A vacuum is essential in the deposition of thin films to ensure high-quality, pure, and adherent coatings. The vacuum environment reduces gas pressure, allowing vaporized atoms to travel longer distances without colliding with other particles, which minimizes nucleation and soot formation. It also significantly lowers contamination levels by removing unwanted substances like oxygen, nitrogen, and carbon dioxide, which can interfere with film formation, weaken adhesion, or introduce impurities. Additionally, the vacuum enables precise control over gas and vapor composition, facilitates a low-pressure plasma environment, and ensures efficient mass flow control, all of which are critical for achieving consistent and high-performance thin films.
Key Points Explained:
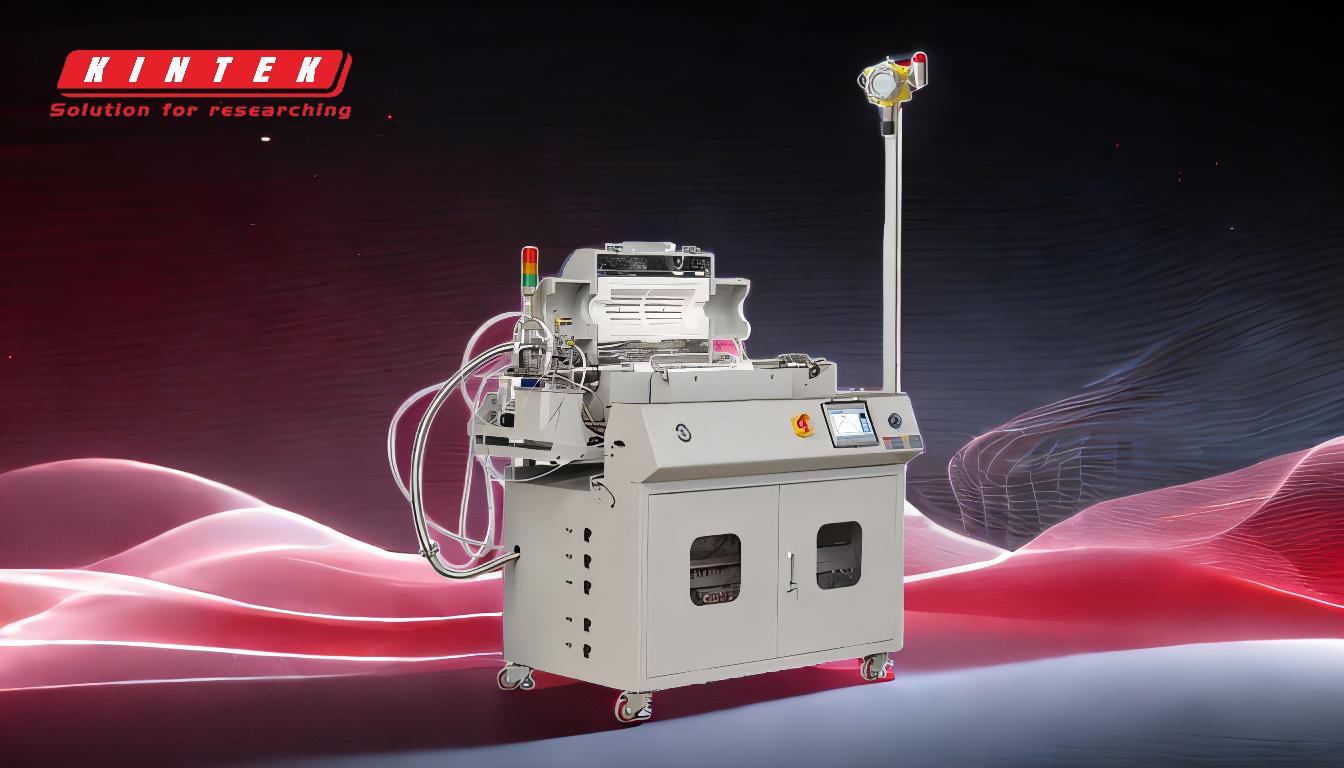
-
Reduction of Gas Pressure for Longer Mean-Free Path:
- In a vacuum, the gas pressure is significantly reduced, allowing vaporized atoms or molecules to travel longer distances without colliding with other particles. This longer mean-free path ensures that the particles can reach the substrate without forming unwanted clusters or soot, which would degrade the quality of the thin film.
- Without a vacuum, the high density of gas molecules would cause frequent collisions, leading to nucleation and the formation of particulate matter, which can contaminate the film.
-
Minimization of Contamination:
- A vacuum environment drastically reduces the presence of contaminants such as oxygen, nitrogen, carbon dioxide, and water vapor. These contaminants can react with the film material, leading to impurities, oxidation, or other chemical reactions that compromise the film's properties.
- For example, oxygen can oxidize metal films, while water vapor can introduce hydrogen or hydroxyl groups, altering the film's electrical or optical properties.
-
Control of Gas and Vapor Composition:
- A vacuum allows precise control over the composition of gases and vapors in the deposition chamber. This is crucial for processes like chemical vapor deposition (CVD) or plasma-enhanced CVD, where specific gas mixtures are required to achieve the desired film properties.
- By maintaining a controlled environment, the deposition process can be fine-tuned to produce films with specific characteristics, such as conductivity, transparency, or hardness.
-
Facilitation of Low-Pressure Plasma Environment:
- Many thin film deposition techniques, such as sputtering or plasma-enhanced deposition, rely on a low-pressure plasma to ionize gases and create reactive species. A vacuum is necessary to sustain this plasma, as it requires a low particle density to function effectively.
- The plasma enhances the energy of the particles, improving film adhesion and uniformity.
-
Enabling High Thermal Evaporation Rates:
- In physical vapor deposition (PVD) techniques like thermal evaporation, a vacuum ensures that the material being evaporated can reach the substrate without being obstructed by gas molecules. This results in a high deposition rate and a dense, uniform film.
- The absence of gas molecules also prevents scattering of the vaporized material, ensuring that it deposits directly onto the substrate.
-
Enhancing Film Purity and Adhesion:
- A high vacuum ensures that the film material bonds directly to the substrate without interference from contaminants. This results in a film with high purity and strong adhesion, which is critical for applications requiring durability and performance.
- Impurities or weak adhesion can lead to delamination, reduced conductivity, or other failures in the final product.
-
Mass Flow Control and Process Consistency:
- A vacuum environment allows for precise control of the mass flow of gases and vapors into the deposition chamber. This ensures consistent process conditions, which are essential for producing uniform thin films with reproducible properties.
- Variations in pressure or gas composition can lead to defects or inconsistencies in the film, making vacuum control a key factor in achieving high-quality results.
In summary, the use of a vacuum in thin film deposition is critical for ensuring the purity, uniformity, and performance of the deposited films. It minimizes contamination, controls the deposition environment, and enables precise process control, all of which are essential for producing high-quality thin films for a wide range of applications.
Summary Table:
Key Benefit | Explanation |
---|---|
Reduction of Gas Pressure | Allows vaporized atoms to travel longer distances, minimizing nucleation and soot. |
Minimization of Contamination | Removes unwanted substances like oxygen, nitrogen, and carbon dioxide. |
Control of Gas and Vapor Composition | Enables precise control for processes like CVD and plasma-enhanced deposition. |
Low-Pressure Plasma Environment | Facilitates plasma-enhanced deposition for better film adhesion and uniformity. |
High Thermal Evaporation Rates | Ensures dense, uniform films in PVD techniques like thermal evaporation. |
Enhanced Film Purity and Adhesion | Bonds film material directly to the substrate, ensuring high purity and strength. |
Mass Flow Control and Process Consistency | Maintains consistent process conditions for reproducible thin film properties. |
Need high-quality thin films for your applications? Contact our experts today to learn more!