Surface hardening is a process used to increase the hardness of the outer surface of a metal while maintaining a softer, more ductile core. This technique is essential for improving wear resistance, fatigue strength, and overall durability of components. Various methods and products are employed for surface hardening, including heat treatment, chemical treatments, and mechanical processes. The choice of method depends on the material, application, and desired properties.
Key Points Explained:
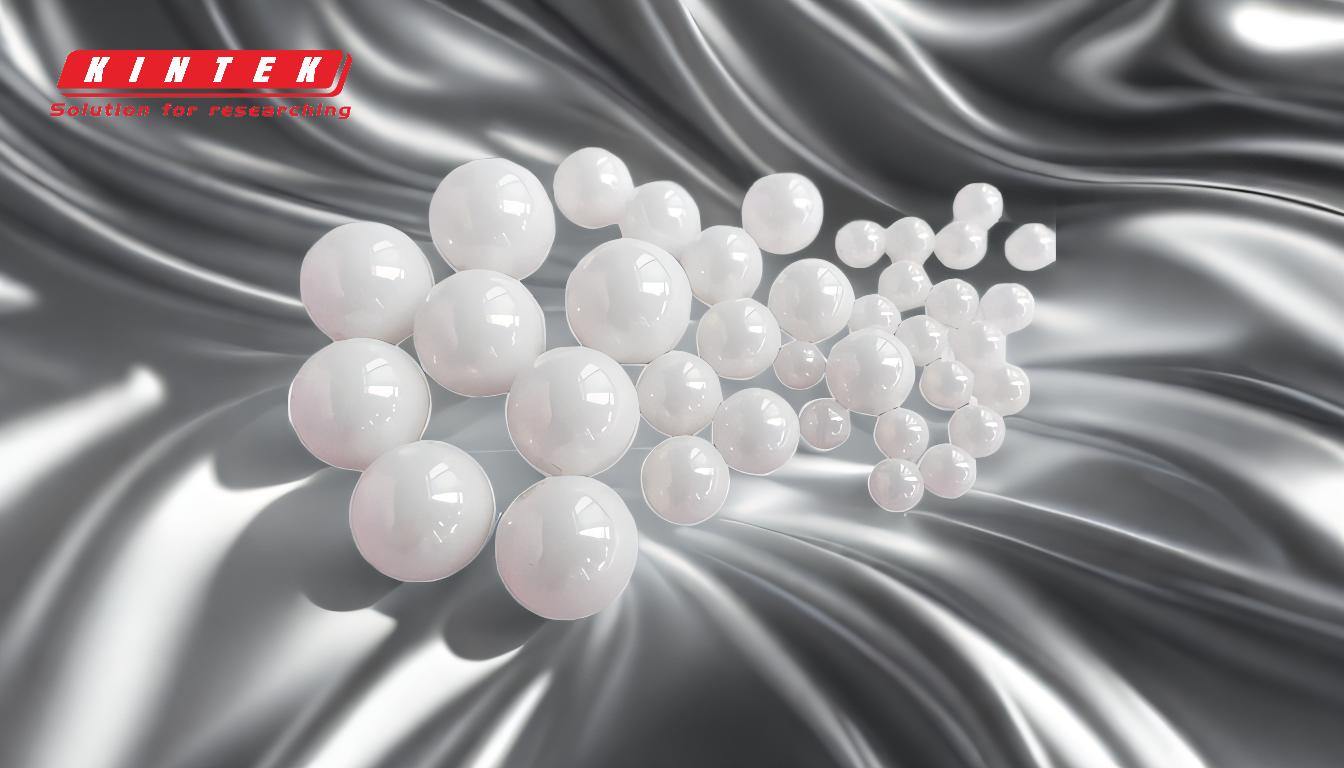
-
Heat Treatment Methods:
- Induction Hardening: This method uses electromagnetic induction to heat the surface of the metal, followed by rapid quenching. It is commonly used for gears, shafts, and other components that require high surface hardness.
- Flame Hardening: This involves heating the metal surface with an oxy-acetylene flame and then quenching it. It is suitable for large components and irregular shapes.
- Laser Hardening: A focused laser beam is used to heat the surface, followed by self-quenching due to the rapid heat dissipation into the bulk material. This method offers precision and minimal distortion.
-
Chemical Treatment Methods:
- Carburizing: This process involves introducing carbon into the surface layer of low-carbon steel by heating it in a carbon-rich environment. The carbon diffuses into the surface, increasing hardness after quenching.
- Nitriding: This method introduces nitrogen into the surface of the metal, forming hard nitrides. It is performed at lower temperatures, reducing distortion and making it suitable for finished components.
- Cyaniding: A process where the metal is heated in a molten cyanide bath, allowing carbon and nitrogen to diffuse into the surface. It is less commonly used due to environmental concerns.
-
Mechanical Methods:
- Shot Peening: This involves bombarding the surface with small spherical media (shots) to induce compressive stresses, which improve fatigue resistance and surface hardness.
- Roller Burnishing: A cold-working process where a hardened roller is pressed against the surface to smooth and harden it. It is often used for improving the surface finish and hardness of cylindrical components.
-
Products and Materials:
- Steels: Various grades of steel, such as low-carbon steels, alloy steels, and tool steels, are commonly surface hardened using the above methods.
- Cast Irons: Certain types of cast iron, like ductile iron, can also be surface hardened to improve wear resistance.
- Non-Ferrous Alloys: Some non-ferrous alloys, such as titanium and aluminum, can undergo surface hardening processes like nitriding or anodizing to enhance surface properties.
-
Applications:
- Automotive Industry: Components like gears, crankshafts, and camshafts often undergo surface hardening to withstand high stress and wear.
- Aerospace Industry: Critical parts such as landing gear and turbine blades are surface hardened to ensure durability and safety.
- Tooling and Machinery: Cutting tools, dies, and molds are surface hardened to extend their service life and maintain precision.
-
Advantages of Surface Hardening:
- Enhanced Wear Resistance: The hardened surface resists abrasion and wear, extending the life of the component.
- Improved Fatigue Strength: Surface hardening introduces compressive stresses that improve resistance to fatigue failure.
- Ductile Core: The softer core maintains toughness and ductility, preventing brittle fracture.
-
Considerations for Selection:
- Material Compatibility: Not all materials are suitable for every surface hardening method. The choice depends on the base material and its properties.
- Component Geometry: The shape and size of the component influence the choice of hardening method. Complex geometries may require more precise methods like laser hardening.
- Cost and Efficiency: Some methods, like induction hardening, are cost-effective for high-volume production, while others, like laser hardening, may be more expensive but offer greater precision.
In conclusion, surface hardening encompasses a variety of methods and products tailored to enhance the surface properties of metals. The selection of the appropriate method depends on the material, application, and desired outcomes, ensuring that components can withstand the demands of their operational environment.
Summary Table:
Category | Methods/Examples |
---|---|
Heat Treatment | Induction Hardening, Flame Hardening, Laser Hardening |
Chemical Treatment | Carburizing, Nitriding, Cyaniding |
Mechanical Methods | Shot Peening, Roller Burnishing |
Materials | Steels, Cast Irons, Non-Ferrous Alloys |
Applications | Automotive, Aerospace, Tooling & Machinery |
Advantages | Enhanced Wear Resistance, Improved Fatigue Strength, Ductile Core |
Selection Factors | Material Compatibility, Component Geometry, Cost & Efficiency |
Discover the best surface hardening solution for your needs—contact our experts today!