Heat treatment is a critical process in metallurgy and materials science, used to alter the physical and sometimes chemical properties of materials, particularly metals. The two primary heating technologies used in heat treatments are induction heating and resistance heating. Induction heating is widely used for its precision and efficiency, especially in processes like induction hardening and annealing. Resistance heating, on the other hand, is versatile and commonly employed in furnaces for processes such as tempering and normalizing. Both technologies have distinct advantages and are chosen based on the specific requirements of the heat treatment process.
Key Points Explained:
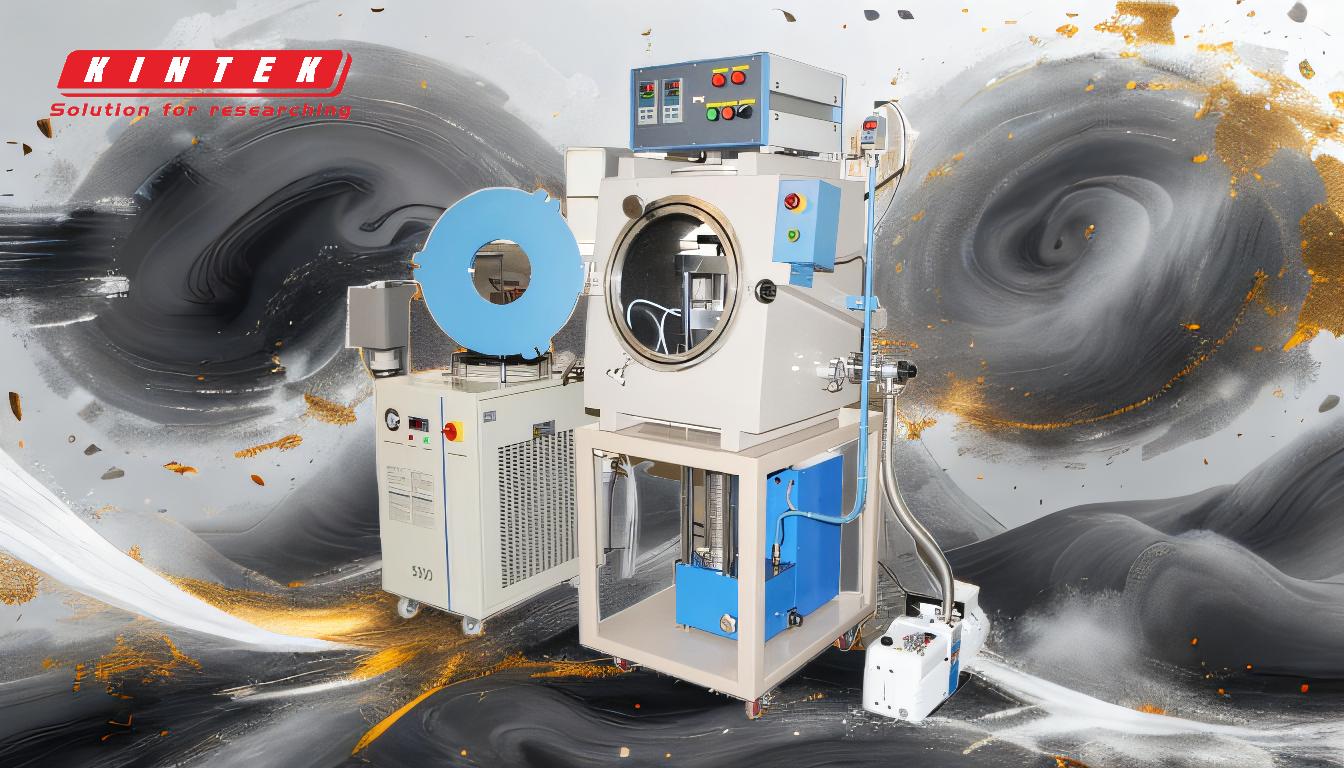
-
Induction Heating:
- How It Works: Induction heating uses electromagnetic induction to generate heat within the material. An alternating current passes through a coil, creating a magnetic field that induces eddy currents in the conductive material, heating it up.
-
Applications:
- Induction Hardening: Used to harden the surface of steel parts, improving wear resistance while maintaining a softer, more ductile core.
- Induction Annealing: Selectively softens specific areas of a metal part, making it easier to work with or reducing internal stresses.
- Induction Soldering/Brazing: Joins metal components by heating them to a temperature where a filler metal melts and flows into the joint.
- Advantages: High precision, fast heating, energy efficiency, and the ability to target specific areas of a part.
-
Resistance Heating:
- How It Works: Resistance heating relies on the principle of Joule heating, where electrical resistance in a material generates heat when an electric current passes through it. This is commonly achieved using heating elements like resistance wires, silicon carbon rods, or molybdenum bands.
-
Applications:
- Furnace Heating: Used in processes like annealing, tempering, and normalizing, where uniform heating of the entire part is required.
- Hot Pressing: Indirect resistance heating is used in hot pressing technology to apply heat and pressure simultaneously, often for sintering or bonding materials.
- Advantages: Uniform heating, versatility in temperature range, and suitability for batch processing.
-
Comparison of Induction and Resistance Heating:
- Precision: Induction heating offers better precision for localized heating, while resistance heating is better suited for uniform heating of larger parts.
- Speed: Induction heating is faster due to its direct heating mechanism, whereas resistance heating may take longer to achieve the desired temperature.
- Energy Efficiency: Induction heating is generally more energy-efficient for small-scale or localized applications, while resistance heating is more efficient for large-scale, continuous processes.
- Equipment Complexity: Induction heating systems are more complex and expensive, whereas resistance heating systems are simpler and more cost-effective for many industrial applications.
-
Other Heating Technologies:
- While induction and resistance heating are the most common, other technologies like field-assisted sintering technique (FAST) or direct hot pressing are also used in specialized applications. These methods combine heat and pressure to achieve unique material properties.
-
Heating Elements in Resistance Heating:
- Stainless Steel Tubes: Used for moderate temperature ranges and corrosive environments.
- Resistance Wires: Commonly used in furnaces for their durability and consistent performance.
- Silicon Carbon Rods: Suitable for high-temperature applications due to their excellent thermal stability.
- Graphite and Tungsten Mesh: Used in extreme high-temperature environments, such as in vacuum furnaces.
In summary, induction and resistance heating are the two primary technologies used in heat treatments, each with its own strengths and applications. The choice between them depends on factors like the required precision, heating speed, and the scale of the process. Understanding these technologies helps in selecting the most appropriate method for specific heat treatment needs.
Summary Table:
Aspect | Induction Heating | Resistance Heating |
---|---|---|
How It Works | Electromagnetic induction generates heat | Joule heating via electrical resistance |
Applications | Hardening, annealing, soldering/brazing | Annealing, tempering, normalizing |
Advantages | High precision, fast, energy-efficient | Uniform heating, versatile, batch-friendly |
Precision | Best for localized heating | Best for uniform heating |
Speed | Faster heating | Slower heating |
Energy Efficiency | More efficient for small-scale applications | More efficient for large-scale processes |
Equipment Complexity | More complex and expensive | Simpler and cost-effective |
Need help selecting the right heating technology for your heat treatment process? Contact our experts today for personalized advice!