Argon is often preferred over nitrogen in specific applications due to its unique properties, such as being denser and completely inert. This makes it ideal for environments where preventing oxygen contamination is critical, such as in aerospace or metalworking industries. While nitrogen is also inert and widely used, argon's higher density and non-reactivity with metal surfaces make it a better choice in scenarios where absolute inertness is required. However, its higher cost can be a limiting factor. Below, we explore the key reasons why argon is chosen over nitrogen in detail.
Key Points Explained:
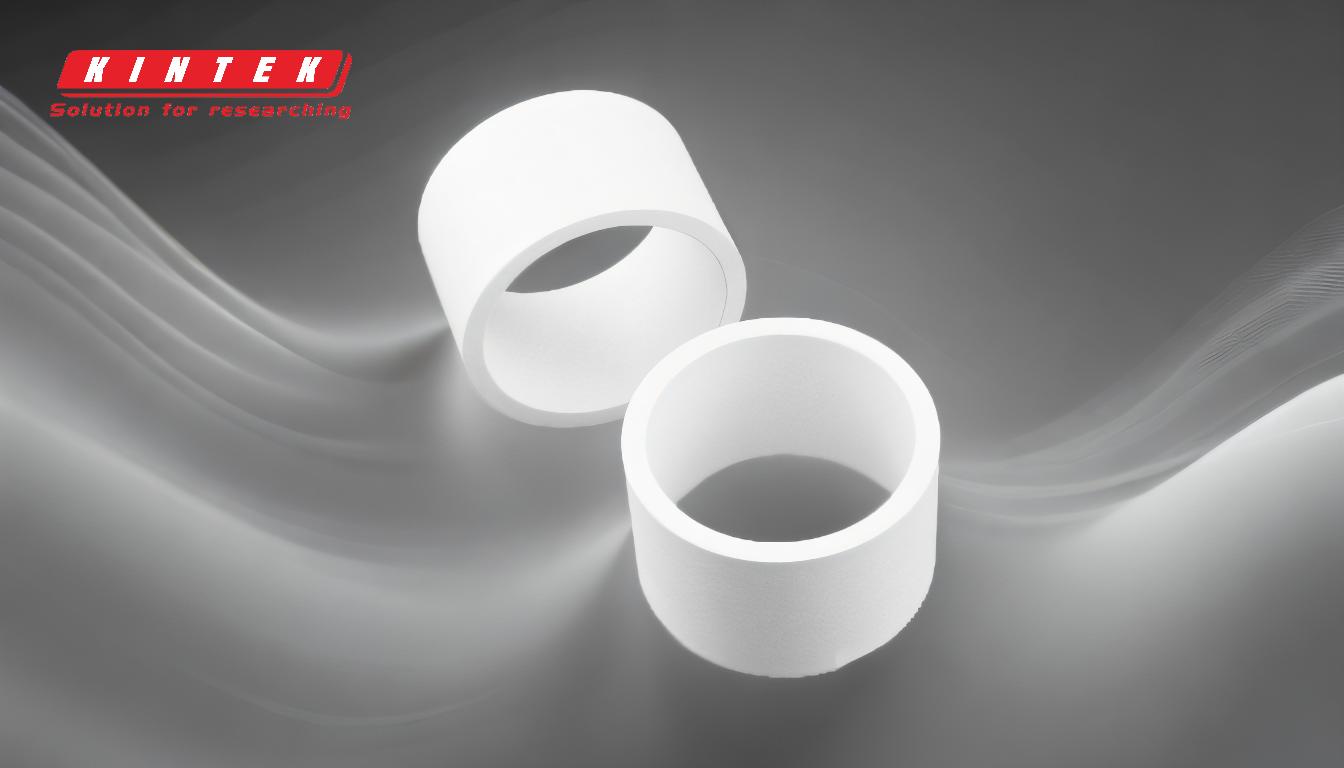
-
Inertness of Argon:
- Argon is a noble gas, meaning it is completely inert and does not react with other substances, including metals. This makes it ideal for applications where maintaining a non-reactive atmosphere is crucial, such as in welding or metal fabrication.
- Nitrogen, while also inert, can form nitrides under certain high-temperature conditions, which may not be desirable in sensitive processes.
-
Density Advantage:
- Argon is denser than nitrogen, which means it can create a more effective barrier against oxygen and other reactive gases. This is particularly important in applications like purging or shielding, where preventing oxygen ingress is critical.
- The higher density of argon makes it slower to disperse, providing longer-lasting protection compared to nitrogen.
-
Applications in Aerospace and Metalworking:
- In the aerospace industry, argon is often used to create a non-reactive environment for welding and manufacturing components. Its inertness ensures that metal surfaces remain uncontaminated during these processes.
- Similarly, in metalworking, argon is preferred for processes like TIG (Tungsten Inert Gas) welding, where even minor reactions with the metal can compromise the quality of the weld.
-
Cost Considerations:
- While argon offers superior performance in many applications, it is more expensive than nitrogen. This cost difference can be a significant factor in industries where large volumes of gas are required.
- Nitrogen is often chosen for less critical applications where its lower cost and adequate performance make it a more economical option.
-
Specific Use Cases for Argon:
- Argon is particularly useful in processes like purging pipelines or tanks, where its density ensures that oxygen is effectively displaced and does not re-enter the system.
- It is also used in specialized applications like semiconductor manufacturing, where even trace amounts of oxygen or other reactive gases can cause defects.
In summary, argon is preferred over nitrogen in situations where its inertness and density provide a clear advantage, such as in high-precision welding, aerospace manufacturing, and other critical applications. However, the higher cost of argon means that nitrogen remains a viable alternative for less demanding scenarios.
Summary Table:
Aspect | Argon | Nitrogen |
---|---|---|
Inertness | Completely inert; no reactions with metals or other substances. | Inert but can form nitrides under high temperatures. |
Density | Denser, providing a stronger barrier against oxygen and reactive gases. | Less dense, disperses faster than argon. |
Applications | Aerospace, metalworking, TIG welding, semiconductor manufacturing. | Less critical applications where cost is a priority. |
Cost | More expensive due to superior performance. | More economical for large-scale or less demanding uses. |
Need help choosing the right gas for your application? Contact our experts today for tailored advice!