Sintering pottery involves heating ceramic materials to a temperature high enough to cause the particles to bond together, typically without melting the material. The exact temperature required depends on the type of ceramic being sintered. For most ceramics, sintering occurs at 50% to 75% of their melting temperature, which is generally above 1000°C. For example, porcelain can be sintered in a simple kiln, while advanced ceramics may require precise high-temperature sintering in a controlled atmosphere. The sintering temperature in experiments can reach up to 1800°C, and kilns are often designed to withstand temperatures up to 1288°C/2350°F.
Key Points Explained:
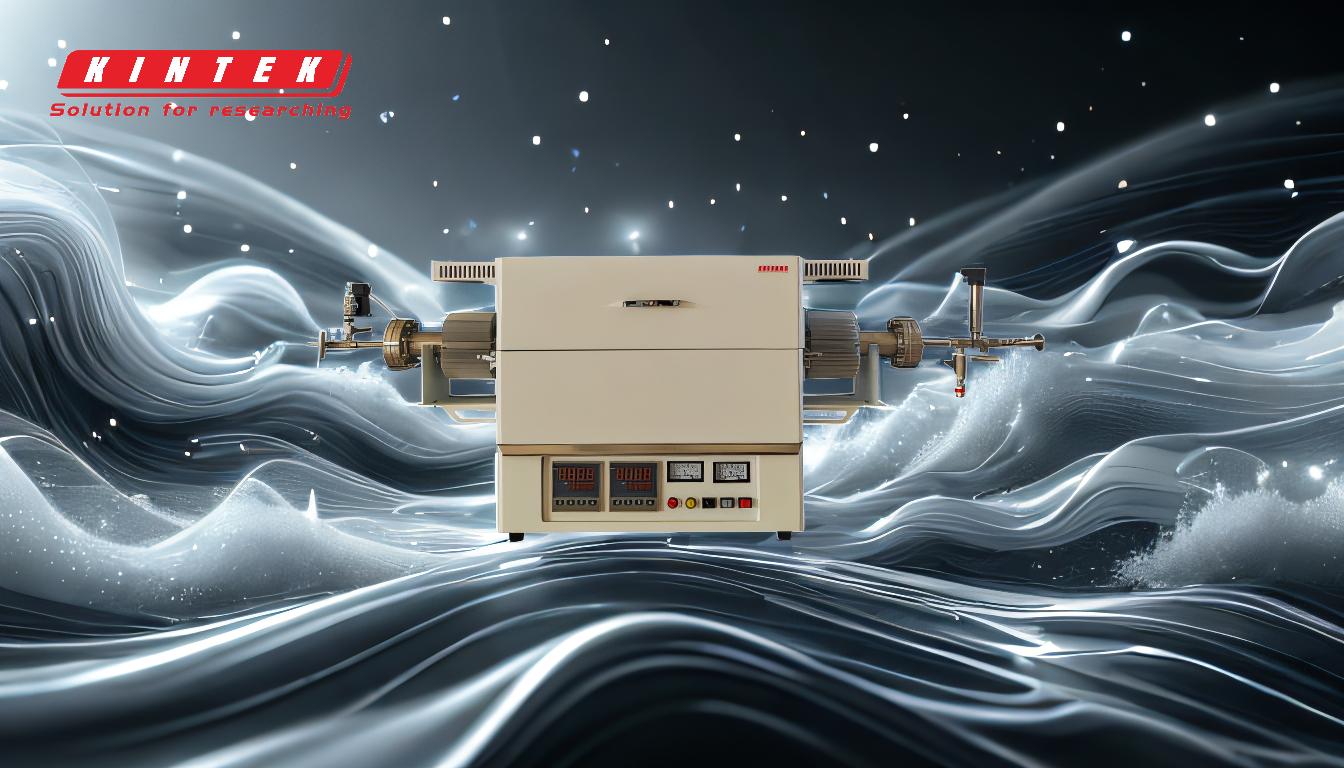
-
Temperature Range for Sintering:
- Sintering typically occurs at 50% to 75% of the ceramic material's melting temperature.
- For most ceramics, this means temperatures above 1000°C.
- Example: If a ceramic material has a melting temperature of 2000°C, the sintering temperature would be between 1000°C and 1500°C.
-
Variability Based on Ceramic Type:
- Porcelain: Can be sintered in a simple, low-cost kiln, typically at lower temperatures compared to advanced ceramics.
- Advanced Technical Non-Oxide Ceramics: Require high-temperature sintering, often in a precisely controlled atmosphere to prevent contamination and ensure stability.
-
Experimental Sintering Temperatures:
- In experiments, sintering temperatures can reach up to 1800°C, especially for advanced ceramics that require high-density bonding.
- This high temperature ensures that the ceramic reaches more than 95% of its theoretical density.
-
Kiln Design and Temperature Limits:
- Sintering kilns are designed to reach high temperatures, with some capable of reaching up to 1288°C/2350°F.
- The design must accommodate the specific needs of the ceramic being sintered, including temperature stability and atmosphere control.
-
Atmospheric Considerations:
- Shielding Gas: For sintering at atmospheric pressure, shielding gases like endothermic gas are used to prevent surface contamination.
- Vacuum Sintering: Pure metals and some ceramics may be sintered in a vacuum to avoid contamination and achieve higher purity.
-
Practical Implications for Purchasers:
- When purchasing equipment for sintering, consider the maximum temperature requirements of the ceramics you plan to sinter.
- Ensure the kiln or sintering furnace can maintain precise temperature control and, if necessary, a controlled atmosphere.
- For advanced ceramics, investing in high-temperature capable equipment with atmosphere control features is essential.
By understanding these key points, purchasers can make informed decisions about the equipment and consumables needed for their specific sintering requirements, ensuring optimal results for their ceramic products.
Summary Table:
Aspect | Details |
---|---|
Temperature Range | 50% to 75% of melting temperature, typically above 1000°C. |
Porcelain Sintering | Lower temperatures, simple kilns. |
Advanced Ceramics | High-temperature sintering (up to 1800°C), controlled atmosphere required. |
Kiln Design | Capable of reaching up to 1288°C/2350°F, with precise temperature control. |
Atmosphere Control | Shielding gases or vacuum for contamination-free sintering. |
Need help selecting the right sintering equipment? Contact our experts today for personalized advice!