A muffle furnace is a specialized heating device used in laboratories, industries, and research settings for high-temperature processes. Its primary purpose is to heat materials uniformly and without contamination, making it ideal for applications like heat treatment, material analysis, and chemical processes. The furnace's unique design separates the heating chamber from combustion byproducts, ensuring a clean environment for sensitive experiments. It is widely used for annealing, sintering, glass fusing, and elemental analysis, among other processes. With its ability to reach temperatures up to 1400°C and provide consistent heat distribution, the muffle furnace is an essential tool for precision and reliability in high-temperature applications.
Key Points Explained:
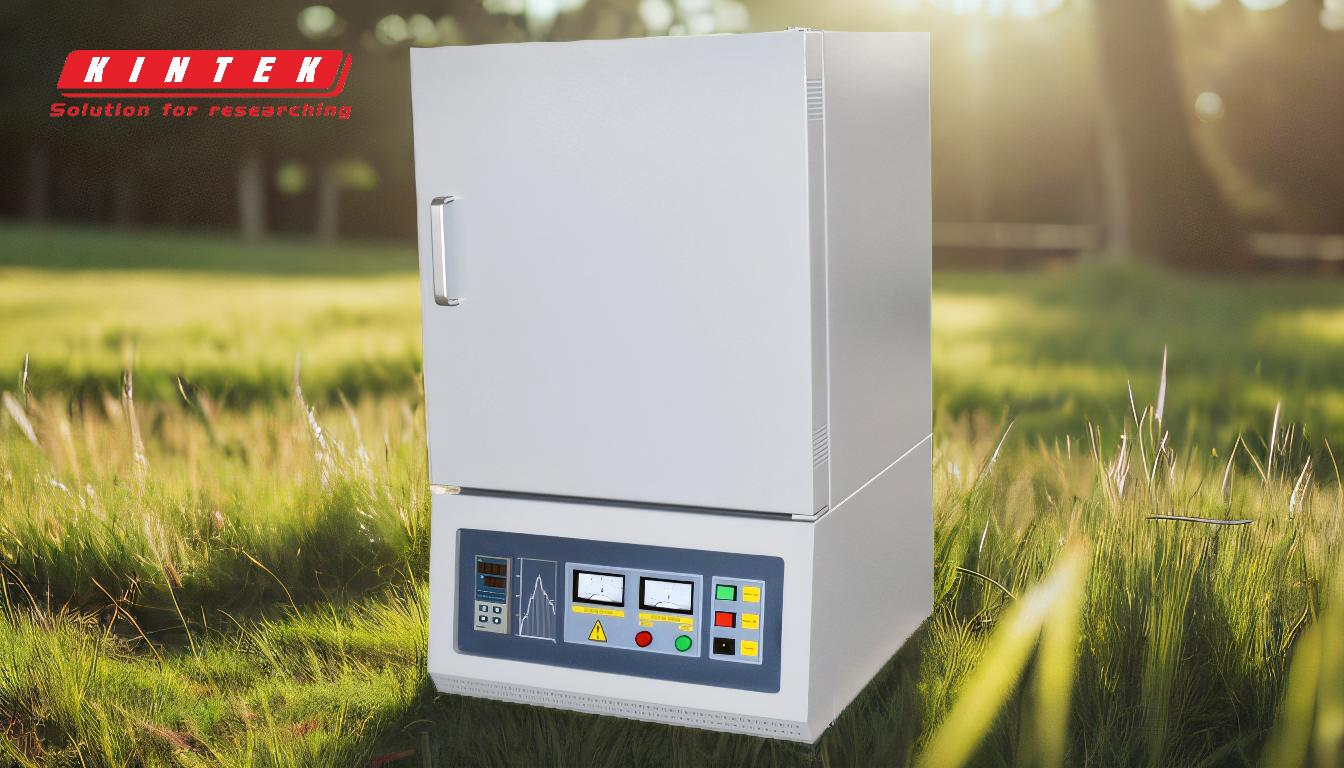
-
Contamination-Free Heating:
- The defining feature of a muffle furnace is its ability to heat materials without exposing them to combustion byproducts like gases, ash, or residue. This is achieved by separating the heating chamber from the heat source, ensuring a clean environment. This makes it ideal for scientific research and material analysis, where contamination could skew results.
-
High-Temperature Capabilities:
- Muffle furnaces can reach temperatures up to 1400°C, making them suitable for a wide range of high-temperature applications. These include processes like fusing glass, creating enamel coatings, and sintering ceramics. The high thermal conductivity of the furnace's materials ensures efficient heat transfer and uniform treatment of workpieces.
-
Versatility in Applications:
- Muffle furnaces are used in diverse fields, including metallurgy, ceramics, and materials science. Common applications include:
- Heat Treatment: Processes like annealing, hardening, and tempering of metals.
- Material Analysis: Detecting elements in coal or other materials.
- Industrial Processes: Sintering, brazing, and metallizing.
- Muffle furnaces are used in diverse fields, including metallurgy, ceramics, and materials science. Common applications include:
-
Uniform Heat Distribution:
- The furnace uses a combination of radiant and convection heat transfer to ensure homogeneous heating. This is crucial for processes requiring consistent temperature control, such as creating technical ceramics or reducing metal powders.
-
Dual-Chamber Design:
- Modern muffle furnaces feature two chambers separated by an air gap. The top chamber acts as the reaction vessel, while the bottom chamber allows for easy removal of processed materials. This design enhances efficiency and safety during high-temperature operations.
-
Energy Efficiency and Safety:
- The furnace's insulated construction and mechanical convection system minimize heat loss and direct airflow out of an exhaust muffle. This eliminates the need for a fume hood in many cases, making it a safer and more energy-efficient option for high-temperature applications.
-
Material Compatibility:
- Muffle furnaces are constructed from heat-resistant materials with high thermal conductivity, ensuring durability and performance. They can process a variety of materials, including low-carbon steel, stainless steel, copper, and ceramics.
-
Precision and Control:
- The electrically powered design of muffle furnaces allows for precise temperature control, which is essential for processes like glass formation or soldering. This precision ensures repeatability and reliability in research and industrial settings.
In summary, the muffle furnace is a versatile and indispensable tool for high-temperature processes, offering contamination-free heating, uniform temperature distribution, and precise control. Its applications span across industries, making it a critical asset for laboratories, manufacturing, and research institutions.
Summary Table:
Feature | Description |
---|---|
Contamination-Free Heating | Separates heating chamber from combustion byproducts for clean, precise results. |
High-Temperature Capability | Reaches up to 1400°C, ideal for glass fusing, sintering, and material analysis. |
Uniform Heat Distribution | Ensures consistent temperature for processes like annealing and ceramics. |
Versatile Applications | Used in heat treatment, material analysis, and industrial processes. |
Energy Efficiency | Insulated design minimizes heat loss, enhancing safety and reducing energy use. |
Material Compatibility | Works with low-carbon steel, stainless steel, copper, and ceramics. |
Precision Control | Electrically powered for accurate temperature regulation in critical processes. |
Ready to enhance your lab's capabilities? Contact us today to learn more about muffle furnaces!