Press forging is a manufacturing process used to shape metal into desired forms by applying compressive forces. This method is widely used in various industries due to its ability to produce high-strength, durable, and precise components. The process involves placing a heated metal workpiece between two dies and applying pressure to shape it. Products made from press forging include automotive parts, aerospace components, industrial machinery parts, and tools. The process is favored for its ability to produce complex shapes with excellent mechanical properties, making it ideal for applications requiring high performance and reliability.
Key Points Explained:
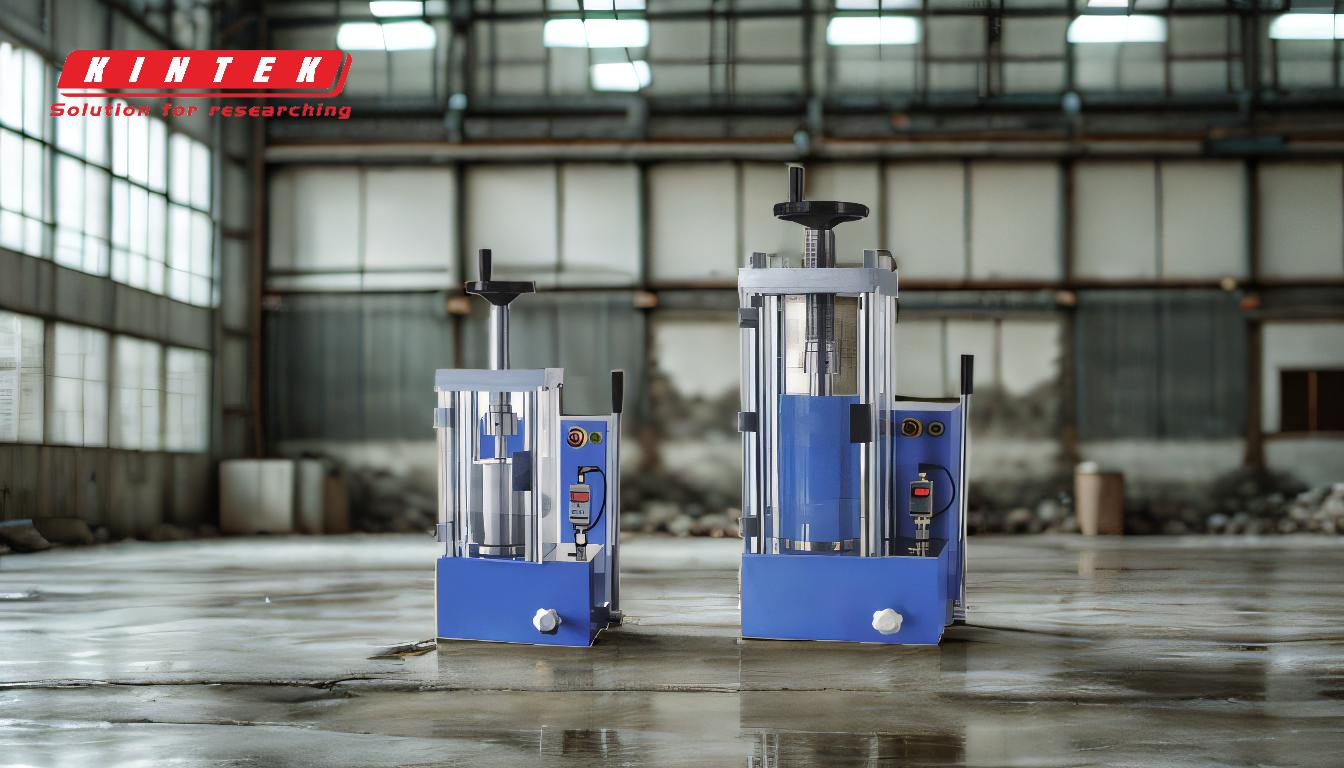
-
Automotive Parts:
- Engine Components: Press forging is used to manufacture critical engine parts such as crankshafts, connecting rods, and camshafts. These components require high strength and durability to withstand the stresses of engine operation.
- Transmission Parts: Gears, shafts, and other transmission components are often produced using press forging. The process ensures precise dimensions and high fatigue resistance, essential for smooth and reliable transmission operation.
- Suspension and Steering Components: Parts like control arms, steering knuckles, and ball joints are commonly made through press forging. These components need to endure significant loads and impacts, making the strength and reliability of forged parts crucial.
-
Aerospace Components:
- Structural Parts: Press forging is used to create structural components such as landing gear parts, wing spars, and fuselage frames. These parts must meet stringent aerospace standards for strength, weight, and durability.
- Engine Parts: Turbine blades, compressor disks, and other engine components are often forged using this method. The high-temperature and high-stress environment of aerospace engines requires materials with exceptional mechanical properties, which press forging provides.
-
Industrial Machinery Parts:
- Heavy Equipment Components: Parts for construction and mining equipment, such as bulldozer blades, excavator arms, and hydraulic cylinders, are commonly produced using press forging. These components need to withstand extreme conditions and heavy loads.
- Pump and Valve Parts: Forged components are used in pumps and valves to ensure they can handle high pressures and corrosive environments. The precision and strength of forged parts are critical for the reliable operation of these systems.
-
Tools and Hardware:
- Hand Tools: Wrenches, pliers, hammers, and other hand tools are often made through press forging. The process provides the necessary strength and durability for these tools to perform effectively under heavy use.
- Industrial Tools: Cutting tools, dies, and molds used in manufacturing processes are frequently forged to achieve the required hardness and wear resistance.
-
Advantages of Press Forging:
- High Strength and Durability: The compressive forces applied during press forging align the grain structure of the metal, resulting in components with superior mechanical properties.
- Precision and Consistency: The use of dies ensures that each forged part is produced with high dimensional accuracy and consistency, reducing the need for additional machining.
- Complex Shapes: Press forging can produce intricate shapes that would be difficult or impossible to achieve with other manufacturing methods.
- Material Efficiency: The process minimizes material waste, as the metal is shaped directly into the desired form without significant removal of material.
In summary, press forging is a versatile and efficient manufacturing process used to produce a wide range of high-performance components across various industries. Its ability to create strong, durable, and precise parts makes it an essential technique in modern manufacturing.
Summary Table:
Category | Examples |
---|---|
Automotive Parts | Engine components (crankshafts, connecting rods), transmission parts, suspension and steering components |
Aerospace Components | Structural parts (landing gear, wing spars), engine parts (turbine blades, compressor disks) |
Industrial Machinery | Heavy equipment components (bulldozer blades, excavator arms), pump and valve parts |
Tools and Hardware | Hand tools (wrenches, pliers), industrial tools (cutting tools, dies, molds) |
Advantages | High strength, precision, complex shapes, material efficiency |
Need high-strength forged components for your industry? Contact us today to learn more about press forging solutions!