturing, optical coatings, and electron microscopy sample preparation.
Key Points Explained:
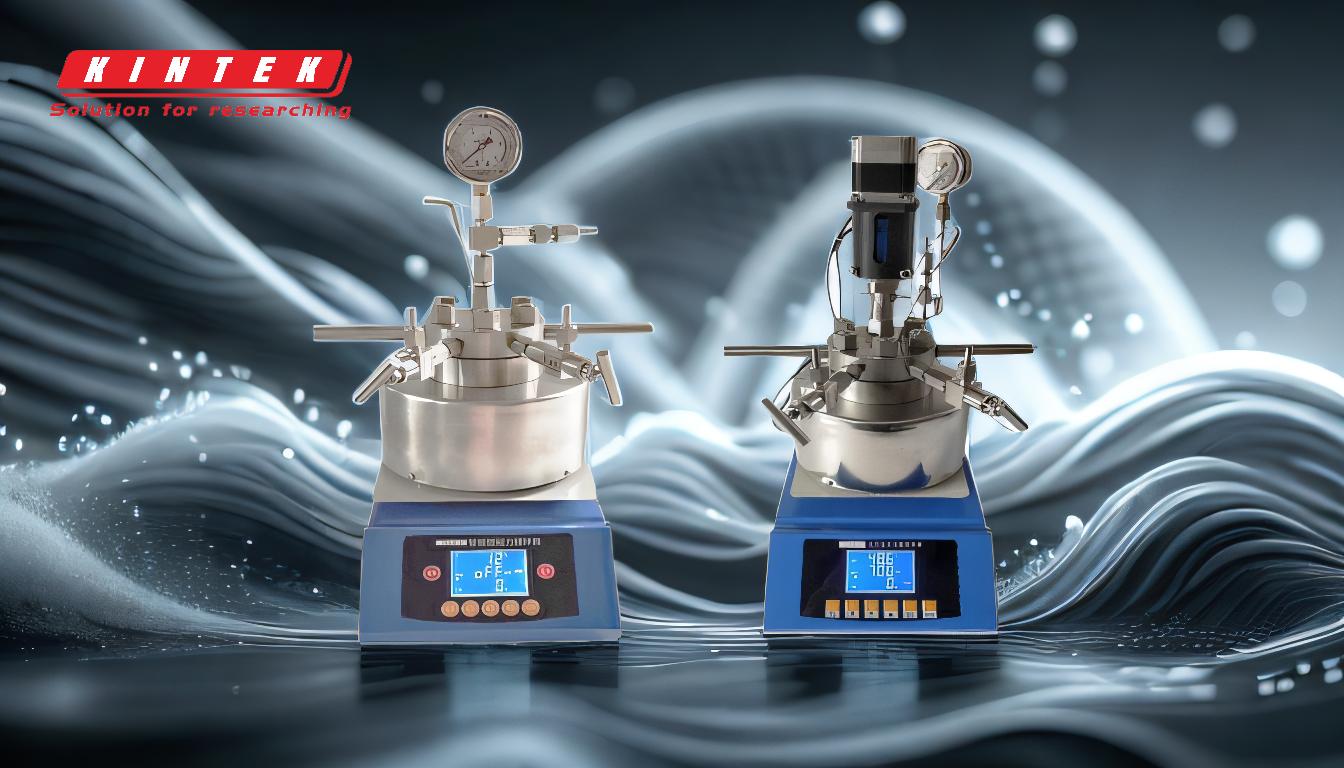
-
Low-Pressure Environment:
- Sputter coating occurs in a vacuum chamber where the pressure is maintained between 1 to 15 mTorr. This low-pressure environment is essential for the ionization of argon gas and the acceleration of ions toward the target material.
- The vacuum ensures minimal interference from other gases, allowing for precise control over the deposition process.
-
Ionization and Plasma Formation:
- A small amount of argon gas is introduced into the vacuum chamber. When voltage (DC, RF, or median frequency) is applied, the argon gas is ionized, forming a plasma.
- The plasma consists of free electrons and positively charged argon ions, which are accelerated toward the negatively charged target material.
-
Target Material Erosion:
- The accelerated argon ions collide with the target material, causing atoms to be ejected from the surface in a process known as sputtering.
- The sputtered atoms are ejected into the gas phase and travel toward the substrate, where they deposit and form a thin film.
-
Uniform Coating Formation:
- The sputtered atoms deposit on all surfaces within the vacuum chamber, including the substrate. This omni-directional deposition results in a uniform and even coating.
- The uniformity of the coating is critical for applications such as electron microscopy, where consistent thickness is required to prevent charging and improve image quality.
-
Applications of Sputter Coating:
- Semiconductor Manufacturing: Sputter coating is used to deposit thin films of metals and dielectrics on silicon wafers.
- Optical Coatings: Anti-reflective and high-emissivity films are applied to glass and other optical components.
- Electron Microscopy: Sputter coating is used to prepare samples by applying a conductive layer, such as gold, to prevent charging and enhance secondary electron emission.
-
Techniques and Variations:
- Magnetron Sputtering: Uses magnetic fields to confine the plasma near the target, increasing the efficiency of the sputtering process.
- RF Sputtering: Utilizes radio frequency power to ionize the gas, suitable for insulating target materials.
- DC Sputtering: Employs direct current power, commonly used for conductive target materials.
-
Pressure Control:
- The pressure in the vacuum chamber is carefully controlled to optimize the sputtering process. Too high a pressure can lead to collisions between gas molecules, reducing the energy of the ions. Too low a pressure may result in insufficient ionization and poor deposition rates.
-
Benefits of Sputter Coating:
- Precision: Allows for the deposition of thin films with precise thickness and composition.
- Uniformity: Ensures even coating across complex geometries and large areas.
- Versatility: Suitable for a wide range of materials, including metals, alloys, and ceramics.
By maintaining the appropriate pressure and utilizing advanced sputtering techniques, sputter coating provides a reliable and efficient method for depositing high-quality thin films in various industrial and scientific applications.
Summary Table:
Key Aspect | Details |
---|---|
Pressure Range | 1 to 15 mTorr |
Purpose of Low Pressure | Ensures efficient ionization and uniform coating |
Common Techniques | Magnetron, RF, and DC sputtering |
Applications | Semiconductor manufacturing, optical coatings, electron microscopy |
Benefits | Precision, uniformity, and versatility in thin film deposition |
Discover how sputter coating can enhance your process—contact our experts today for tailored solutions!