The carburizing process, while widely used for surface hardening of steel components, has several disadvantages depending on the method employed (atmosphere or vacuum carburizing). These include high initial capital costs, the need for empirical process control, environmental and safety concerns, and challenges related to equipment maintenance and post-processing. Each method has its unique drawbacks, such as soot and tar formation in vacuum carburizing or case depth quality issues in atmosphere carburizing. Understanding these disadvantages is crucial for equipment and consumable purchasers to make informed decisions.
Key Points Explained:
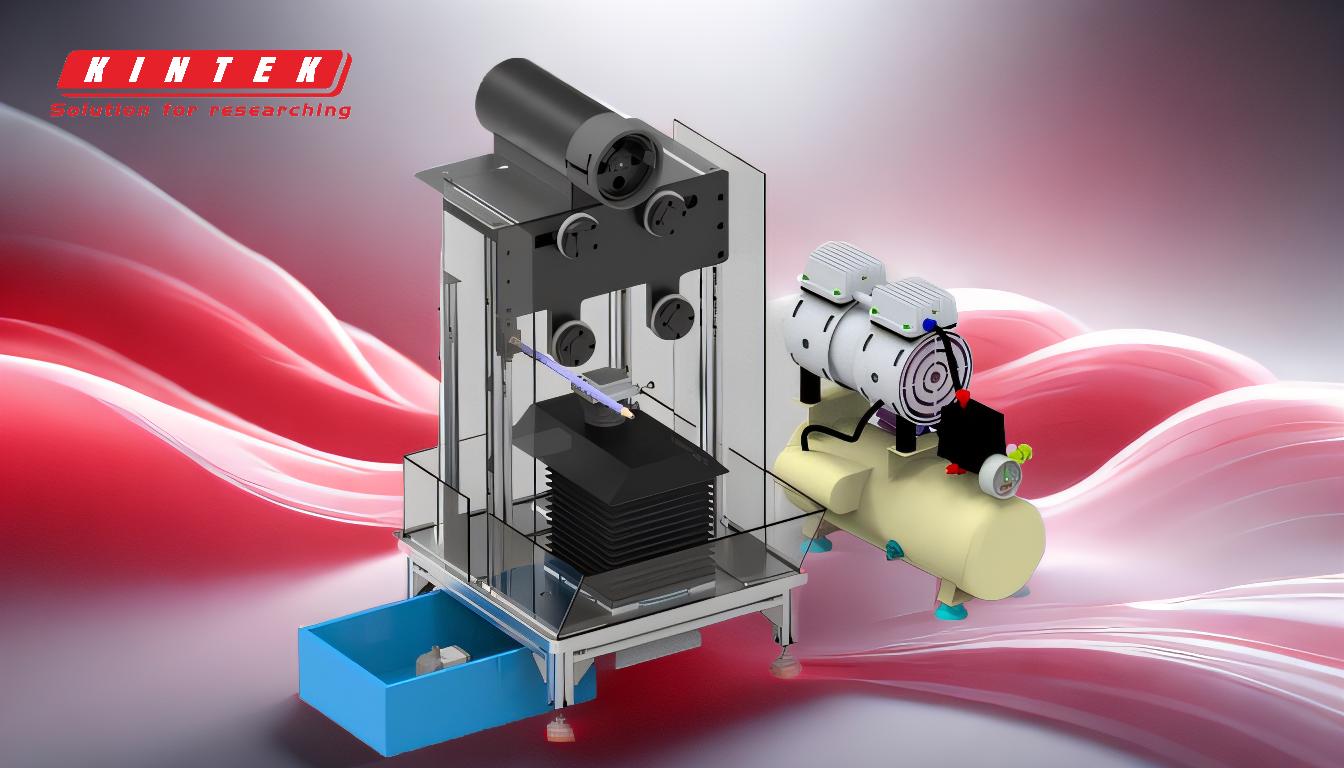
-
High Initial Capital Equipment Cost:
- Explanation: Vacuum carburizing requires specialized equipment, which often comes with a higher initial investment compared to traditional atmosphere carburizing. This includes advanced vacuum chambers, gas handling systems, and precise temperature control mechanisms.
- Impact: For businesses, this means a significant upfront financial commitment, which may not be feasible for smaller operations or those with limited budgets.
-
Empirical Process Control:
- Explanation: Both atmosphere and vacuum carburizing rely heavily on empirical data to achieve repeatable results. This means that operators must have extensive experience and conduct numerous trial runs to determine the optimal settings for each specific load.
- Impact: This reliance on trial-and-error can lead to inefficiencies, increased production time, and higher costs due to the need for skilled personnel and potential material wastage during testing.
-
Formation of Soot and Tar (Vacuum Carburizing):
- Explanation: In vacuum carburizing, the type, pressure, and quantity of hydrocarbon gas introduced can lead to the formation of soot and tar. These byproducts can contaminate the equipment and the parts being processed.
- Impact: This necessitates frequent cleaning and maintenance of the equipment, increasing downtime and operational costs. Additionally, the presence of soot and tar can affect the quality of the carburized layer, potentially leading to rework or scrapping of parts.
-
Equipment Conditioning (Atmosphere Carburizing):
- Explanation: Atmosphere carburizing equipment must be properly conditioned if it is idled or shut down for any period. This involves purging the system and ensuring that the atmosphere is correctly balanced before resuming operations.
- Impact: This requirement can lead to delays in production, especially if the equipment is frequently stopped and started. It also adds to the operational complexity and requires additional resources for maintenance.
-
Large Material Allowances for Post-Processing:
- Explanation: Both methods often require significant material allowances to accommodate post-processing operations such as grinding or machining. This is necessary to achieve the final dimensions and surface finish after carburizing.
- Impact: This increases material costs and can lead to higher waste generation, which may not be sustainable or cost-effective in the long run.
-
Case Depth Quality Issues:
- Explanation: Achieving consistent case depth can be challenging in atmosphere carburizing due to variations in the carbon potential of the atmosphere and other process variables.
- Impact: Inconsistent case depth can lead to parts that do not meet specifications, resulting in rework, scrap, or even failure in service. This variability can also complicate quality control processes.
-
Environmental Pollution and Safety Concerns:
- Explanation: Atmosphere carburizing involves the use of potentially hazardous gases, which require constant monitoring to prevent environmental pollution and ensure workplace safety.
- Impact: This adds to the operational burden, requiring investments in safety equipment, training, and compliance with environmental regulations. Failure to manage these aspects properly can result in fines, legal issues, and harm to the company’s reputation.
In summary, while carburizing is an effective method for enhancing the surface properties of steel components, it comes with several disadvantages that must be carefully considered. These include high initial costs, the need for empirical process control, environmental and safety concerns, and challenges related to equipment maintenance and post-processing. Understanding these drawbacks is essential for making informed decisions when selecting and implementing carburizing processes.
Summary Table:
Disadvantage | Method | Impact |
---|---|---|
High Initial Capital Equipment Cost | Vacuum Carburizing | Significant upfront investment, challenging for smaller operations |
Empirical Process Control | Both Methods | Requires skilled personnel, trial-and-error, and increased production time |
Formation of Soot and Tar | Vacuum Carburizing | Frequent cleaning, equipment contamination, and potential part rework |
Equipment Conditioning | Atmosphere Carburizing | Delays in production and added operational complexity |
Large Material Allowances | Both Methods | Increased material costs and higher waste generation |
Case Depth Quality Issues | Atmosphere Carburizing | Inconsistent results, rework, or scrapping of parts |
Environmental Pollution | Atmosphere Carburizing | Safety concerns, regulatory compliance, and potential fines |
Need help choosing the right surface hardening process? Contact our experts today for tailored solutions!