When selecting metals that can withstand high temperatures, it is essential to consider factors such as melting point, thermal stability, oxidation resistance, and mechanical strength under extreme conditions. Metals like tungsten, molybdenum, tantalum, and nickel-based alloys are renowned for their high-temperature performance. Tungsten has the highest melting point of all metals, making it ideal for applications like aerospace and lighting. Molybdenum offers excellent thermal conductivity and resistance to thermal shock, while tantalum is highly corrosion-resistant and suitable for chemical processing. Nickel-based alloys, such as Inconel, combine high-temperature strength with oxidation resistance, making them perfect for jet engines and gas turbines. Understanding the specific requirements of your application will help you choose the most suitable metal.
Key Points Explained:
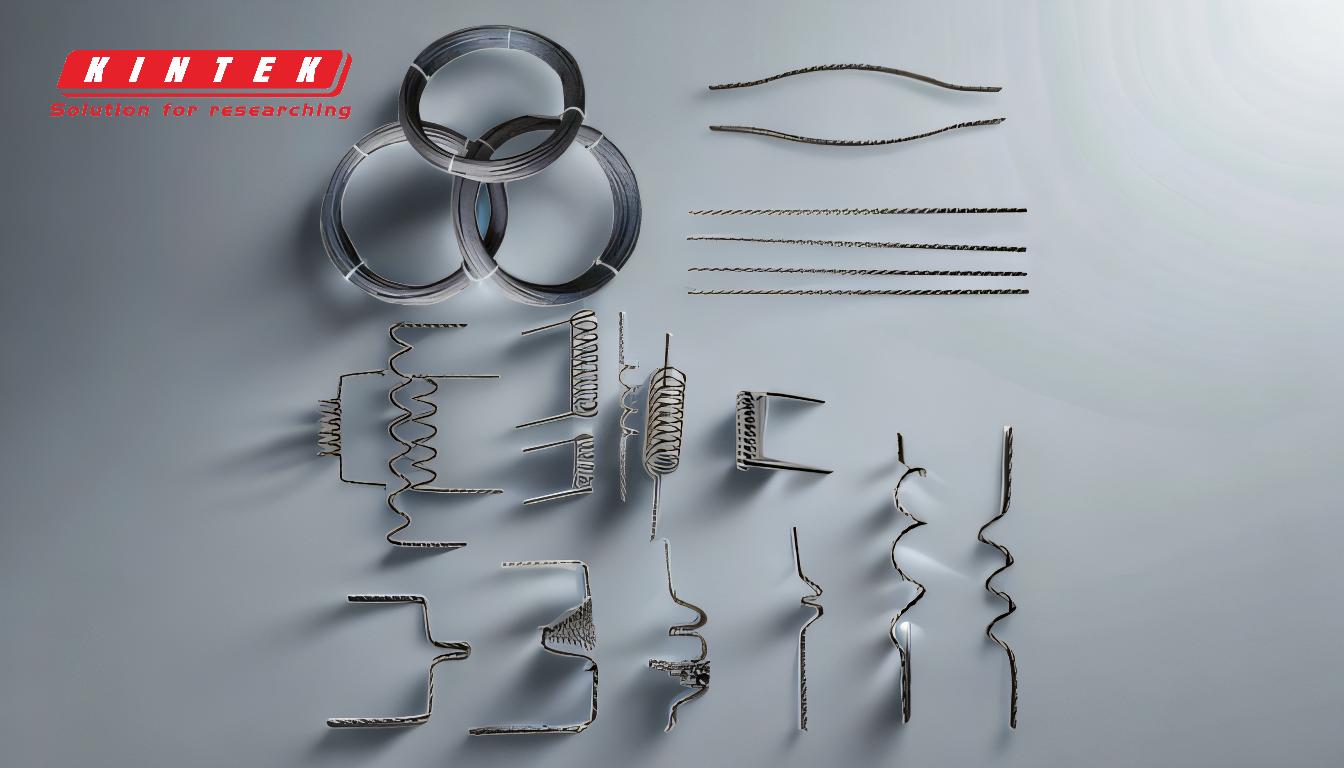
-
Tungsten:
- Melting Point: Tungsten has the highest melting point of all metals at 3,422°C (6,192°F), making it ideal for extreme high-temperature environments.
- Applications: Commonly used in aerospace, lighting (filaments in incandescent bulbs), and electronics.
- Advantages: Exceptional thermal stability, high density, and excellent mechanical strength at elevated temperatures.
- Limitations: Brittle at room temperature and prone to oxidation at high temperatures unless protected by an inert atmosphere or coating.
-
Molybdenum:
- Melting Point: Molybdenum melts at 2,623°C (4,753°F), making it suitable for high-temperature applications.
- Applications: Used in furnace components, aerospace, and electronics.
- Advantages: High thermal conductivity, resistance to thermal shock, and good strength at elevated temperatures.
- Limitations: Susceptible to oxidation at temperatures above 600°C (1,112°F), requiring protective coatings or environments.
-
Tantalum:
- Melting Point: Tantalum has a melting point of 3,017°C (5,463°F), making it highly resistant to heat.
- Applications: Ideal for chemical processing equipment, capacitors, and high-temperature furnace parts.
- Advantages: Excellent corrosion resistance, particularly in acidic environments, and good ductility.
- Limitations: Expensive and less commonly used due to cost, but invaluable in specific high-temperature, corrosive environments.
-
Nickel-Based Alloys (e.g., Inconel):
- Melting Point: Nickel-based alloys typically have melting points around 1,400°C (2,552°F), but their strength and oxidation resistance make them suitable for high-temperature applications.
- Applications: Widely used in jet engines, gas turbines, and nuclear reactors.
- Advantages: Excellent oxidation and corrosion resistance, high mechanical strength, and durability under cyclic thermal stress.
- Limitations: Higher cost compared to some other metals, but justified by their performance in extreme conditions.
-
Other Considerations:
- Oxidation Resistance: Metals like tungsten and molybdenum require protective coatings or inert atmospheres to prevent oxidation at high temperatures.
- Mechanical Properties: Strength, ductility, and thermal expansion coefficients must be evaluated to ensure the metal can withstand thermal cycling and mechanical stress.
- Cost and Availability: While some high-temperature metals like tungsten and tantalum are expensive, their unique properties often justify the cost for critical applications.
By understanding these key points, you can make an informed decision when selecting a metal for high-temperature applications, ensuring it meets the specific demands of your project.
Summary Table:
Metal | Melting Point (°C) | Key Applications | Advantages | Limitations |
---|---|---|---|---|
Tungsten | 3,422 | Aerospace, lighting | Highest melting point, thermal stability | Brittle at room temperature, prone to oxidation |
Molybdenum | 2,623 | Furnace components, electronics | High thermal conductivity, thermal shock resistance | Susceptible to oxidation above 600°C |
Tantalum | 3,017 | Chemical processing | Excellent corrosion resistance, ductility | Expensive, less common |
Nickel Alloys | ~1,400 | Jet engines, gas turbines | High strength, oxidation resistance | Higher cost, justified by performance |
Need help choosing the right high-temperature metal for your project? Contact our experts today for tailored solutions!