Porcelain firing under vacuum is a specialized process used to achieve high-quality results in dental and ceramic applications. This method involves placing porcelain materials in a vacuum environment within a porcelain furnace to eliminate air bubbles, ensure uniform heating, and enhance the material's strength and aesthetics. The vacuum environment prevents oxidation, reduces porosity, and allows for precise control over the firing process, resulting in durable and visually appealing porcelain restorations. Below, the key points of this process are explained in detail.
Key Points Explained:
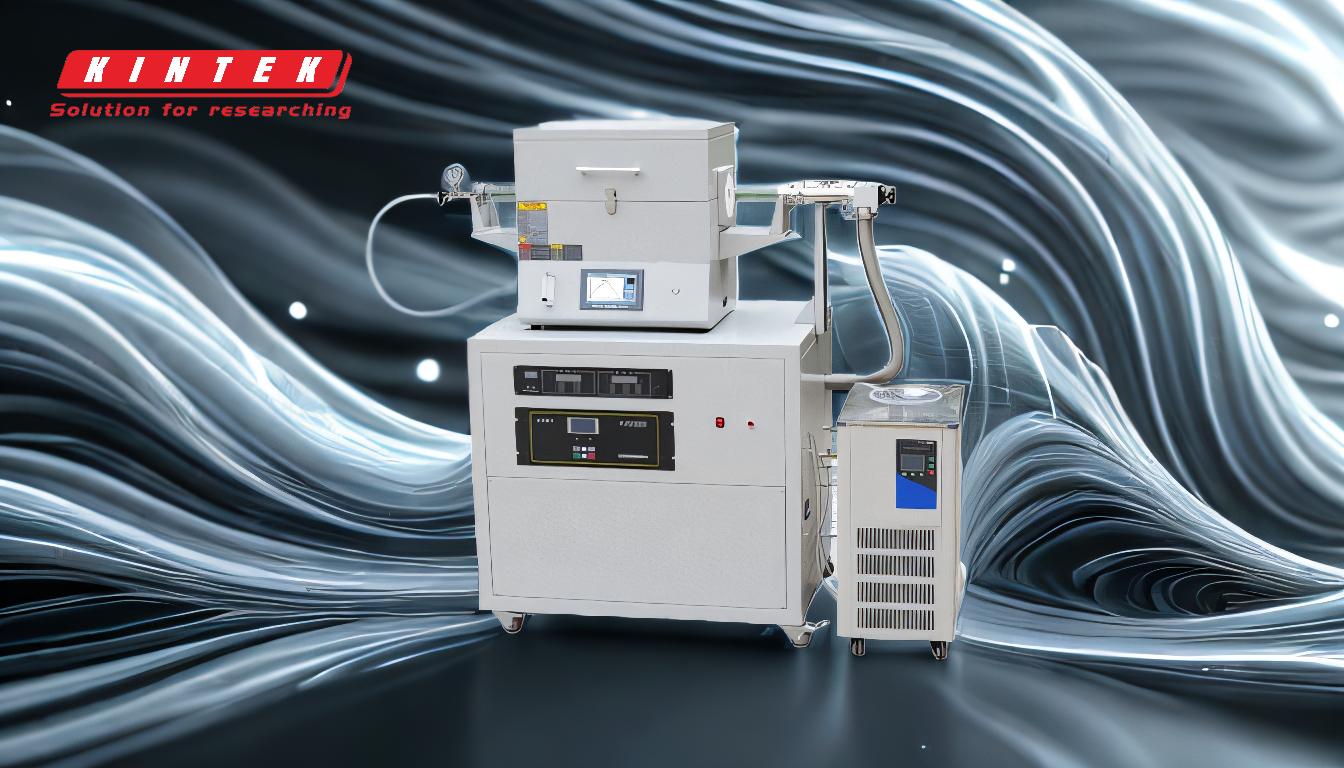
-
Elimination of Air Bubbles:
- Porcelain materials are prone to trapping air bubbles during the firing process, which can weaken the structure and compromise the final product's integrity.
- Firing under vacuum removes these air bubbles by creating a low-pressure environment that forces trapped air out of the material.
- This results in a denser, more homogenous structure, which is critical for dental restorations and high-precision ceramic applications.
-
Uniform Heating:
- A vacuum environment ensures even heat distribution throughout the porcelain material.
- Inconsistent heating can lead to warping, cracking, or uneven sintering, which are detrimental to the final product's quality.
- The controlled environment of a porcelain furnace allows for precise temperature regulation, ensuring uniform thermal expansion and contraction.
-
Prevention of Oxidation:
- Oxidation can discolor porcelain and weaken its structure, particularly in materials containing metal oxides.
- Firing under vacuum minimizes exposure to oxygen, preserving the material's color and structural integrity.
- This is especially important for dental porcelain, where aesthetics and durability are paramount.
-
Reduction of Porosity:
- Porosity in porcelain can lead to micro-cracks and reduced mechanical strength.
- The vacuum firing process compacts the material, reducing porosity and enhancing its overall durability.
- This makes the porcelain more resistant to wear and tear, which is essential for long-lasting dental restorations.
-
Enhanced Aesthetic Quality:
- Vacuum firing produces a smoother surface finish, improving the porcelain's translucency and natural appearance.
- This is crucial for dental applications, where the restoration must closely match the patient's natural teeth in color and texture.
- The process also allows for better control over glaze application, resulting in a more polished and lifelike finish.
-
Improved Bonding with Substrates:
- In dental applications, porcelain must bond securely to metal or ceramic substrates.
- Vacuum firing enhances the bonding process by ensuring a clean, oxide-free interface between the porcelain and the substrate.
- This results in stronger, more reliable restorations that are less likely to fail over time.
-
Precision and Control:
- Modern porcelain furnaces equipped with vacuum capabilities offer advanced programming options for precise control over firing cycles.
- This includes adjustable heating rates, cooling rates, and vacuum levels, allowing technicians to tailor the process to specific materials and applications.
- Such precision ensures consistent results and reduces the likelihood of errors or defects.
In summary, firing porcelain under vacuum in a porcelain furnace is essential for producing high-quality, durable, and aesthetically pleasing results. The process eliminates air bubbles, ensures uniform heating, prevents oxidation, reduces porosity, and enhances bonding, making it indispensable in dental and ceramic industries.
Summary Table:
Benefits of Vacuum Firing | Key Details |
---|---|
Elimination of Air Bubbles | Removes trapped air for a denser, more homogenous structure. |
Uniform Heating | Ensures even heat distribution, preventing warping and cracking. |
Prevention of Oxidation | Minimizes oxygen exposure, preserving color and structural integrity. |
Reduction of Porosity | Compacts material, reducing micro-cracks and enhancing durability. |
Enhanced Aesthetic Quality | Produces smoother surfaces and natural translucency for lifelike results. |
Improved Bonding with Substrates | Ensures strong, reliable bonding with metal or ceramic substrates. |
Precision and Control | Advanced programming for tailored firing cycles and consistent results. |
Unlock the full potential of vacuum firing for your porcelain applications—contact our experts today!