Porcelain is fired at high temperatures to achieve its characteristic strength, durability, and translucency. The firing temperature typically ranges between 1200°C (2192°F) and 1400°C (2552°F), depending on the type of porcelain and the desired properties. The process involves multiple stages, including bisque firing and glaze firing, each requiring precise temperature control. A porcelain furnace is essential for this process, as it ensures even heating and cooling, which are critical for preventing defects like cracking or warping. Understanding the firing process and temperature requirements is crucial for achieving high-quality porcelain products.
Key Points Explained:
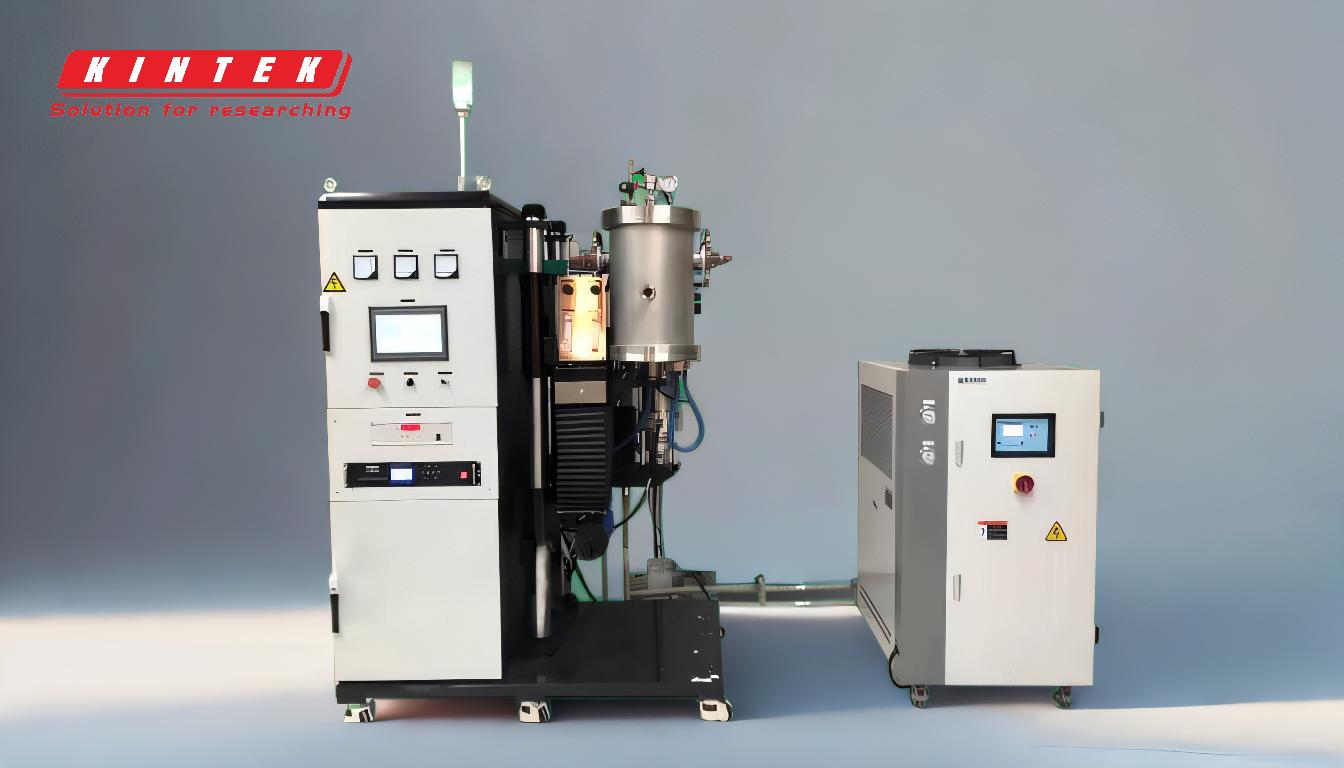
-
Firing Temperature Range for Porcelain:
- Porcelain is fired at temperatures between 1200°C (2192°F) and 1400°C (2552°F). This high-temperature firing is necessary to vitrify the clay, making it non-porous and strong.
- The exact temperature depends on the type of porcelain (e.g., hard-paste or soft-paste) and the specific application (e.g., tableware, decorative items, or industrial components).
-
Stages of Firing:
- Bisque Firing: This is the first firing stage, typically done at 900°C to 1000°C (1652°F to 1832°F). It removes all moisture and organic materials from the clay, making it hard and porous enough to absorb glaze.
- Glaze Firing: The second stage occurs at the higher temperature range of 1200°C to 1400°C (2192°F to 2552°F). This stage melts the glaze, fusing it to the porcelain body and creating a smooth, glass-like surface.
-
Role of the Porcelain Furnace:
- A porcelain furnace is specifically designed to handle the high temperatures and precise control required for firing porcelain. It ensures uniform heating and cooling, which are critical to prevent defects such as cracking, warping, or uneven glaze application.
- Modern porcelain furnaces often feature programmable settings, allowing users to customize firing schedules for different types of porcelain and glazes.
-
Factors Influencing Firing Temperature:
- Clay Composition: The type and purity of the clay used in porcelain affect the firing temperature. For example, kaolin clay, a primary component of porcelain, requires high temperatures to vitrify.
- Glaze Compatibility: The glaze must be formulated to melt at the same temperature as the porcelain body to ensure proper adhesion and finish.
- Desired Properties: Higher firing temperatures generally result in stronger and more durable porcelain, but they also increase the risk of defects if not carefully controlled.
-
Importance of Temperature Control:
- Precise temperature control is essential throughout the firing process. Rapid heating or cooling can cause thermal shock, leading to cracks or breaks in the porcelain.
- A porcelain furnace with advanced temperature regulation capabilities is crucial for achieving consistent results.
-
Applications of High-Temperature Fired Porcelain:
- Porcelain fired at high temperatures is used in a wide range of applications, including:
- Tableware: High durability and resistance to staining make it ideal for dishes and cups.
- Decorative Items: Its smooth, glass-like finish is perfect for art pieces and ornaments.
- Industrial Components: High-strength porcelain is used in electrical insulators, laboratory equipment, and other specialized applications.
- Porcelain fired at high temperatures is used in a wide range of applications, including:
-
Challenges in High-Temperature Firing:
- Energy Consumption: Firing porcelain at high temperatures requires significant energy, making it a costly process.
- Material Shrinkage: Porcelain shrinks during firing, which must be accounted for during the design and molding stages.
- Defect Prevention: Proper firing techniques and equipment are essential to minimize defects like warping, cracking, or glaze imperfections.
By understanding the firing process and the role of a porcelain furnace, manufacturers and artists can produce high-quality porcelain products that meet specific functional and aesthetic requirements.
Summary Table:
Aspect | Details |
---|---|
Firing Temperature | 1200°C to 1400°C (2192°F to 2552°F) |
Bisque Firing | 900°C to 1000°C (1652°F to 1832°F) |
Glaze Firing | 1200°C to 1400°C (2192°F to 2552°F) |
Key Factors | Clay composition, glaze compatibility, desired properties |
Applications | Tableware, decorative items, industrial components |
Challenges | Energy consumption, material shrinkage, defect prevention |
Ready to achieve flawless porcelain results? Contact our experts today to find the perfect porcelain furnace for your needs!