Sintering is a manufacturing process that involves compacting and forming a solid mass of material using heat or pressure without melting it to the point of liquefaction. This process significantly influences the microstructure of materials, affecting properties such as grain size, pore size, and grain boundary distribution. These microstructural changes directly impact the material's mechanical properties, including strength, durability, and thermal stability. Sintering is versatile and applicable to a wide range of materials, including ceramics, metals, polymers, and composites, making it suitable for diverse applications like rapid prototyping, high-temperature components, and additive manufacturing.
Key Points Explained:
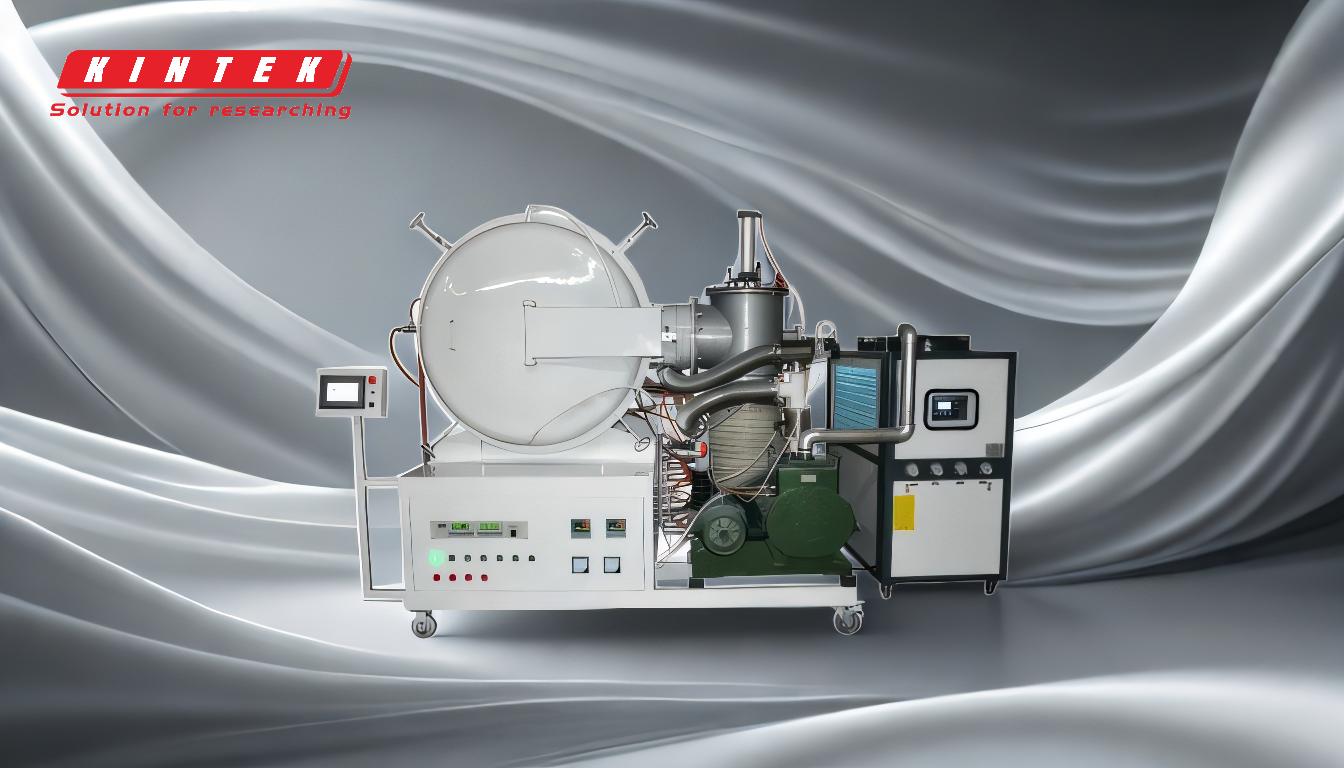
-
Microstructural Changes During Sintering:
- Grain Size: Sintering alters the size of grains within the material. Smaller grains generally enhance strength and hardness due to the Hall-Petch relationship, which states that smaller grains increase the material's resistance to deformation.
- Pore Size: The process reduces pore size and porosity, leading to denser materials. Lower porosity improves mechanical properties like tensile strength and wear resistance.
- Grain Boundary Shape and Distribution: Sintering affects the shape and distribution of grain boundaries, which are critical for controlling crack propagation and material toughness.
-
Impact on Material Properties:
- Strength: Sintered materials often exhibit higher strength due to reduced porosity and refined grain structure. This is particularly important in applications requiring high load-bearing capacity.
- Durability: Enhanced grain boundary distribution and reduced porosity contribute to improved fatigue resistance and longevity, especially in high-stress environments.
- Thermal Stability: Sintered ceramics and metals maintain structural integrity at high temperatures, making them ideal for applications like aerospace components and industrial furnaces.
-
Materials Suitable for Sintering:
- Ceramics: Commonly used for high-temperature applications due to their thermal stability and resistance to wear and corrosion.
- Metals: Includes stainless steel, aluminum, nickel, copper, titanium alloys, and specialized steels like iron-copper and iron-nickel steels. These materials are processed to enhance properties such as strength, conductivity, and corrosion resistance.
- Polymers: Used in rapid prototyping and filter manufacturing, where sintering provides precise control over material properties and geometry.
- Composites: Sintering allows for the combination of different materials to achieve tailored properties, such as improved strength-to-weight ratios or enhanced thermal conductivity.
-
Applications of Sintered Materials:
- High-Temperature Components: Sintered ceramics and metals are used in gears, bearings, and turbine blades, where thermal stability and wear resistance are critical.
- Small Components: Metal sintering is ideal for producing small, complex parts like gears and pulleys with high precision and strength.
- Additive Manufacturing: Advanced sintering technologies enable the production of intricate components using metal powders, making it a key process in 3D printing and powder metallurgy.
-
Advantages of Sintering:
- Versatility: Suitable for a wide range of materials and applications, from industrial components to consumer products.
- Cost-Effectiveness: Reduces material waste and energy consumption compared to traditional melting processes.
- Customization: Allows for precise control over material properties, enabling the production of components with tailored characteristics.
In summary, sintering is a critical process that transforms raw materials into high-performance components by refining their microstructure and enhancing their mechanical and thermal properties. Its versatility and ability to work with diverse materials make it indispensable in modern manufacturing and engineering.
Summary Table:
Aspect | Details |
---|---|
Microstructural Changes | - Grain size refinement increases strength and hardness. |
- Reduced pore size improves tensile strength and wear resistance. | |
- Enhanced grain boundary distribution boosts toughness. | |
Impact on Properties | - Higher strength and durability. |
- Improved thermal stability for high-temperature applications. | |
Materials | Ceramics, metals (e.g., stainless steel, titanium), polymers, composites. |
Applications | High-temperature components, small parts, additive manufacturing. |
Advantages | Versatility, cost-effectiveness, and customization. |
Learn how sintering can optimize your manufacturing process—contact our experts today!