Metal casting is a complex process that requires precise temperature control to ensure the metal is properly melted, poured, and solidified. The temperature needed for metal casting depends on the type of metal being used, as each metal has a unique melting point and casting requirements. Generally, the temperature must be high enough to melt the metal completely but not so high that it causes defects or degradation. The process also involves preheating molds and maintaining specific cooling rates to achieve the desired properties in the final product. Below, we’ll explore the key factors that determine the appropriate temperature for metal casting.
Key Points Explained:
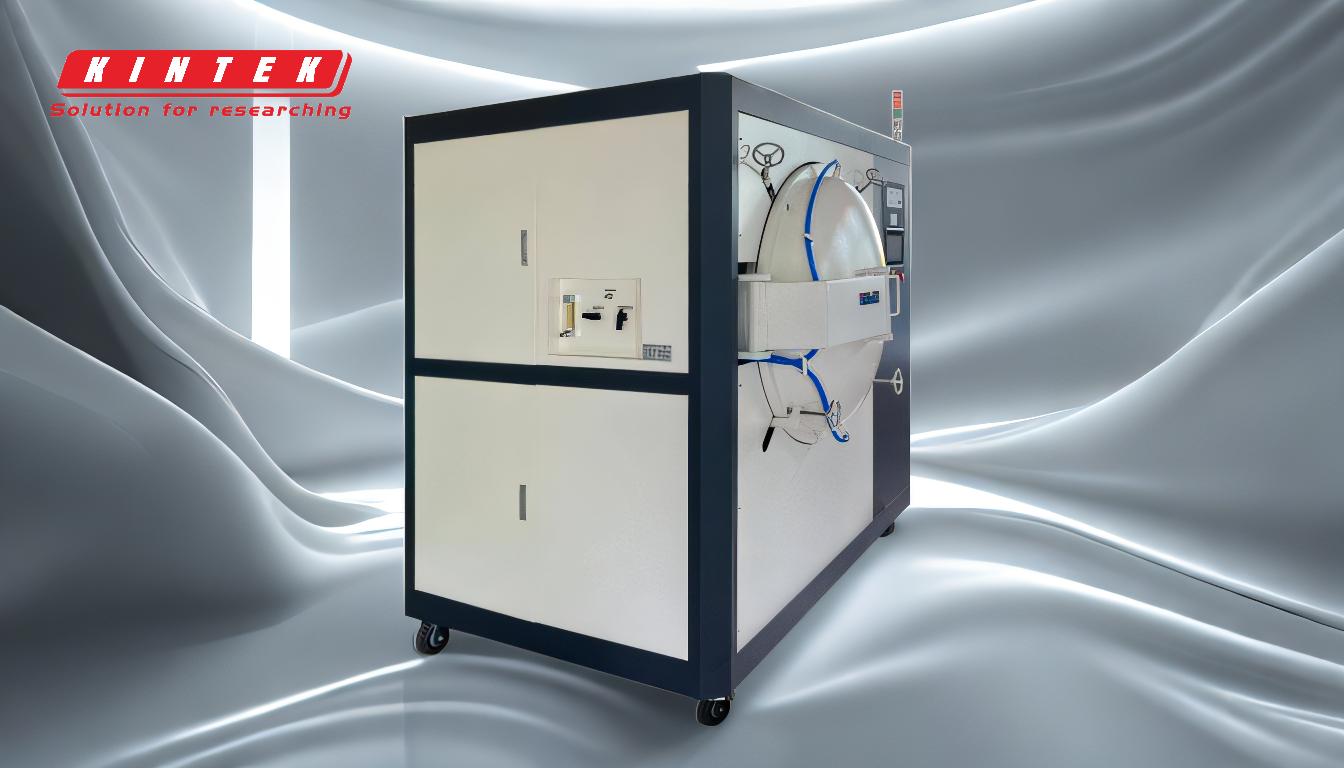
-
Melting Points of Common Casting Metals
Different metals have different melting points, which directly influence the casting temperature. For example:- Aluminum: Melts at approximately 660°C (1220°F). Casting temperatures are typically around 700–750°C (1292–1382°F) to ensure proper fluidity.
- Copper: Melts at 1085°C (1985°F), with casting temperatures ranging from 1100–1200°C (2012–2192°F).
- Iron: Melts at 1538°C (2800°F), and casting temperatures are usually between 1500–1600°C (2732–2912°F).
- Steel: Melts at around 1370–1510°C (2500–2750°F), depending on the alloy, with casting temperatures often exceeding 1600°C (2912°F).
-
Superheating the Metal
To ensure the metal is fully liquid and has good fluidity for pouring, it is often heated slightly above its melting point, a process called superheating. This helps prevent premature solidification and ensures the metal fills the mold completely. For example, aluminum is typically superheated to 700–750°C, while iron may require superheating to 1500–1600°C. -
Mold Preheating
The temperature of the mold is also critical. Preheating the mold prevents thermal shock, which can cause cracking or incomplete filling. For sand casting, molds are usually preheated to 200–300°C (392–572°F), while for investment casting, ceramic molds may be preheated to higher temperatures, depending on the metal being cast. -
Cooling Rates and Solidification
After pouring, the metal must cool and solidify at a controlled rate to achieve the desired microstructure and mechanical properties. Rapid cooling can lead to internal stresses or brittleness, while slow cooling may result in coarse grain structures. The cooling rate is influenced by the mold material, metal type, and casting design. -
Factors Affecting Casting Temperature
- Metal Composition: Alloys have different melting and casting temperatures compared to pure metals. For example, cast iron has a lower melting point than pure iron due to its carbon content.
- Casting Method: Different methods, such as sand casting, die casting, or investment casting, require varying temperatures to accommodate the mold material and process requirements.
- Part Geometry: Complex shapes may require higher temperatures to ensure the metal flows into all areas of the mold.
-
Temperature Measurement and Control
Accurate temperature measurement is essential for successful casting. Tools like pyrometers and thermocouples are used to monitor the molten metal and mold temperatures. Advanced furnaces, such as induction or electric arc furnaces, provide precise temperature control for different metals. -
Safety Considerations
Handling molten metal at high temperatures requires strict safety protocols. Protective gear, proper ventilation, and temperature monitoring systems are essential to prevent accidents and ensure a safe working environment.
In summary, the temperature required for metal casting depends on the type of metal, the casting method, and the desired properties of the final product. By carefully controlling the melting, pouring, and cooling processes, manufacturers can achieve high-quality castings with minimal defects.
Summary Table:
Metal | Melting Point | Casting Temperature Range |
---|---|---|
Aluminum | 660°C (1220°F) | 700–750°C (1292–1382°F) |
Copper | 1085°C (1985°F) | 1100–1200°C (2012–2192°F) |
Iron | 1538°C (2800°F) | 1500–1600°C (2732–2912°F) |
Steel | 1370–1510°C (2500–2750°F) | 1600°C+ (2912°F+) |
Need expert advice on achieving the perfect casting temperature? Contact us today for tailored solutions!