In the Physical Vapor Deposition (PVD) coating process, various gases are used depending on the desired coating properties and the specific PVD technique employed. Argon is the most commonly used inert gas due to its non-reactive nature, ensuring the purity of the coating material during vaporization. Reactive gases like oxygen, nitrogen, methane, and acetylene are also used to form compound coatings such as oxides, nitrides, and carbides. The choice of gas depends on the coating material, the substrate, and the intended application of the coated product.
Key Points Explained:
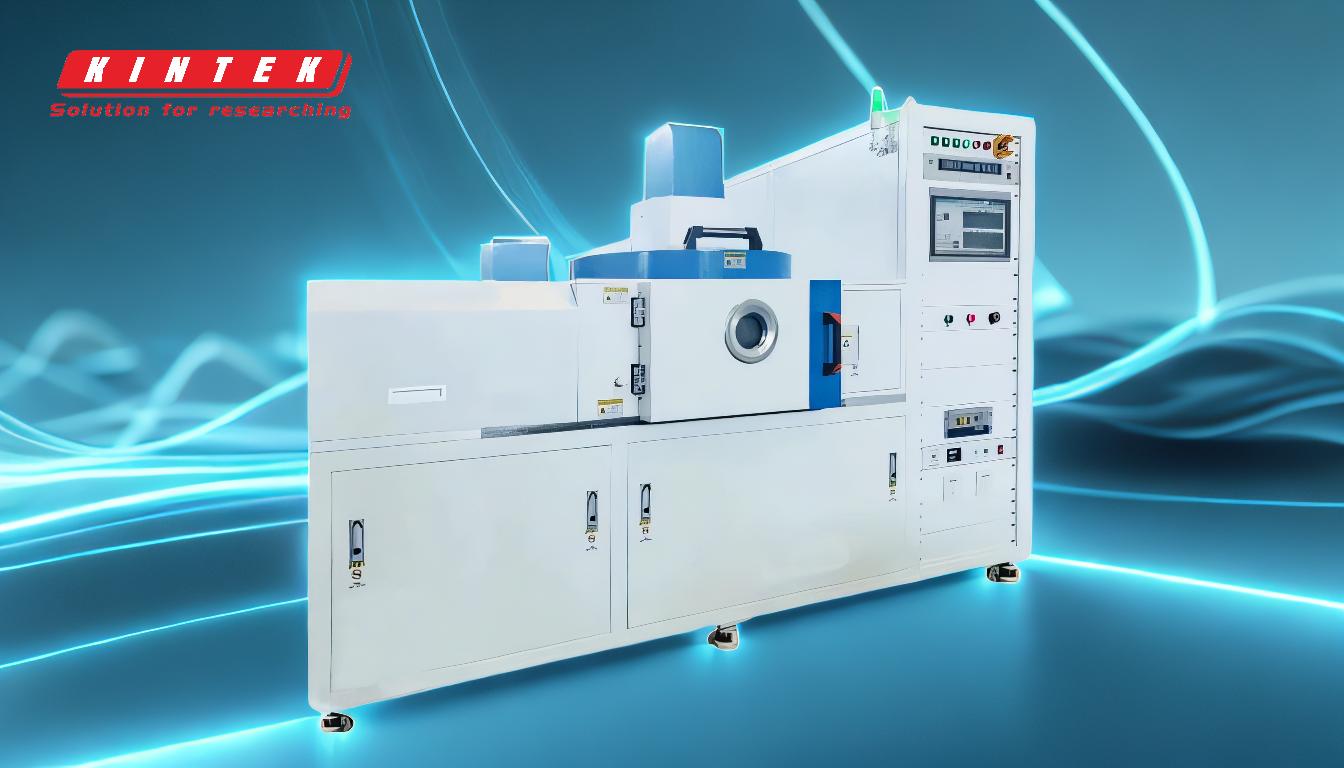
-
Argon as the Primary Inert Gas:
- Role: Argon is widely used in PVD because it is inert, meaning it does not chemically react with the coating material or the substrate. This ensures that the coating material remains pure during the vaporization and deposition stages.
- Process: During magnetron sputtering or cathodic arc evaporation, argon ions are used to bombard the target material, causing it to vaporize and form a plasma. The vaporized material then deposits onto the substrate.
- Advantages: Argon's inert nature makes it ideal for creating pure metallic coatings without introducing impurities.
-
Reactive Gases for Compound Coatings:
- Oxygen (O2): Used to form metal oxide coatings (e.g., titanium dioxide, aluminum oxide). These coatings are often used for their hardness, wear resistance, and optical properties.
- Nitrogen (N2): Reacts with metal atoms to form nitrides (e.g., titanium nitride, chromium nitride), which are known for their hardness, corrosion resistance, and decorative gold-like appearance.
- Methane (CH4) and Acetylene (C2H2): Used to create carbide coatings (e.g., titanium carbide, silicon carbide), which are extremely hard and wear-resistant. Acetylene is particularly used for diamond-like carbon (DLC) coatings.
- Hexa-Methyl-Disiloxane (HMDSO): Used in Plasma-Assisted Chemical Vapor Deposition (PACVD) to create silicon-containing coatings, which are often used for their optical and barrier properties.
-
Gas Selection Based on PVD Technique:
- Magnetron Sputtering: Argon is the primary sputtering gas, but reactive gases like nitrogen or oxygen can be introduced to form compound coatings.
- Cathodic Arc Evaporation: Argon is used as the primary gas, but reactive gases can be added to modify the coating properties.
- Thermal or Electron Beam Evaporation: Argon is typically used, but reactive gases can be introduced to form compound coatings.
-
Process Gas Input System:
- Gas Supply: Gases are supplied from cylinders and controlled through valves and meters to ensure precise flow rates.
- Vacuum Chamber: The gases are introduced into the vacuum chamber, where they interact with the vaporized coating material to form the desired coating.
-
Applications of Different Gases:
- Decorative Coatings: Nitrogen is often used to create gold-like coatings for decorative purposes.
- Functional Coatings: Oxygen and methane are used to create hard, wear-resistant coatings for industrial applications.
- Optical Coatings: HMDSO is used to create coatings with specific optical properties.
-
Importance of Gas Purity:
- High-purity gases are essential to avoid contamination and ensure consistent coating quality. Impurities in the gas can lead to defects in the coating, reducing its performance and durability.
By carefully selecting the appropriate gas or gas mixture, manufacturers can tailor the properties of the PVD coating to meet specific application requirements, whether for decorative, functional, or optical purposes.
Summary Table:
Gas Type | Role in PVD Coating | Common Applications |
---|---|---|
Argon (Ar) | Inert gas for pure metallic coatings, used in sputtering and evaporation processes. | Pure metallic coatings, ensuring no impurities. |
Oxygen (O2) | Forms metal oxide coatings (e.g., TiO2, Al2O3) for hardness and wear resistance. | Hard, wear-resistant coatings for industrial applications. |
Nitrogen (N2) | Creates nitrides (e.g., TiN, CrN) for hardness, corrosion resistance, and decoration. | Decorative gold-like coatings and functional wear-resistant layers. |
Methane (CH4) | Forms carbide coatings (e.g., TiC, SiC) for extreme hardness and wear resistance. | Industrial applications requiring high durability. |
Acetylene (C2H2) | Used for diamond-like carbon (DLC) coatings. | High-performance coatings for tools and machinery. |
HMDSO | Creates silicon-containing coatings for optical and barrier properties. | Optical coatings and protective barrier layers. |
Need help selecting the right gases for your PVD coating process? Contact our experts today for tailored solutions!