Furnace brazing is a process that involves joining metal parts using a filler metal that melts at a temperature above 450°C (842°F) but below the melting point of the base metals. The specific temperature for furnace brazing depends on several factors, including the type of base metals, the braze alloy used, and the desired joint properties. Generally, the brazing temperature should be the lowest possible within the recommended range, typically at least 25°C (50°F) above the liquidus temperature of the braze alloy. This ensures proper flow and bonding without damaging the base materials. Laboratory muffle furnaces, often used for brazing, typically operate within a range of 1100°C to 1200°C, which is suitable for many brazing applications.
Key Points Explained:
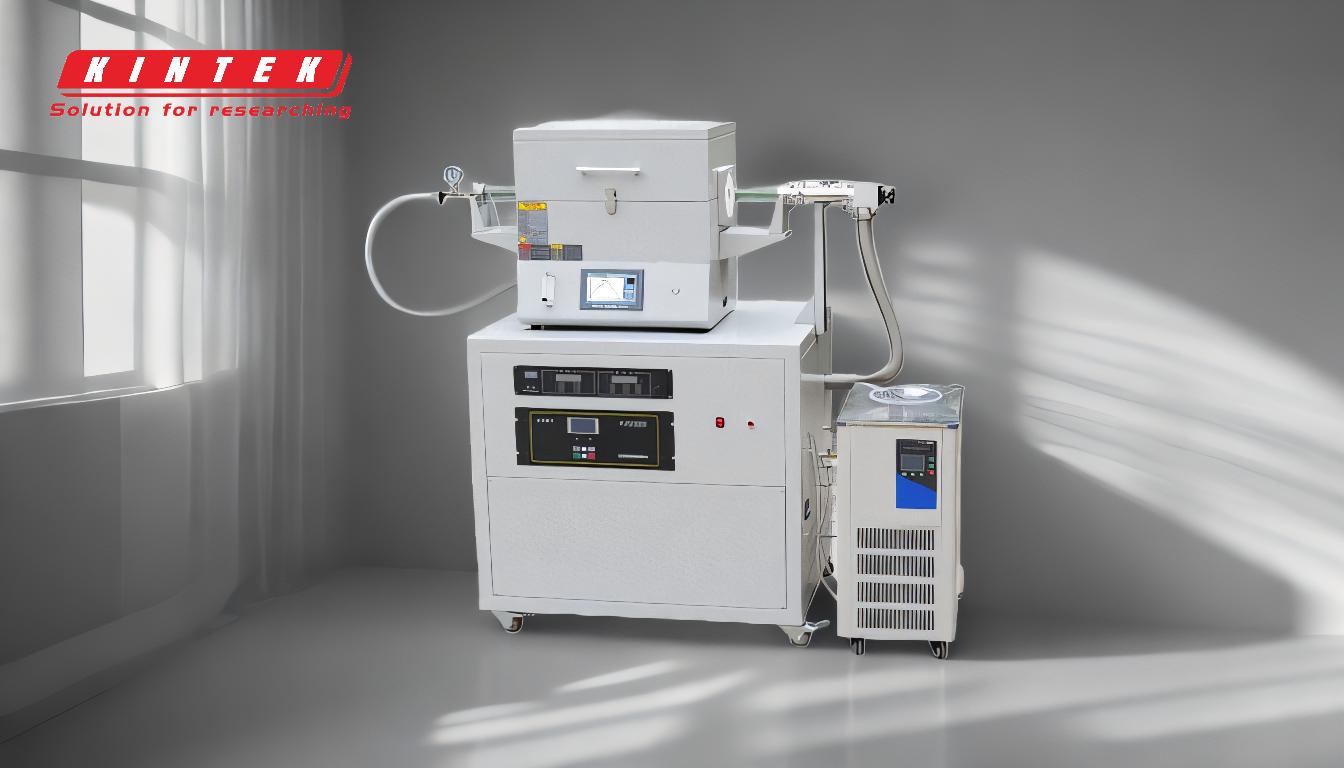
-
Definition of Furnace Brazing:
- Furnace brazing is a metal-joining process that uses a filler metal with a melting point above 450°C but below the melting point of the base metals. This process is widely used in industries requiring strong, leak-tight joints.
-
Factors Influencing Brazing Temperature:
- Base Metal Materials: The type of base metals being joined determines the appropriate brazing temperature. For example, stainless steel and titanium require higher temperatures compared to copper or aluminum.
- Braze Alloy: The filler metal's liquidus temperature (the temperature at which it fully melts) is critical. The brazing temperature must be at least 25°C above this point to ensure proper flow and bonding.
- Joint Requirements: The desired strength, corrosion resistance, and thermal properties of the joint also influence the brazing temperature.
-
Optimal Brazing Temperature:
- The ideal brazing temperature is the lowest possible within the recommended range to minimize thermal stress on the base materials while ensuring the filler metal flows adequately. This balance is crucial for achieving high-quality joints.
-
Role of Laboratory Muffle Furnaces:
- Laboratory muffle furnaces are commonly used for brazing due to their precise temperature control and uniform heating. These furnaces typically operate within a range of 1100°C to 1200°C, making them suitable for a wide variety of brazing applications.
-
Atmosphere Considerations:
- The furnace atmosphere (e.g., inert gas, vacuum, or reducing atmosphere) plays a significant role in preventing oxidation and ensuring clean, strong joints. The choice of atmosphere depends on the base metals and braze alloy used.
-
Equipment and Investment:
- Selecting the right furnace for brazing involves considering the size and quantity of parts, the required temperature range, and the type of atmosphere control. Laboratory muffle furnaces are often preferred for their versatility and precision.
By understanding these key points, a purchaser can make informed decisions about the appropriate furnace and brazing parameters for their specific application, ensuring optimal results and cost-effectiveness.
Summary Table:
Key Factor | Description |
---|---|
Base Metal Materials | Determines the brazing temperature (e.g., stainless steel requires higher heat). |
Braze Alloy | Must be at least 25°C above the liquidus temperature for proper flow. |
Joint Requirements | Strength, corrosion resistance, and thermal properties influence temperature. |
Optimal Temperature | Lowest within the range to minimize thermal stress while ensuring bonding. |
Muffle Furnace Range | Typically 1100°C to 1200°C, suitable for most brazing applications. |
Ready to optimize your brazing process? Contact us today for expert guidance and equipment solutions!