Deposition chambers, particularly in Physical Vapor Deposition (PVD) processes, operate under high vacuum conditions to ensure optimal material deposition. This environment minimizes contamination, allows for precise control over the deposition process, and ensures that the material adheres firmly to the substrate. High vacuum conditions are essential for processes like microchip manufacturing, where even minor contamination can lead to significant defects. The vacuum environment also increases the mean free path of atoms, enabling efficient material transfer and high thermal evaporation rates.
Key Points Explained:
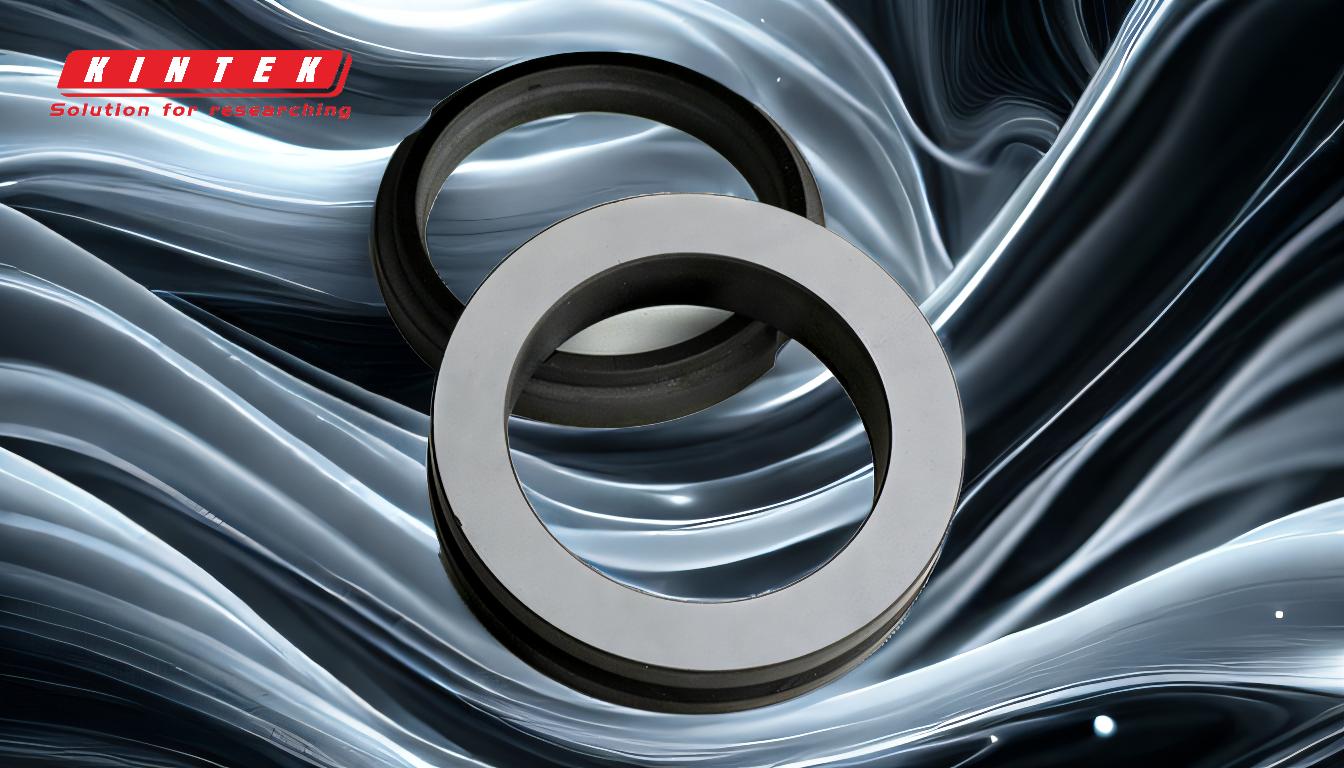
-
Minimizing Contamination:
- A high vacuum environment significantly reduces the presence of unwanted atoms and molecules, which could otherwise contaminate the deposition process. This is crucial for applications like microchip manufacturing, where even tiny particles can cause defects. The high vacuum ensures a clean environment, free from dust, moisture, and other contaminants that could interfere with the deposition process.
-
Increasing Mean Free Path:
- In a high vacuum, the density of atoms and molecules is drastically reduced, increasing the mean free path of the particles involved in the deposition process. This means that atoms or molecules can travel longer distances without colliding with other particles, ensuring that they reach the substrate with sufficient energy to adhere firmly. This is particularly important for achieving uniform and high-quality coatings.
-
Enabling High Thermal Evaporation Rates:
- High vacuum conditions allow for higher thermal evaporation rates, which are essential for efficient material transfer. In a vacuum, materials can be heated to high temperatures without the risk of oxidation or other unwanted chemical reactions. This ensures that the material evaporates uniformly and deposits smoothly onto the substrate.
-
Facilitating Controlled and Repeatable Processes:
- A high vacuum environment provides a controlled and repeatable setting for deposition processes. By eliminating variables such as air pressure and contamination, manufacturers can achieve consistent results across multiple batches. This is particularly important in industries like semiconductor manufacturing, where precision and consistency are critical.
-
Preventing Chemical Reactions (Unless Desired):
- In PVD processes, the high vacuum environment prevents unwanted chemical reactions, ensuring that the deposited material remains pure. However, if a chemical reaction is desired—such as the introduction of oxygen to create oxide coatings—the vacuum environment can be adjusted to allow for controlled reactions. This flexibility is a key advantage of high vacuum deposition chambers.
-
Supporting Advanced Manufacturing Applications:
- High vacuum conditions are essential for advanced manufacturing applications, such as the production of microchips, CDs, and DVDs. These processes require an extremely clean environment to ensure that the final products are free from defects. The high vacuum environment in deposition chambers is critical for meeting the stringent quality standards required in these industries.
In summary, the high vacuum environment in deposition chambers is essential for minimizing contamination, increasing the mean free path of particles, enabling high thermal evaporation rates, and facilitating controlled and repeatable processes. These factors collectively ensure high-quality material deposition, making high vacuum conditions indispensable in advanced manufacturing and PVD processes.
Summary Table:
Key Benefit | Explanation |
---|---|
Minimizing Contamination | Reduces unwanted atoms and molecules, ensuring a clean environment for deposition. |
Increasing Mean Free Path | Allows particles to travel longer distances without collisions, ensuring firm adhesion. |
Enabling High Thermal Evaporation Rates | Ensures efficient material transfer and uniform deposition. |
Facilitating Controlled Processes | Provides a repeatable environment for consistent results across batches. |
Preventing Unwanted Reactions | Maintains material purity while allowing controlled reactions if needed. |
Supporting Advanced Applications | Essential for microchip manufacturing and other high-precision industries. |
Learn how high vacuum deposition chambers can enhance your manufacturing process—contact us today!