Argon is widely used in furnaces due to its inert properties, making it an ideal choice for creating non-reactive environments. It prevents oxidation and contamination during high-temperature processes, ensuring the purity and quality of materials. While argon is more expensive than other gases, its benefits in maintaining material integrity often outweigh the cost. This gas is particularly valuable in industries like aerospace and manufacturing, where precision and material quality are critical. Below, we explore the key reasons for using argon in furnaces and its applications.
Key Points Explained:
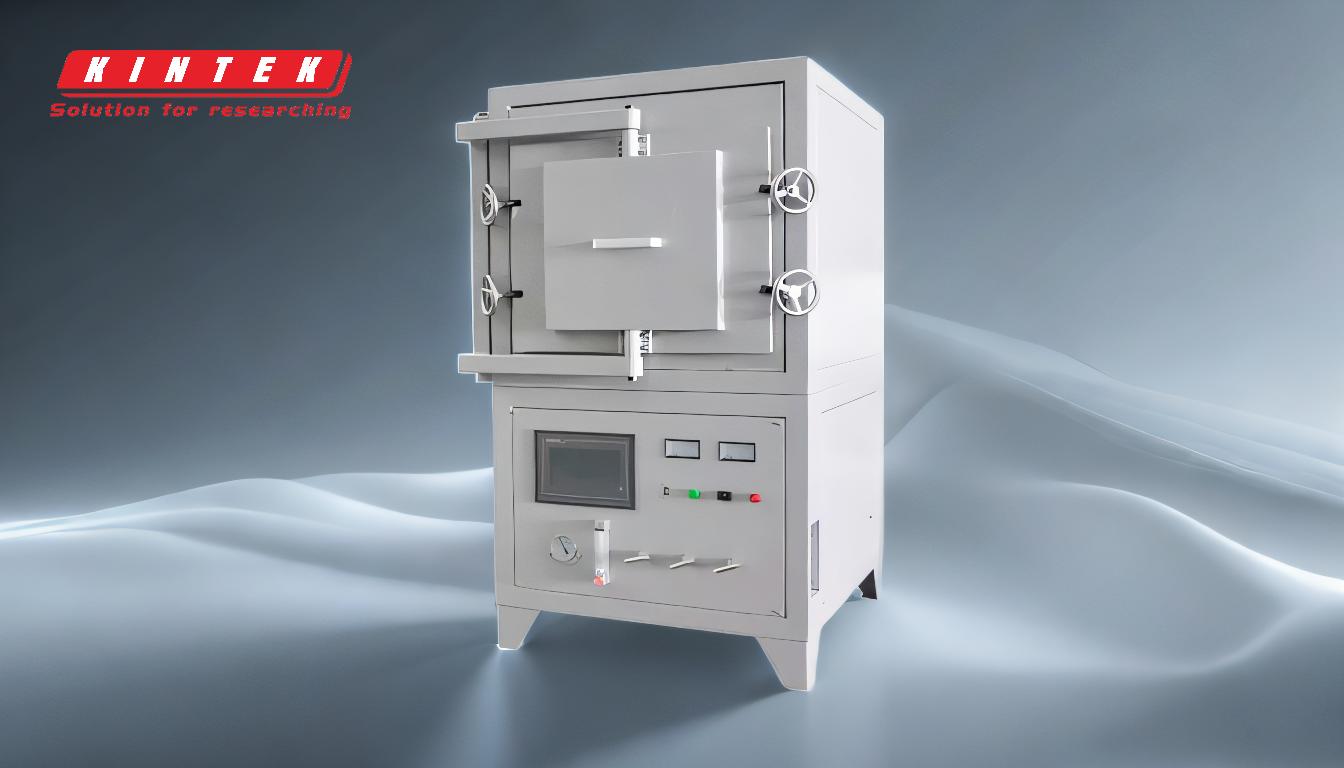
-
Inert Nature of Argon:
- Argon is a noble gas, meaning it is chemically inert and does not react with other elements or compounds. This property is crucial in furnace applications, as it prevents unwanted chemical reactions, such as oxidation, during high-temperature processes.
- In processes like heat treatment or metal fabrication, argon ensures that the metal surfaces remain uncontaminated, preserving their mechanical and chemical properties.
-
Applications in High-Temperature Processes:
- Argon is commonly used in furnaces for processes like annealing, sintering, and brazing. These processes require a controlled atmosphere to prevent oxidation or degradation of materials.
- For example, in the aerospace industry, argon is used to protect titanium and other reactive metals during heat treatment, ensuring the final product meets stringent quality standards.
-
Role in PVD (Physical Vapor Deposition) Processes:
- In PVD processes, argon is used to create a non-reactive environment within the vacuum chamber. This ensures that the coating material remains pure as it transitions into the vapor phase and deposits onto the substrate.
- The inert nature of argon prevents contamination, which is critical for achieving high-quality coatings in industries like electronics and optics.
-
Thermal Insulation Properties:
- While not directly related to furnaces, argon's thermal insulation properties are worth noting. In double-glazed windows, argon is used to fill the space between panes, reducing heat transfer and improving energy efficiency.
- This principle of thermal insulation can be extrapolated to furnace applications, where argon helps maintain consistent temperatures and reduces energy consumption.
-
Cost Considerations:
- Argon is more expensive than other gases like nitrogen, which can be a drawback for some applications. However, its unique properties often justify the cost, especially in industries where material purity and quality are paramount.
- For cost-sensitive applications, a mix of argon and other gases may be used to balance performance and expense.
-
Detection and Usage Verification:
- In some applications, such as double-glazed windows, the presence of argon can be verified by checking for small holes in the spacer material, which are used to pump argon into the space between panes.
- While this is specific to windows, it highlights the importance of ensuring proper argon usage in various applications to achieve desired outcomes.
In summary, argon's inertness, ability to maintain material purity, and thermal properties make it a valuable gas for furnace applications. Despite its higher cost, its benefits in ensuring high-quality results in critical processes make it a preferred choice in many industries.
Summary Table:
Key Reason | Description |
---|---|
Inert Nature | Prevents oxidation and contamination during high-temperature processes. |
High-Temperature Applications | Used in annealing, sintering, and brazing to maintain material integrity. |
PVD Processes | Ensures pure coatings in electronics and optics by creating non-reactive environments. |
Thermal Insulation | Helps maintain consistent temperatures and reduces energy consumption. |
Cost vs. Benefits | Higher cost justified by superior material quality and process outcomes. |
Learn how argon can enhance your furnace processes—contact our experts today!