Porcelain is fired at high temperatures, typically ranging between 1200°C (2192°F) and 1400°C (2552°F), depending on the type of porcelain and the desired characteristics of the final product. The firing process is crucial as it transforms the clay body into a dense, vitrified, and durable material. Low-fire porcelain is fired at the lower end of this range, while high-fire porcelain requires temperatures closer to 1400°C. The exact temperature depends on factors such as the composition of the clay, the glaze used, and the intended application of the porcelain. Proper firing ensures the porcelain achieves its signature strength, translucency, and resistance to water absorption.
Key Points Explained:
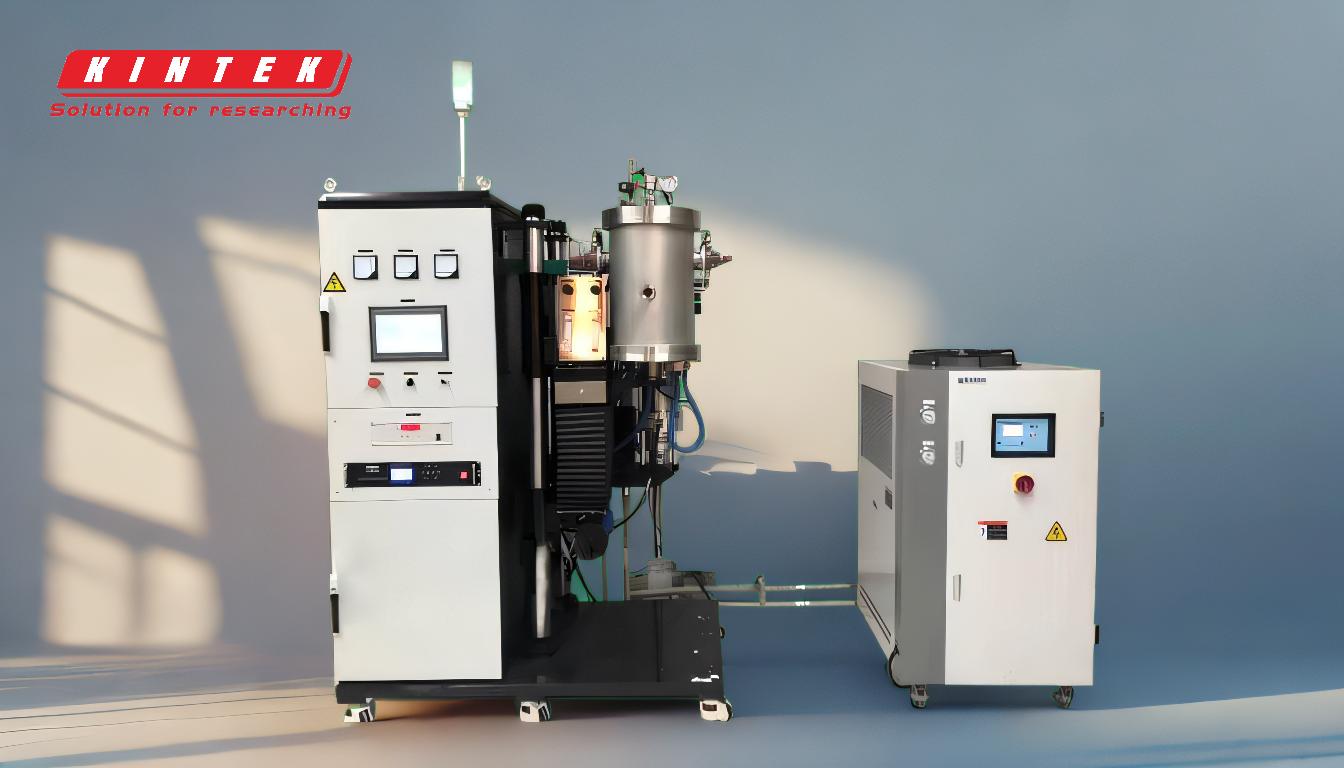
-
Temperature Range for Porcelain Firing:
- Porcelain is typically fired between 1200°C (2192°F) and 1400°C (2552°F). This range ensures the clay body vitrifies, becoming non-porous and durable.
- Low-fire porcelain is fired at 1200°C to 1280°C, while high-fire porcelain requires 1280°C to 1400°C.
-
Types of Porcelain and Their Firing Temperatures:
- Bone China: A type of porcelain fired at 1200°C to 1300°C. It contains bone ash, which gives it a unique translucency and strength.
- Hard-Paste Porcelain: Fired at 1300°C to 1400°C, this type is known for its durability and resistance to thermal shock.
- Soft-Paste Porcelain: Fired at lower temperatures (around 1200°C to 1250°C), it is less durable but easier to work with.
-
Factors Influencing Firing Temperature:
- Clay Composition: The mineral content of the clay affects the required firing temperature. For example, kaolin-rich clays need higher temperatures.
- Glaze Compatibility: The glaze must mature at the same temperature as the clay body to ensure a smooth, durable finish.
- Desired Characteristics: Higher temperatures result in greater strength and translucency, while lower temperatures may be used for decorative pieces.
-
Firing Process and Stages:
- Bisque Firing: The first firing, done at 900°C to 1000°C, removes physical and chemical water from the clay, making it harder and ready for glazing.
- Glaze Firing: The second firing, done at the higher porcelain range (1200°C to 1400°C), melts the glaze and fully vitrifies the clay body.
-
Importance of Temperature Control:
- Precise temperature control is critical to avoid defects such as cracking, warping, or under-vitrification.
- Modern kilns, such as electric or gas kilns, allow for accurate temperature regulation, ensuring consistent results.
-
Applications of Porcelain and Firing Considerations:
- Tableware: Requires high durability and resistance to thermal shock, often fired at higher temperatures.
- Artistic and Decorative Pieces: May be fired at lower temperatures for ease of shaping and glazing.
- Industrial Porcelain: Used in electrical insulators and laboratory equipment, typically fired at the highest temperatures for maximum strength and durability.
By understanding the firing temperatures and processes, a purchaser can select the right type of porcelain for their specific needs, ensuring the final product meets the desired quality and functionality standards.
Summary Table:
Aspect | Details |
---|---|
Temperature Range | 1200°C (2192°F) to 1400°C (2552°F) |
Low-Fire Porcelain | 1200°C to 1280°C |
High-Fire Porcelain | 1280°C to 1400°C |
Types of Porcelain | Bone China (1200°C-1300°C), Hard-Paste (1300°C-1400°C), Soft-Paste (1200°C-1250°C) |
Key Factors | Clay composition, glaze compatibility, desired characteristics |
Firing Stages | Bisque Firing (900°C-1000°C), Glaze Firing (1200°C-1400°C) |
Applications | Tableware, artistic pieces, industrial porcelain |
Need help selecting the right porcelain for your needs? Contact our experts today!