Compression moulding is a versatile manufacturing process widely used across various industries due to its ability to produce high-strength, durable, and complex parts. It involves placing a pre-measured amount of material into a heated mould cavity, which is then compressed under high pressure to form the desired shape. This method is particularly advantageous for producing large, intricate components with consistent quality. Industries such as automotive, aerospace, electronics, and consumer goods rely on compression moulding for creating parts like seals, gaskets, electrical insulators, and even composite materials. Its efficiency, cost-effectiveness, and ability to handle a wide range of materials make it a preferred choice for many applications.
Key Points Explained:
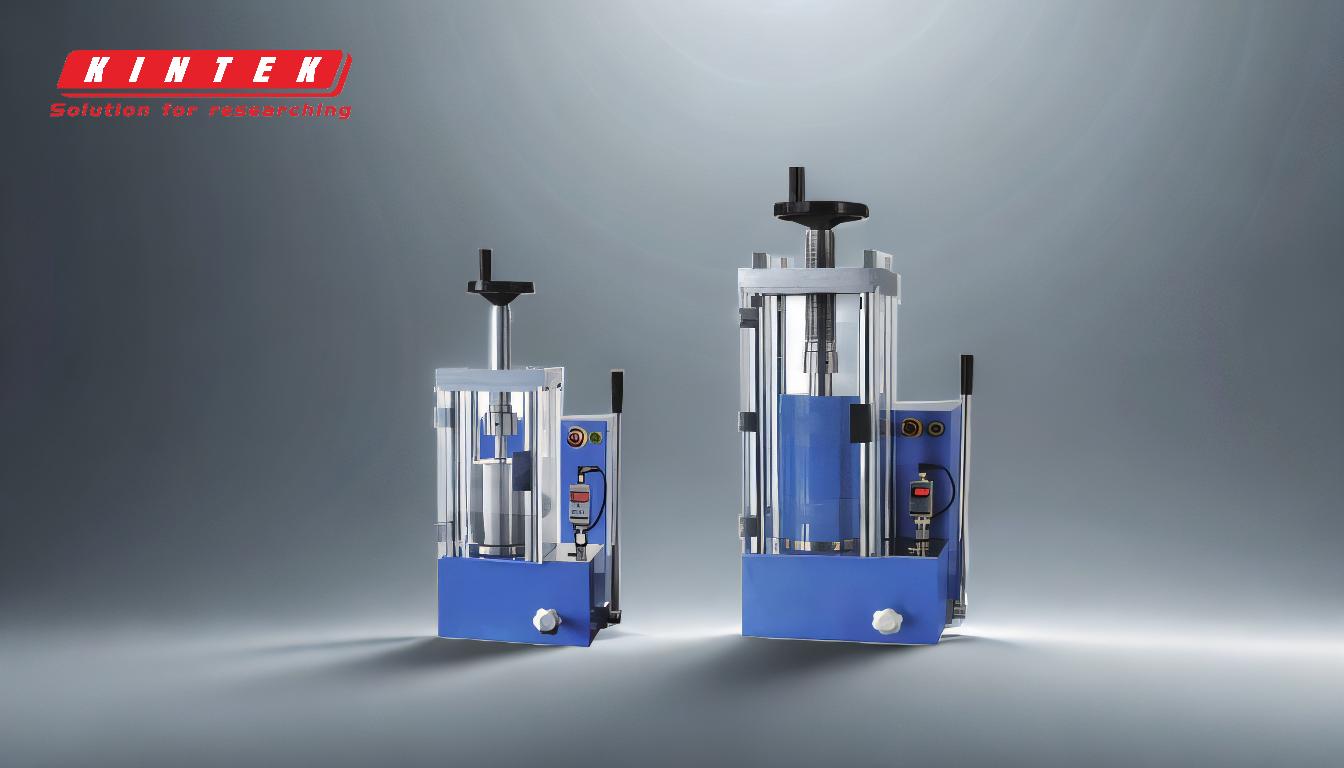
-
Automotive Industry:
- Compression moulding is extensively used in the automotive sector to manufacture parts such as rubber seals, gaskets, and vibration dampers. These components require high durability and resistance to environmental factors like heat, chemicals, and wear.
- The process is also employed to produce composite materials used in lightweight vehicle components, contributing to fuel efficiency and reduced emissions.
-
Aerospace Industry:
- In aerospace, compression moulding is crucial for creating high-performance composite parts that need to withstand extreme conditions. These include structural components, interior panels, and insulation materials.
- The ability to produce parts with high strength-to-weight ratios makes compression moulding ideal for aerospace applications where weight reduction is critical.
-
Electronics and Electrical Industry:
- Compression moulding is used to produce electrical insulators, connectors, and housings for electronic devices. These parts often require precise dimensions and excellent electrical insulation properties.
- The process ensures consistent quality and reliability, which is essential for electronic components that must perform under varying electrical and thermal conditions.
-
Consumer Goods:
- Many everyday items, such as kitchenware, appliance parts, and even toys, are manufactured using compression moulding. The process allows for the production of durable and aesthetically pleasing products.
- It is also used for creating handles, knobs, and other ergonomic components that require a comfortable grip and long-lasting performance.
-
Medical and Healthcare Industry:
- Compression moulding is employed to produce medical devices and components that require biocompatibility and sterilization. Examples include surgical instruments, prosthetics, and dental appliances.
- The process ensures that these medical parts meet stringent regulatory standards and perform reliably in critical healthcare applications.
-
Construction and Building Materials:
- In the construction industry, compression moulding is used to create insulation panels, seals, and gaskets for windows and doors. These components need to provide effective thermal and acoustic insulation.
- The process is also used for manufacturing composite materials used in structural applications, offering enhanced durability and resistance to environmental factors.
-
Advantages of Compression Moulding:
- Cost-Effectiveness: Compression moulding is a cost-efficient method for producing large quantities of parts with minimal material waste.
- Material Versatility: It can handle a wide range of materials, including thermosetting plastics, rubber, and composites, making it suitable for diverse applications.
- High Strength and Durability: The process produces parts with excellent mechanical properties, ensuring long-lasting performance in demanding environments.
-
Limitations and Considerations:
- While compression moulding offers numerous benefits, it may not be suitable for very complex geometries or parts requiring extremely tight tolerances.
- The process requires precise control over temperature, pressure, and curing time to ensure consistent quality, which can be challenging for some manufacturers.
In conclusion, compression moulding is a highly versatile and efficient manufacturing process used across a wide range of industries. Its ability to produce durable, high-quality parts with consistent performance makes it an essential technique in modern manufacturing. Whether in automotive, aerospace, electronics, or consumer goods, compression moulding continues to play a critical role in shaping the products we rely on every day.
Summary Table:
Industry | Applications |
---|---|
Automotive | Rubber seals, gaskets, vibration dampers, lightweight composite materials |
Aerospace | Structural components, interior panels, insulation materials |
Electronics | Electrical insulators, connectors, housings |
Consumer Goods | Kitchenware, appliance parts, handles, knobs, toys |
Medical and Healthcare | Surgical instruments, prosthetics, dental appliances |
Construction | Insulation panels, seals, gaskets, composite materials for structural use |
Discover how compression moulding can benefit your industry—contact us today to learn more!