A vacuum is essential for thin-film deposition because it creates an environment that ensures the formation of high-quality, pure, and adherent films. By reducing gas pressure, a vacuum increases the mean free path of vaporized atoms, preventing them from colliding and forming unwanted particles or soot. It also minimizes contamination from impurities like oxygen, nitrogen, and carbon dioxide, which can degrade film quality. Additionally, a vacuum environment allows for precise control of gas and vapor composition, facilitates mass flow control, and supports the creation of a low-pressure plasma environment. These factors collectively enable the deposition of thin films with high purity, strong adhesion, and desired properties.
Key Points Explained:
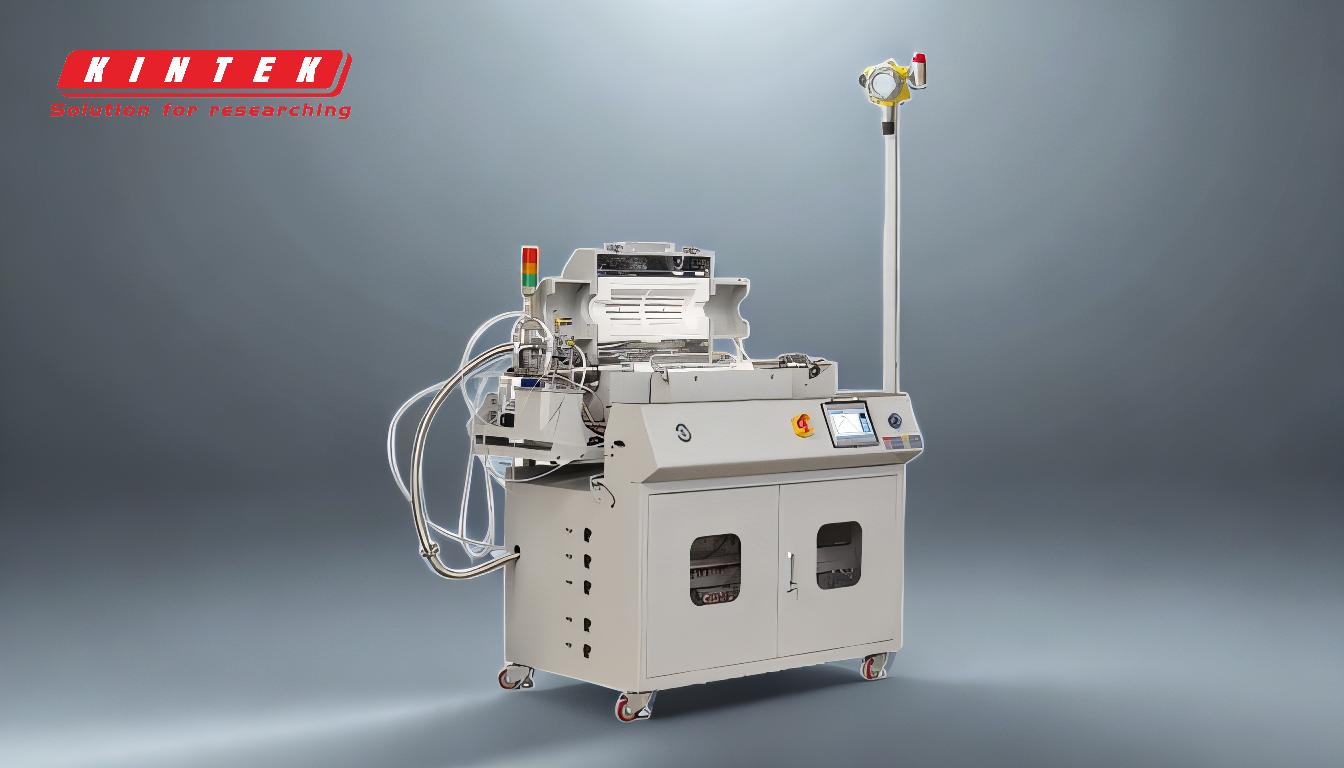
-
Increased Mean Free Path:
- In a vacuum, the gas pressure is significantly reduced, which increases the mean free path of vaporized atoms. The mean free path is the average distance an atom can travel before colliding with another atom or molecule.
- A longer mean free path ensures that vaporized atoms travel directly to the substrate without colliding and forming unwanted particles or soot. This is critical for achieving a uniform and high-quality thin film.
-
Reduction of Contamination:
- A vacuum environment minimizes the presence of contaminants such as oxygen, nitrogen, carbon dioxide, and water vapor. These impurities can react with the film material, leading to defects, poor adhesion, or undesired chemical properties.
- By reducing contamination, the vacuum ensures that the deposited film has high purity and adheres strongly to the substrate, which is essential for applications requiring precise material properties.
-
Control of Gas and Vapor Composition:
- In a vacuum, the composition of gases and vapors within the deposition chamber can be precisely controlled. This allows for the introduction of specific gases or vapors that are necessary for certain deposition processes, such as reactive sputtering or chemical vapor deposition (CVD).
- Controlled gas composition ensures that the film material reacts or deposits in the desired manner, leading to films with tailored properties.
-
Facilitation of Mass Flow Control:
- A vacuum environment enables precise control over the flow of gases and vapors into the processing chamber. This is crucial for processes like atomic layer deposition (ALD) or plasma-enhanced chemical vapor deposition (PECVD), where exact dosing of reactants is required.
- Mass flow control ensures consistent film thickness and composition, which are vital for applications in microelectronics, optics, and coatings.
-
Creation of a Low-Pressure Plasma Environment:
- Many thin-film deposition techniques, such as sputtering and plasma-enhanced deposition, rely on the generation of plasma. A vacuum environment supports the formation of a stable, low-pressure plasma, which is necessary for ionizing gases and enhancing deposition rates.
- Plasma enhances the energy of particles, improving film adhesion and allowing for the deposition of materials at lower temperatures.
-
Prevention of Nucleation in Vapor:
- In the absence of a vacuum, vaporized atoms may collide and nucleate, forming clusters or soot instead of depositing as a thin film. This can lead to non-uniform films with poor mechanical and optical properties.
- A vacuum prevents nucleation by ensuring that atoms travel directly to the substrate, resulting in a smooth and uniform film.
-
High Thermal Evaporation Rate:
- A vacuum environment allows for high thermal evaporation rates, which are necessary for processes like thermal evaporation deposition. The reduced pressure ensures that the evaporated material reaches the substrate without significant loss or scattering.
- This is particularly important for depositing materials with high melting points or for creating films with specific optical or electrical properties.
-
Minimization of Gaseous Contamination:
- By reducing the density of undesirable atoms and molecules, a vacuum ensures that the film material does not bond with contaminants in the air. This is critical for applications requiring high-purity films, such as semiconductor manufacturing or optical coatings.
- Minimizing gaseous contamination also improves the film's mechanical and chemical stability.
-
Strong Adhesion and High Purity:
- A high vacuum environment ensures that the deposited film adheres strongly to the substrate and maintains high purity. This is achieved by eliminating impurities and providing a clean deposition surface.
- Strong adhesion and high purity are essential for films used in demanding applications, such as protective coatings, sensors, and electronic devices.
-
Prevention of Film Degradation:
- Without a vacuum, impurities like oxygen and moisture can react with the film material, causing oxidation, corrosion, or other forms of degradation. This can compromise the film's performance and longevity.
- A vacuum environment prevents such reactions, ensuring that the film retains its desired properties over time.
In summary, a vacuum is indispensable for thin-film deposition because it creates a controlled environment that ensures the formation of high-quality, pure, and adherent films. By addressing factors like contamination, mean free path, and gas composition, a vacuum enables precise and reliable deposition processes critical for advanced applications in various industries.
Summary Table:
Key Benefit | Description |
---|---|
Increased Mean Free Path | Reduces collisions, ensuring uniform and high-quality thin films. |
Reduction of Contamination | Minimizes impurities like oxygen and nitrogen for high-purity films. |
Control of Gas Composition | Enables precise introduction of specific gases for tailored film properties. |
Facilitation of Mass Flow Control | Ensures consistent film thickness and composition for critical applications. |
Low-Pressure Plasma Environment | Supports stable plasma for enhanced deposition rates and adhesion. |
Prevention of Nucleation | Prevents cluster formation, ensuring smooth and uniform films. |
High Thermal Evaporation Rate | Allows efficient deposition of high-melting-point materials. |
Strong Adhesion & High Purity | Ensures films adhere strongly and maintain purity for demanding applications. |
Prevention of Film Degradation | Protects films from oxidation and corrosion, preserving performance over time. |
Ready to achieve high-quality thin-film deposition? Contact us today to learn more about our vacuum solutions!