The production of carbon nanotubes (CNTs) involves several methods, each with its own advantages and limitations. The most common methods include chemical vapor deposition (CVD), laser ablation, and arc discharge. CVD is the dominant commercial process due to its cost-effectiveness and structural controllability. However, not all methods are equally viable or widely adopted for large-scale production. This analysis will explore the methods used for CNT production and identify which methods are less suitable or not used at all.
Key Points Explained:
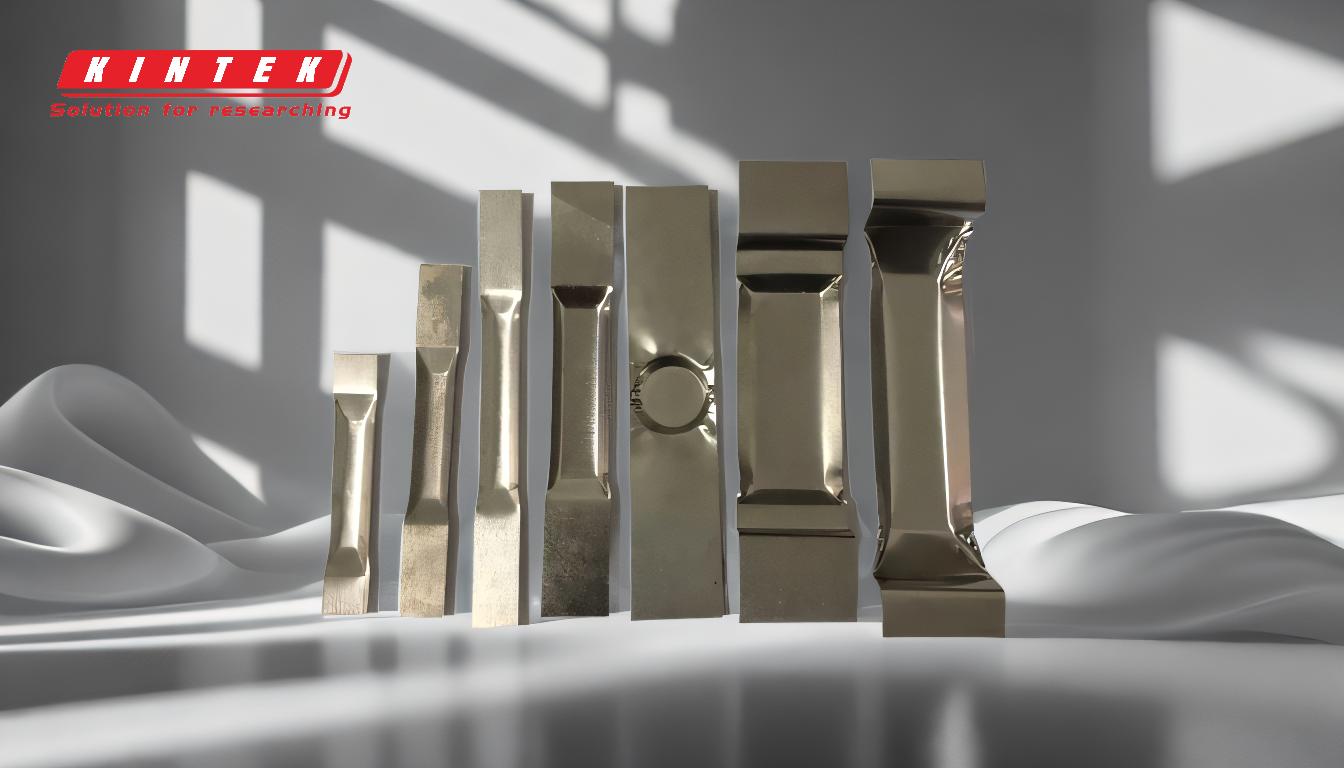
-
Chemical Vapor Deposition (CVD):
- CVD is the most widely used method for producing carbon nanotubes commercially.
- It involves the decomposition of hydrocarbon gases at high temperatures in the presence of a catalyst.
- The process allows for precise control over the structure and properties of the CNTs, making it highly cost-effective and scalable.
- CVD is associated with thermal treatments and gas-phase rearrangement, which are critical for achieving high-quality CNTs.
- The method is also environmentally friendly compared to other techniques, as it can be optimized to reduce material and energy consumption.
-
Laser Ablation:
- Laser ablation involves using a high-powered laser to vaporize a carbon target in the presence of a catalyst.
- This method can produce high-quality CNTs, but it is less cost-effective and scalable compared to CVD.
- The process requires expensive equipment and consumes a significant amount of energy, making it less suitable for large-scale production.
- Laser ablation is typically used in research settings rather than industrial applications.
-
Arc Discharge:
- Arc discharge involves creating an electric arc between two carbon electrodes in an inert gas atmosphere.
- This method can produce CNTs, but it is less controllable and yields a mixture of different carbon structures, including fullerenes and amorphous carbon.
- The process is energy-intensive and less efficient than CVD, limiting its use in commercial production.
- Arc discharge is primarily used for producing multi-walled carbon nanotubes (MWCNTs) rather than single-walled carbon nanotubes (SWCNTs).
-
Emerging Methods:
- Emerging methods for CNT production include the use of green or waste feedstocks, such as carbon dioxide captured by electrolysis in molten salts and methane pyrolysis.
- These methods aim to reduce the environmental impact of CNT production by utilizing alternative carbon sources.
- While promising, these methods are still in the experimental or early development stages and have not yet been widely adopted for commercial production.
-
Methods Not Used for CNT Production:
- Some methods, such as mechanical milling or chemical exfoliation, are not suitable for producing carbon nanotubes.
- Mechanical milling involves grinding carbon materials into fine particles, which does not result in the formation of CNTs.
- Chemical exfoliation, used for producing graphene, involves separating layers of graphite, which is not applicable to the synthesis of CNTs.
- These methods lack the necessary conditions, such as high temperatures and catalysts, required for the formation of CNTs.
In summary, while CVD, laser ablation, and arc discharge are established methods for producing carbon nanotubes, emerging methods using green feedstocks are still under development. Methods like mechanical milling and chemical exfoliation are not used for CNT production due to their inability to meet the specific requirements for forming CNTs.
Summary Table:
Method | Suitability for CNT Production | Key Limitations |
---|---|---|
Chemical Vapor Deposition (CVD) | Highly Suitable | None; cost-effective, scalable, and environmentally friendly. |
Laser Ablation | Less Suitable | Expensive equipment, high energy consumption, and limited scalability. |
Arc Discharge | Less Suitable | Energy-intensive, less controllable, and yields mixed carbon structures. |
Mechanical Milling | Not Suitable | Grinds carbon into particles; does not form CNTs. |
Chemical Exfoliation | Not Suitable | Separates graphite layers; not applicable for CNT synthesis. |
Want to learn more about carbon nanotube production methods? Contact us today for expert guidance!